Asset Management in Construction: All You Need to Know
Streamlined asset management in construction prevents unplanned breakdowns and safety risks by regularly monitoring your valuables. Learn more here.
In this article:
- What Is Asset Management in Construction?
- Importance of Asset Management in Construction
- Benefits of Using Asset Management in Construction
- 1. Optimized Resource Allocation
- 2. Reduced Downtime and Delays
- 3. Improved Safety on Job Sites
- 4. Data-Driven Decision Making
- Asset Management in Construction Examples
- 1. Tracking Heavy Machinery Usage
- 2. Inventory Management for Construction Materials
- 3. Theft Prevention and Tool Tracking
- Conclusion
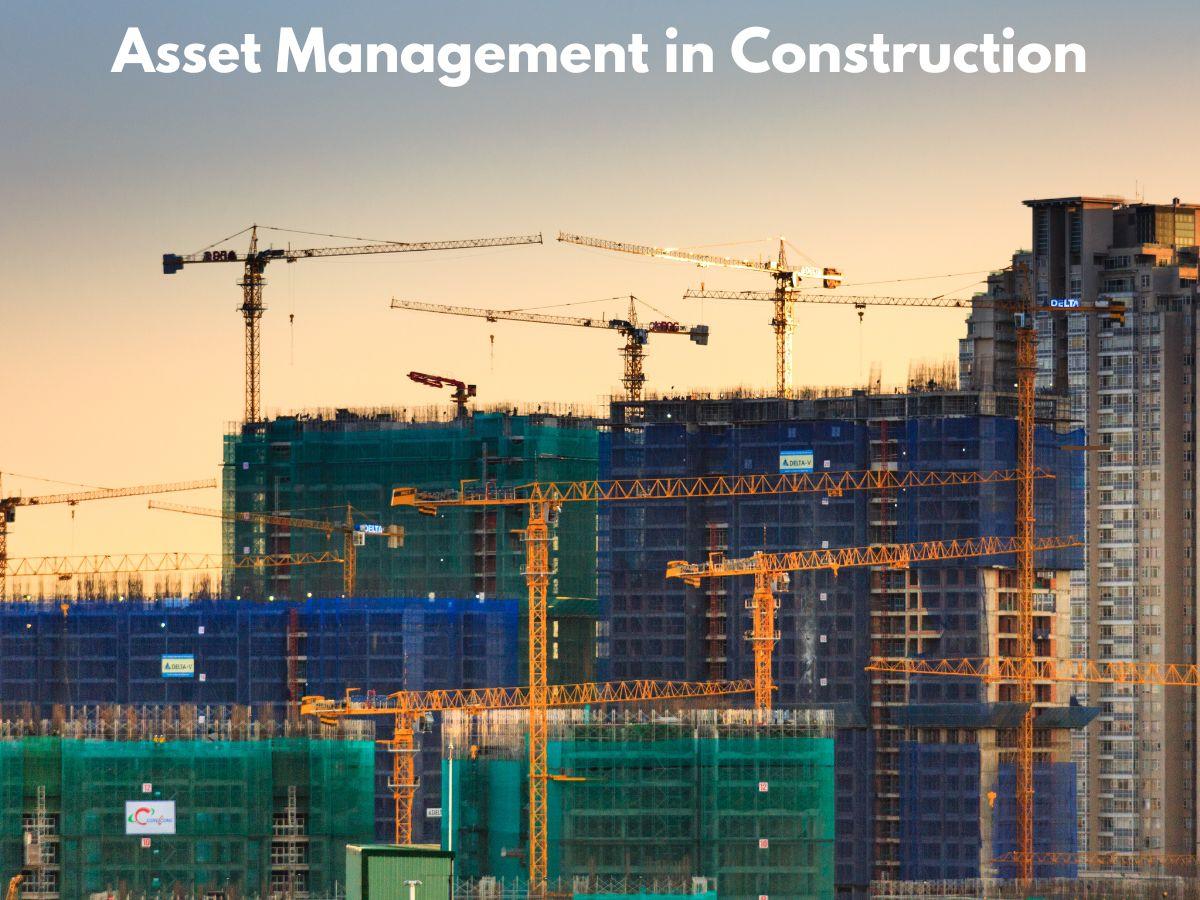
To run a successful construction business, you need three things: skilled labor, reliable materials, and ofcourse, smooth asset management. While most companies prioritize the first two, not many focus on the health and well-being of their assets. This leads to unplanned breakdowns, missed deadlines, and lost productivity, besides risking your worker’s safety.
Asset management in construction refers to the systematic process of tracking, maintaining, and optimizing the use of assets throughout their lifecycle. It ensures that companies get the best return on assets by maximizing asset value while minimizing surprise breakdowns and machine failures. Here’s a detailed guide on construction asset management to help you learn more!
What Is Asset Management in Construction?
The success of a construction company relies on its assets — the resources necessary for smooth project execution. But, how to supervise and govern these resources to optimize their health and longevity? Smooth asset management in construction is the answer.
It refers to the process of keeping track of all the equipment and materials a company uses on a job site. These assets include everything from heavy machinery like bulldozers and cranes to drills, generators, and building materials. The main purpose of construction asset tracking is to make sure these valuables are always in good working condition and available when needed.
With the asset management market set to grow 36.4% by 2030, it’s clear that more companies are recognizing the importance of effective asset management. It not only keeps your projects running smoothly but helps avoid unexpected equipment repairs while improving safety on the work site.
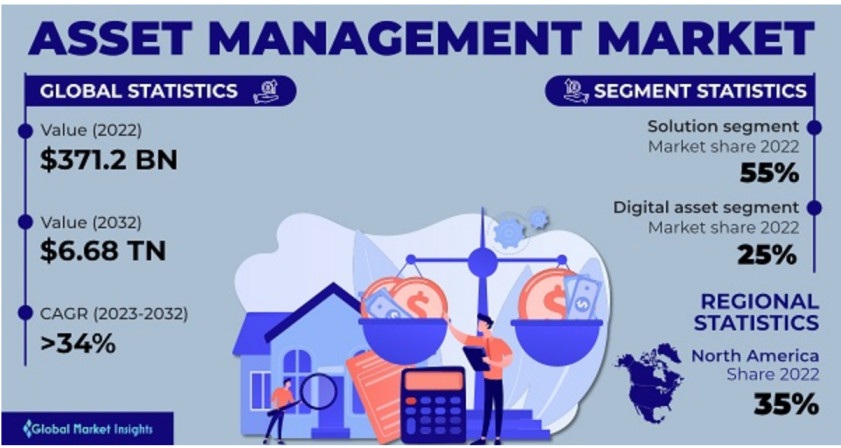
Source: GMInsights
Importance of Asset Management in Construction
Asset management in construction is directly related to the success and smooth execution of any project plan. It involves overseeing all the equipment, machinery, and materials a company uses in its daily operations. In other words, managing assets is all about keeping tabs on the location, condition, and usage of these valuables to ensure they’re always available and well-maintained.
Unplanned downtime costs companies more than you think, causing industrial manufacturers to lose up to $50 billion a year. The leading causes of this include ageing equipment (34%), lack of time for maintenance (9%), and mechanical failure (20%).
Such instances can be prevented with a smooth construction equipment asset management plan, which helps companies stay on top of their maintenance schedules. It also notifies you to replace aged equipment so you don’t have to deal with mechanical failures on-site.
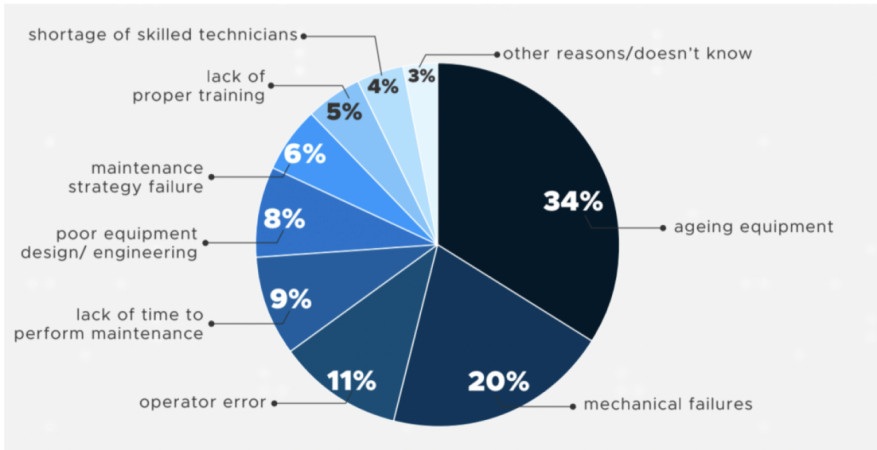
Source: InfraSpeak
Benefits of Using Asset Management in Construction
Considering the heavy-duty equipment used in construction projects like forklifts and tower cranes, companies cannot afford to overlook asset management. After all, poorly managed assets lead to deadline extensions and safety risks, both of which can negatively affect your bottom line. Here are the benefits of using asset management in construction.
1. Optimized Resource Allocation
Without solid asset management in construction, it’s easy to misallocate, or overuse resources, which results in project delays and inefficiencies. As per research, poor resource management is the leading cause of schedule slippage and cost overruns in projects.
However, using paid or even free asset-tracking software allows companies to obtain maximum value from their assets through real-time tracking, maintenance reminders, and resource visibility. The asset management software shows which assets are underutilized or are taking up storage space without generating any return, helping you balance workloads. This reduces wastage and increases the return on investment.
2. Reduced Downtime and Delays
A pause in the production line causes an average manufacturer to lose $22,000 per minute. These surprise failures can be prevented through asset management, which includes real-time tracking of equipment health and regular maintenance schedules. The importance of asset management in construction lies in its ability to help managers identify inefficiencies early on. This reduces downtime and keeps projects on schedule.
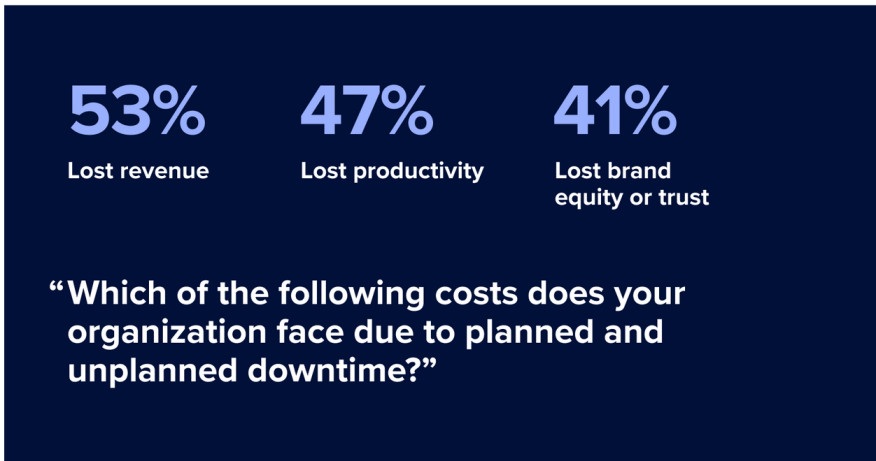
Source: RingCentral
3. Improved Safety on Job Sites
At high-risk construction sites, safety is a top priority — and asset management directly contributes to a safer work environment. When your assets are regularly maintained and checked, the risk of equipment short circuits and workplace incidents decreases. It also ensures that all machinery and equipment are in proper working order, reducing the chances of malfunctioning.
4. Data-Driven Decision Making
Besides improving safety on job sites, asset lifecycle management in construction promotes data-based decision-making for managers. Managers can regularly track the usage, performance, and maintenance history of each asset, enabling them to spot problems in operations. This data-based strategy helps construction units follow a proactive approach, improve planning, and make strategic decisions about their assets.
Asset Management in Construction Examples
If you want to improve the productivity of your onside equipment while minimizing costs, smooth asset management is the best approach. Let's look at a few asset management in construction examples to see how it is applied within the industry.
1. Tracking Heavy Machinery Usage
Let's say you have a large-scale construction site that requires cranes, excavators, and bulldozers. Asset management tools can monitor how often each machine is used, which helps managers identify underutilized equipment. For example, if a crane is only used for 20 hours a week on one site but is in high demand on another, the system can flag this for relocation.
2. Inventory Management for Construction Materials
Inventory asset management is a must for projects that involve building a large commercial structure. It helps keep track of construction materials like concrete, steel beams, and insulation, thereby helping teams restock just in time. The system also monitors the volume of each material available, its storage location, and the expected reorder time to avoid shortages.
3. Theft Prevention and Tool Tracking
Construction sites are an attractive target for theft due to their high-cost assets. Fortunately, now companies can solve this issue by monitoring tools via tagging each piece of equipment with a GPS tracker or barcode and logging it into the asset management system. This way, if a tool is being used without authorization, the system can flag this, thereby preventing theft.
Conclusion
Smooth asset management in the construction industry is the secret to streamlined operations and increased onsite productivity. This practice gives you a real-time view of your asset’s location, usage, and performance patterns, guiding data-backed decisions. It also ensures the proper utilization of resources, which saves long-term expenses.
To maintain a competitive edge in the construction industry, having powerful construction asset management software is a must. This is where Itefy Equipment and Asset Management Software comes in. It offers an ideal solution for construction companies to organize, track, and maintain equipment on the go. Plus, with real-time tracking and maintenance schedule, you can bid farewell to the risk of equipment loss!
Try now and safeguard your assets for the future.
Frequently Asked Questions
-
Asset management in project management refers to tracking and optimizing the use of a company’s resources to minimize downtime and mechanical failures. It helps to make the best use of available resources for a project, thereby reducing delays and unexpected costs.
-
A construction asset manager manages a company’s assets, including machinery, equipment, and tools, throughout their lifecycle. They track the performance of assets, maintenance schedules, and compliance with safety standards to ensure maximum productivity on site.