Optimize Manufacturing Resources with Advanced Equipment Management Software
Are you struggling to keep track of your manufacturing resources? Itefy is here to help you out with its equipment management software. Learn how it can help.
In this article:
- Why Itefy is the Perfect Solution for Manufacturing Resource Management?
- 1. Streamline Equipment and Resource Oversight
- 2. Minimize Downtime with Proactive Management
- 3. Optimize Operations for Maximum Productivity
- Itefy Key Features and How They Transform Manufacturing
- 1. Advanced Equipment Tracking
- 2. Real-Time Location Monitoring
- 3. Simplified Equipment Reservations
- 4. QR Code Scanning for Accurate Tracking
- 5. Maintenance Scheduling and Alerts
- How to Use Itefy for Optimizing Manufacturing Resources
- 1. Create an Account
- 2. Set Up Your Equipment Database
- 3. Plan and Track Reservations
- 4. Monitor And Analyze Items
- 5. Create QR Code Labels
- 6. Creating and Viewing Checkouts
- Take Control of Your Manufacturing Resources Today
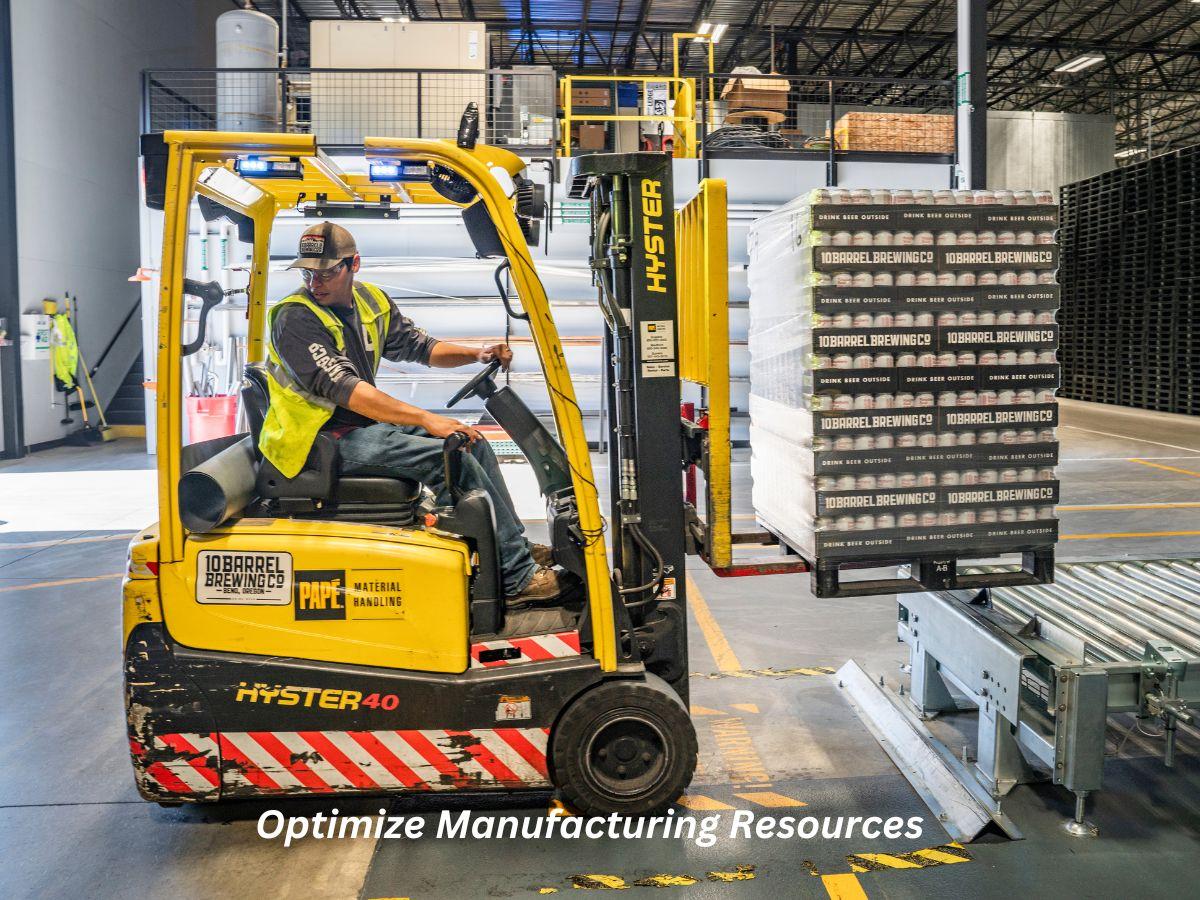
Are you tired of unexpected equipment failures and production delays? Many manufacturers struggle with managing their resources effectively which leads to wasted time, higher costs and endless stress. Without the right tools, it’s tough to keep operations running smoothly and avoid downtime.
That’s where Itefy comes in to help companies optimize their manufacturing resources while keeping the downtime to a minimum. With our advanced equipment management software, you can easily track and monitor your assets in real-time, identify underutilized equipment and reallocate resources to enhance productivity.
Itefy ensures that everyone on your team is on the same page with a centralized database for all your manufacturing resources.
Why Itefy is the Perfect Solution for Manufacturing Resource Management?
Did you know that unplanned downtime costs manufacturers an estimated $50 billion every year? This is why it’s important to actively monitor your manufacturing resources or you’ll be one of the companies facing this huge loss.
Itefy addresses these very challenges head-on and streamlines resource tracking, minimizes downtime and optimizes operations. Here’s a detailed look at these three benefits:
1. Streamline Equipment and Resource Oversight
Managing large inventories of manufacturing tools and equipment is a significant challenge for most companies. You’ll be surprised to know that businesses lose 11% of their revenue because of poor inventory management. However, Itefy solves this problem by providing a centralized database with advanced search and filtering capabilities. With Itefy, you can:
- Quickly locate tools and equipment using specific filters like type, location, or availability.
- Utilize QR code integration to instantly retrieve detailed equipment information. This reduces search times by 60% on average.
- Track equipment across multiple locations, ensuring full visibility and accountability for all assets.
2. Minimize Downtime with Proactive Management
Unplanned downtime costs manufacturers millions in losses. But, with Itefy’s proactive management features, this can become a worry of the past. This software helps prevent disruptions by offering:
- Real-time tracking of equipment usage, condition, and location.
- Automated alerts for overdue checkouts, upcoming maintenance, or unresolved issues.
- The ability to assign primary responsibility for equipment to ensure accountability.
3. Optimize Operations for Maximum Productivity
Studies show that proper resource allocation can increase manufacturing output by up to 25%. So, Itefy ensures that you get the most out of this by reallocating your resources. The software does this through:
- Detailed analytics on equipment utilization to identify underused or overworked assets.
- A reservation system that enables teams to schedule resources in advance. It helps avoid delays caused by double bookings or availability conflicts.
- Reports on production trends and equipment performance, allowing for data-driven decisions to maximize efficiency.
Itefy Key Features and How They Transform Manufacturing
The equipment management software by Itefy is a powerful tool for manufacturers who want to manage their equipment and resources. It simplifies everyday tasks, reduces errors and helps manufacturers get the most out of their resources.
Here are the main features of this software and how they benefit the manufacturing industry:
1. Advanced Equipment Tracking
Studies show that manufacturers that use automated systems see a 30% boost in operational efficiency. This is why Itefy offers detailed automated tracking for all your manufacturing equipment so you never lose sight of any of it.
In Itefy’s dashboard, each item is logged with specifications like make, model and identification details. The platform helps manufacturers maintain a centralized database and locate tools quickly.
This feature supports efficient manufacturing inventory management which ensures that resources are easy to find and always ready for use.
2. Real-Time Location Monitoring
With Itefy, manufacturers can see where equipment is located at any time. Every item can also be assigned a “home location,” so it is easy to know where it should be when not in use.
The main benefit of it is that it reduces the risk of losing tools or equipment. It also improves planning for upcoming tasks by ensuring equipment is in the right place at the right time.
3. Simplified Equipment Reservations
Itefy’s reservation system helps teams plan better by letting employees book equipment ahead of time. Double bookings are avoided this way and recurring reservations can be made for regular maintenance or tasks.
With better control over reservations, manufacturers can align with their production schedule. This makes it easier for companies to meet deadlines without delays caused by unavailable resources.
4. QR Code Scanning for Accurate Tracking
This software allows users to scan QR codes attached to equipment for quick checkouts and reservations. This eliminates manual errors and makes equipment tracking fast and simple.
By using this feature, manufacturers ensure accuracy in equipment records. Additionally, it saves you time which is actually quite crucial in the fast-moving manufacturing environments.
5. Maintenance Scheduling and Alerts
Itefy helps manufacturers schedule equipment maintenance in advance. It also sends alerts for overdue maintenance or repairs so that manufacturers can keep their machines in top condition. Also, because of this any issues with the equipment are fixed right away.
The major benefit of scheduled maintenance is that it helps minimize equipment downtime, which is one of the biggest causes of production delays. This leads to smoother operations and reduced costs.
How to Use Itefy for Optimizing Manufacturing Resources
To maintain productivity, manufacturers must keep track of numerous resources, including equipment, tools and materials. But, it is not possible without a centralized system as you can easily lose track of your assets or face costly delays. This is why it’s important to have all the resources in one place for better oversight and management.
Here’s how you can get started and make the most of this powerful tool:
1. Create an Account
The best way to check how well this tool works is by signing up for a free trial offered by Itefy. For that visit the website and enter your email address and click on “Start Free Trial”. You can also click on the pink “Try” button to sign up. After this, type in the code received in your email to activate your account.
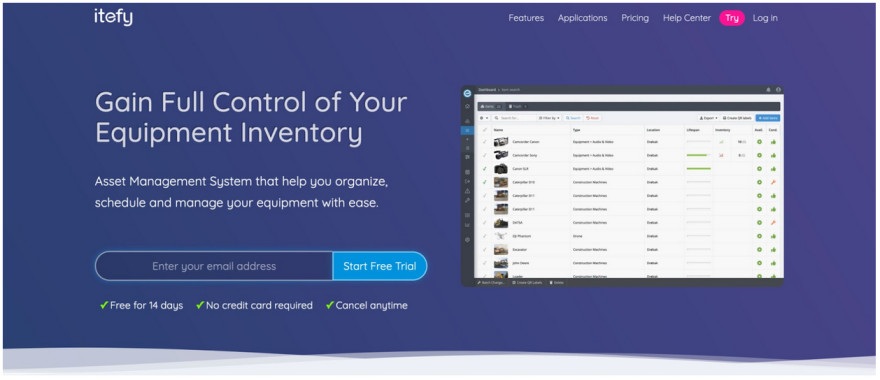
2. Set Up Your Equipment Database
After logging in, you can start adding equipment to your database. To add manufacturing equipment, click on the “Add Items” button with the + sign.
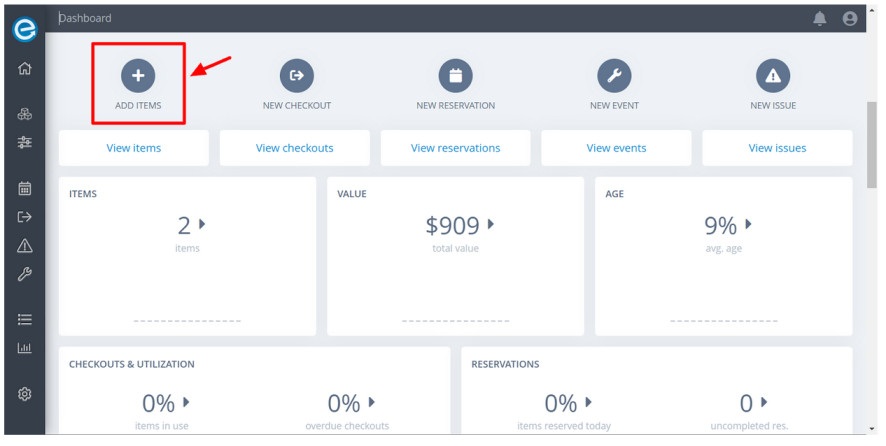
It’ll open a new window where you’ll add the name of the equipment and add its Unique ID. In our case we took Precision Pro Lathe 500 as an example.
Add the item type from the menu. If you can’t find any, create a new one by using the “+” button. In the end, add an image of the equipment so you can easily identify it.
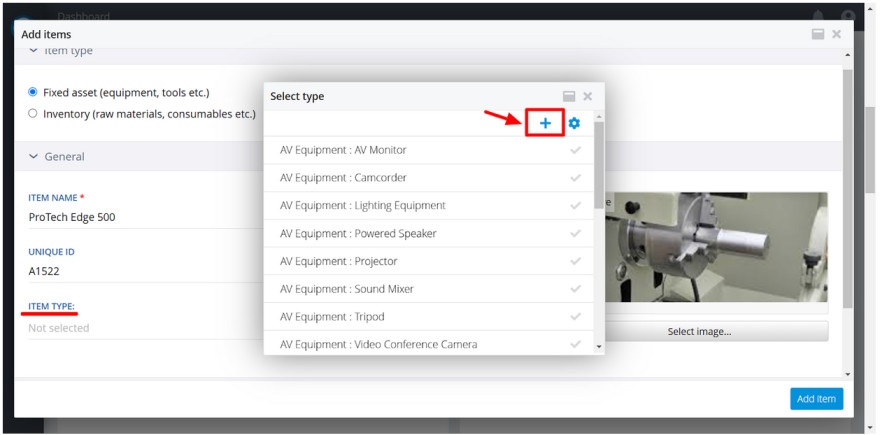
Once you’re done with this step, open the “Purchase Information” drop-down menu. Here you need to add the Purchase Date and Expiry Date for the equipment.
Also add the Purchase and Salvage value for that specific item. Refer to the image below for a better understanding.
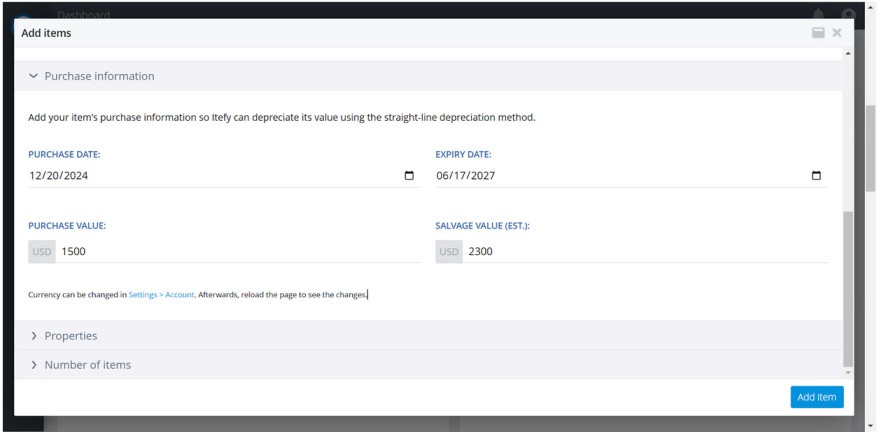
For the next two sections, Properties and Number of Items, add the person responsible for the item and where it is located. Also, add the number of items that you have in use currently.
Once you’ve added all the details and double-checked, click the blue “Add Item” button and your item will be added to the list which you can easily view in the item list.
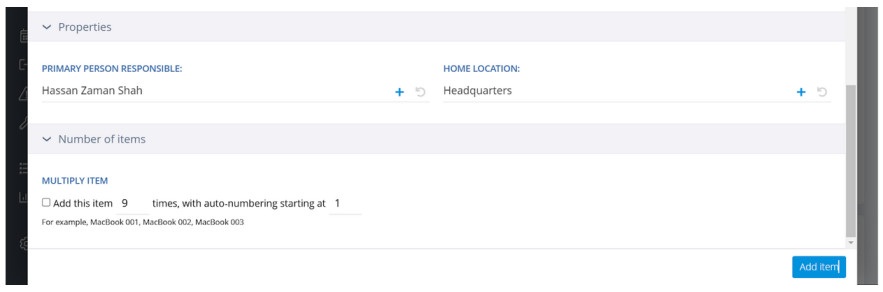
3. Plan and Track Reservations
With Itefy, you can easily create and track reservations. For that, click on the “New Reservation” button with the calendar sign.
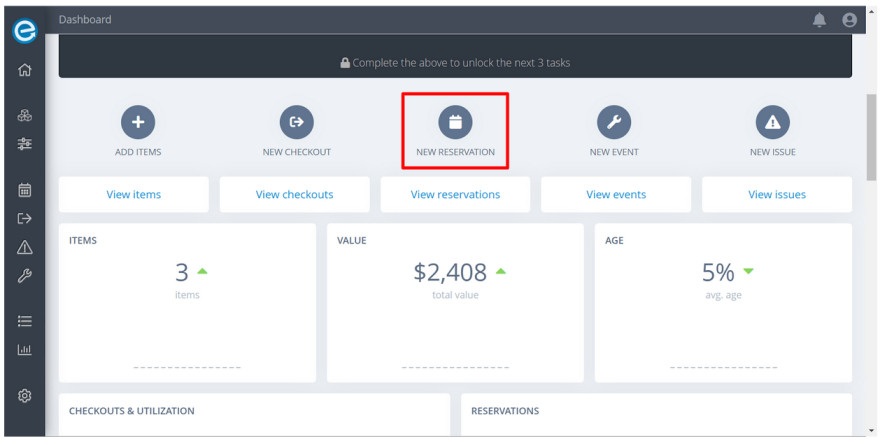
Now, include all the necessary details such as the purpose of the reservation, items you want to reserve, the date and any additional information. Once done, click on “Create Reservation” in the bottom right corner.
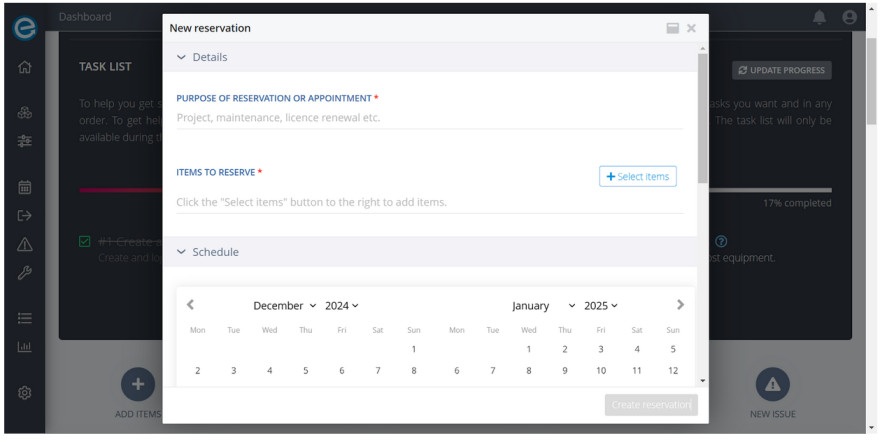
If you want to view upcoming reservations, go to the View Reservations tab and check out which ones are coming up.
4. Monitor And Analyze Items
Click on the “View Items” tab to see a list of equipment you’ve added to the software. Here you can easily check the current value of your manufacturing equipment, lifespan, and mark if the equipment is in optimal condition.

5. Create QR Code Labels
If you decide to label all your equipment for easier access, click on the equipment you want to create the QR code label for from the inventory list.
In the bottom, you’ll see the option to “Create QR Labels”.
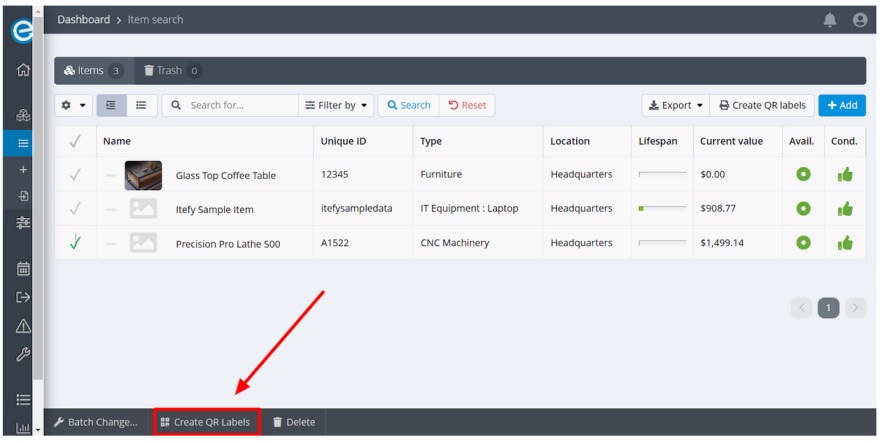
Select the brand and label type to create a label for your item. Then click on “Create PDF File with Label” and you'll have a list of labels which you can now paste on your actual manufacturing equipment.
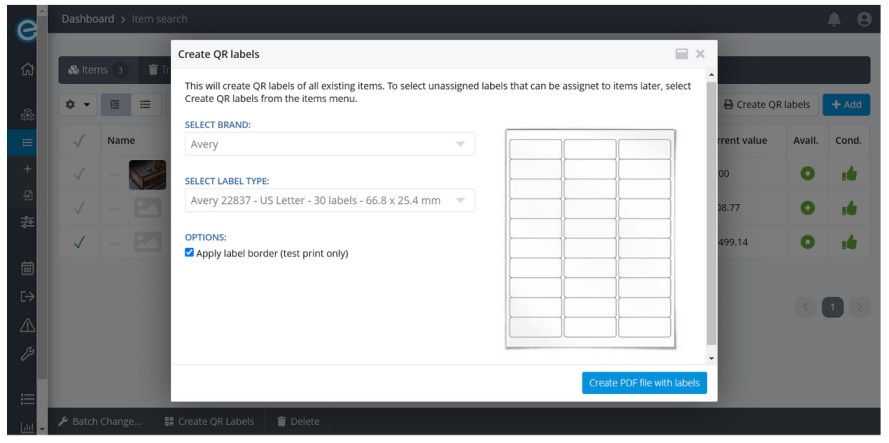
6. Creating and Viewing Checkouts
Another thing that you can do with Itefy is create a “New Checkout” and view the existing ones.
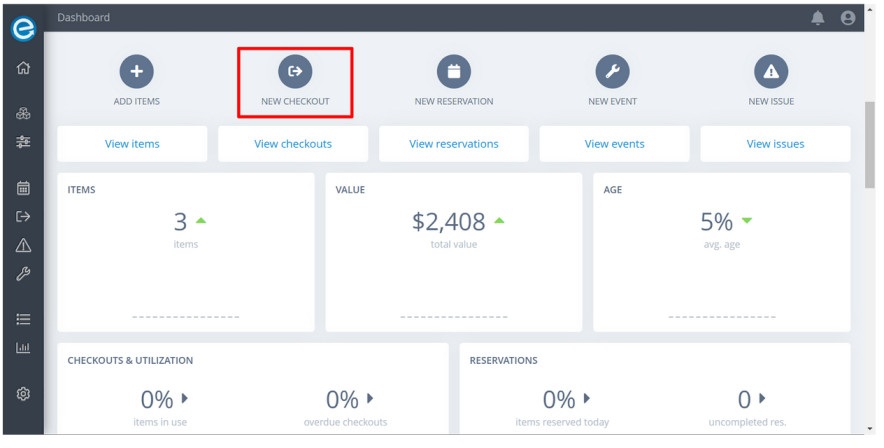
After clicking on this option, you’ll be redirected to a popup where you need to add the reasons for item checkout, the items you want to check out, the date you’ll return it (Duration will be calculated automatically).
You also need to add optional details like the user assigned and the checkout location. If you want, leave additional information for the team. Click on “Check Out” once done.
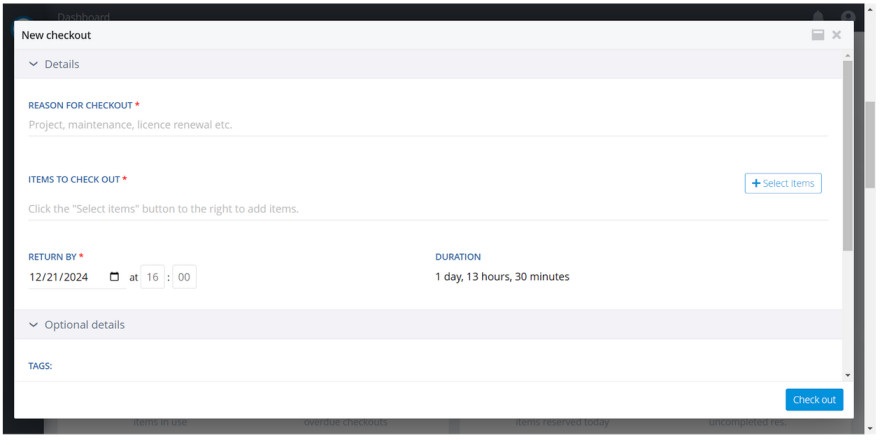
Take Control of Your Manufacturing Resources Today
Efficient resource management is the backbone of any successful manufacturing company. With Itefy’s Equipment Management Software, manufacturing businesses can keep track of their equipment and minimize the equipment downtime. From real-time tracking to streamlined checkouts and proactive maintenance schedules, Itefy offers a solution for every business.
It empowers your team with user-friendly tools, whether on the web or mobile, to ensure smooth operations and reduced losses. Its scalability and intelligent features make it the ideal choice for manufacturers managing multiple facilities or thousands of assets.
So, what are you waiting for? Take control of your manufacturing resources today with Itefy. Request a demo now!
Frequently Asked Questions
-
Equipment management software is a tool designed to help businesses track, organize, and optimize the use of their tools, machinery, and other resources. It provides features like real-time location tracking, maintenance scheduling, and inventory management.
-
Itefy can handle a wide range of manufacturing equipment, such as heavy machinery, tools, vehicles, electronics, and consumable inventory. It’s designed to adapt to the specific needs of manufacturers, so you can track almost any resource in your production process effectively.
-
Itefy helps by providing automated alerts for upcoming or overdue maintenance, real-time tracking of equipment condition, and scheduling proactive repairs. This reduces unexpected failures and ensures your machinery operates smoothly and prevents costly delays.