How to Do Farm Equipment Preventive Maintenance the Right Way
Want to avoid costly breakdowns? Discover how farm equipment preventive maintenance can extend the life of machinery and reduce the need for repairs.
In this article:
- Key Takeaways
- Why Farm Equipment Preventive Maintenance Matters
- Building a Seasonal Maintenance Calendar
- 1. Pre-season (Spring)
- 2. Mid-season (Summer)
- 3. Post-season (Autumn/Winter)
- Key Maintenance Tasks by Component and Frequency
- 1. Engine & Fluids
- 2. Lubrication
- 4. Belts, Hoses & Filters
- 5. Electrical & Lights
- 6. Storage & Cleaning
- Planning & Record-Keeping Systems That Actually Work
- How Itefy Helps in Smart Maintenance Planning
- Common Preventive Maintenance Mistakes on Farms
- 1. Overrunning Machines
- 2. Skipping Lubrication
- 3. Failing to Record Maintenance Tasks
- 4. Ignoring Manufacturer Guidelines
- Don't Let Maintenance Failures Cost You Another Season
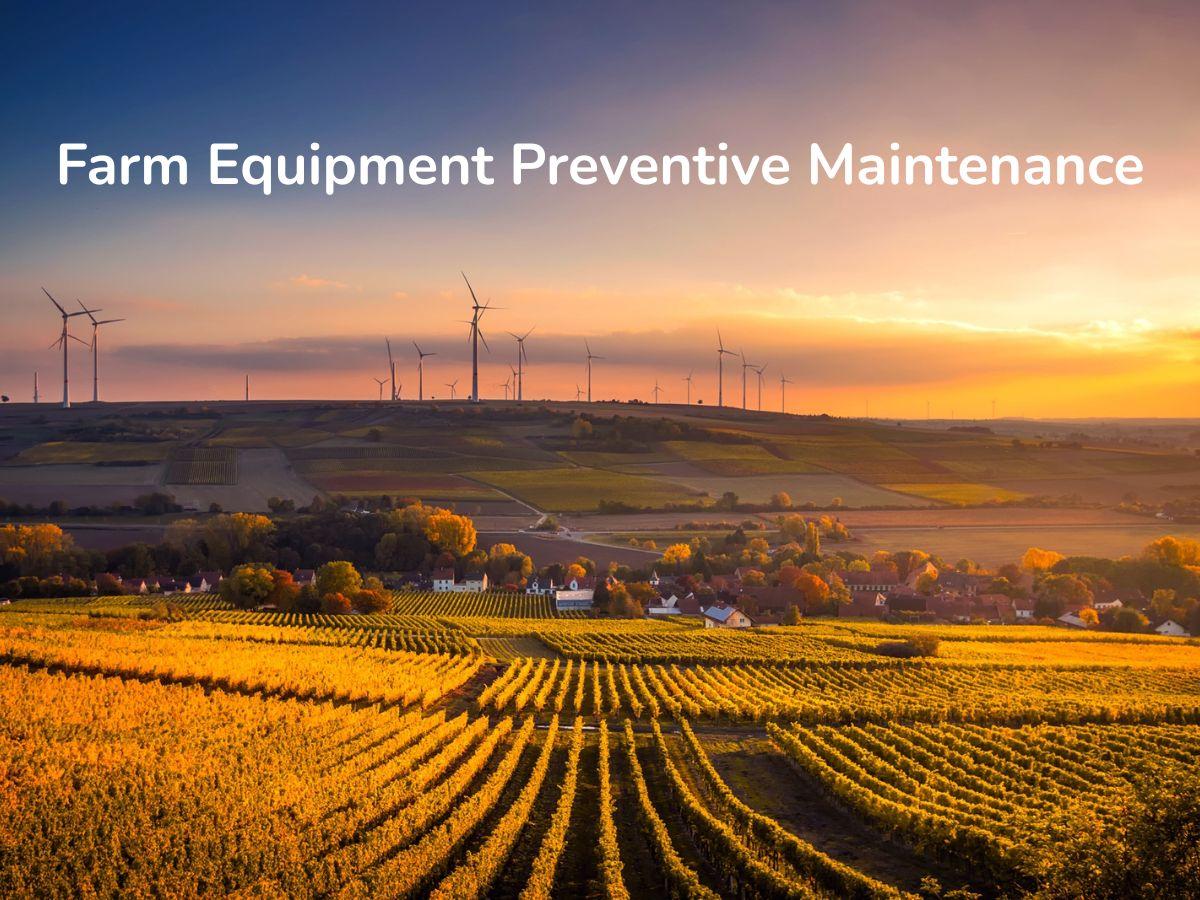
For small to mid-sized farms, every hour of harvest season counts. A single equipment failure can derail their entire schedule and lead to crop loss.
However, 40% of these failures can be avoided with proper maintenance and on-time diagnostics.
That’s where farm equipment preventive maintenance plays a crucial role. It enables you to achieve a successful harvest rather than incurring costly delays.
Let’s break down how a proactive maintenance approach keeps your harvest on track and your machines running.
Key Takeaways
- Why Preventive Maintenance Matters: Preventive maintenance can reduce repair costs by up to 25%. It minimizes unexpected breakdowns, especially during critical seasons such as planting or harvest, and extends equipment lifespan.
- Seasonal Planning Works: Tying maintenance to usage hours instead of calendar dates increases accuracy. A usage-based approach can cut repair costs up to 30% and ensures machines are serviced when they truly need it.
- Avoid Costly Mistakes: Skipping lubrication, overrunning equipment, and ignoring manufacturer guidelines are common but costly mistakes. These minor oversights can lead to major repairs and delays in harvest.
- Smart Tracking with Itefy: Manual logs are often missed. But Itefy keeps you on track with maintenance logs, live status updates, role assignments, and reminders.
Why Farm Equipment Preventive Maintenance Matters
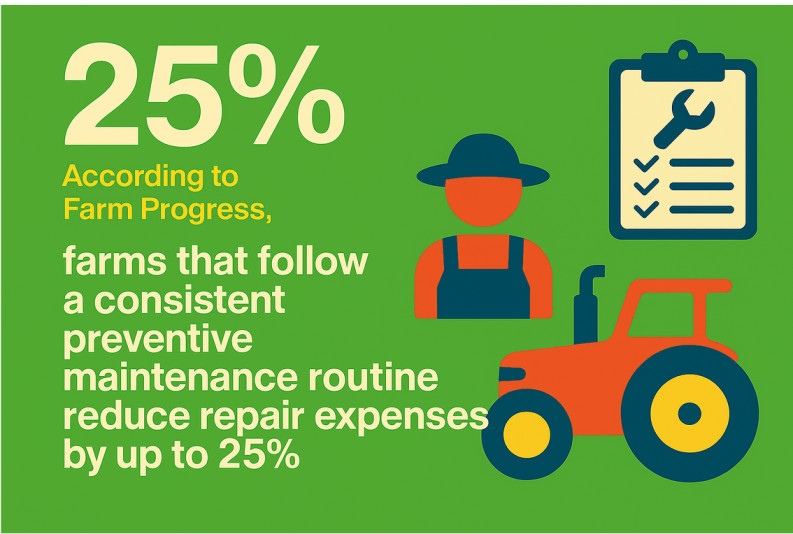
Breakdowns don't wait for a slow day. They hit right in the middle of harvest, planting, or when you're already behind. When they do, the costs go far beyond the repair bill.
Fortunately, much of this disruption can be prevented through consistent farm equipment preventive maintenance. According to FarmProgress, farms that follow a consistent preventive maintenance routine reduce repair expenses by up to 25%.
These proactive practices help identify issues early before they become costly breakdowns. They also keep your equipment running efficiently when you need it most, ensuring fewer delays, longer equipment life, and more productive days in the field.
Building a Seasonal Maintenance Calendar
One of the biggest mistakes in farm equipment preventive maintenance is treating it like a calendar event instead of a usage-based routine. Maintenance shouldn't be done just because it’s spring or fall. It should be tied to the number of hours your machines are working.
Instead of marking dates, track engine hours and schedule service based on activity. Studies have found that usage-based maintenance can reduce repair costs by as much as 30% for a manufacturing plant.
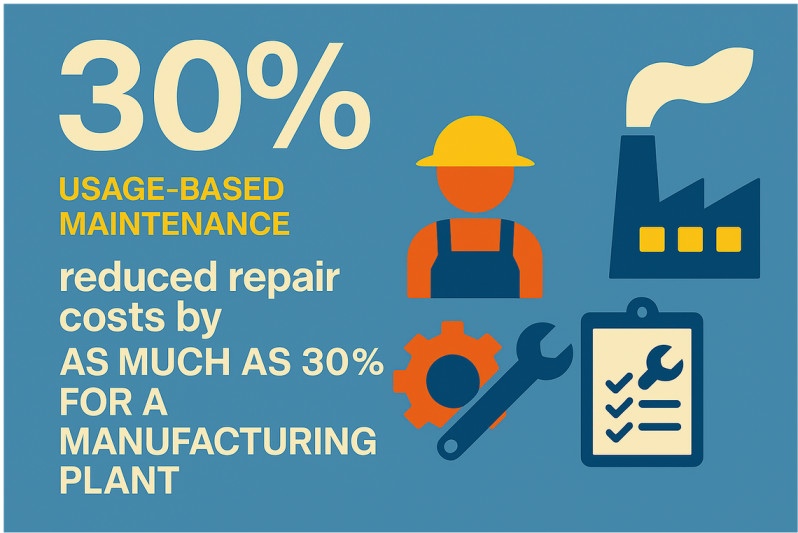
Here's how you can break down seasonal maintenance:
1. Pre-season (Spring)
Before commencing the heavy work, inspect all equipment. Clean out debris, lubricate joints and fittings, check tires, and test batteries. This helps prevent surprises when you need your equipment most. Spring is the ideal time for complete system diagnostics, according to many credible sources and industry experts.
2. Mid-season (Summer)
During peak operation, equipment endures the highest levels of stress. Prioritize regular oil changes, air filter replacements, and inspections of hoses and belts. Summer heat and dust accelerate wear and tear, making mid-season maintenance essential to keep your machines running reliably when you need them most.
3. Post-season (Autumn/Winter)
Once the season winds down, it's time to winterize the machines. Drain fluids, disconnect or remove batteries, apply anti-rust coatings, and store equipment in clean, dry places. This protects your investment during the off-season and makes spring startup smoother.
Key Maintenance Tasks by Component and Frequency
Preventive maintenance isn't just about doing a quick once-over. It's about knowing what to check, how often, and why it matters. Each part of your farm equipment plays a crucial role, and neglecting even one system can result in significant downtime.
Let's break down various tasks and their maintenance schedules:
1. Engine & Fluids
Your engine does the heavy lifting on the farm. To keep it running smoothly, regular oil and filter changes are non-negotiable. Most manufacturers recommend this service every 100 to 150 hours of use, although environments with high dust levels may require more frequent service.
Moreover, coolant levels should be checked consistently. Without proper cooling, engines can overheat, especially during long, hot summer days.
Another component that is often overlooked is the fuel injectors. Make sure to keep an eye on these, as they can reduce power and increase fuel use if clogged.
2. Lubrication
Lubrication is your first line of defense against wear and tear. Fittings, joints, and bearings should be greased every 10 to 25 hours, depending on the application. The harder your equipment works, the more frequently it needs attention.
Chains and linkages also demand frequent attention. Without regular lubrication, friction builds up, leading to heat, damage, and, eventually, breakdowns.
According to Machinery Lubrication, proper lubrication can reduce equipment failures by up to 50%. It's a small step with a big impact, protecting your equipment and extending its life with minimal effort.
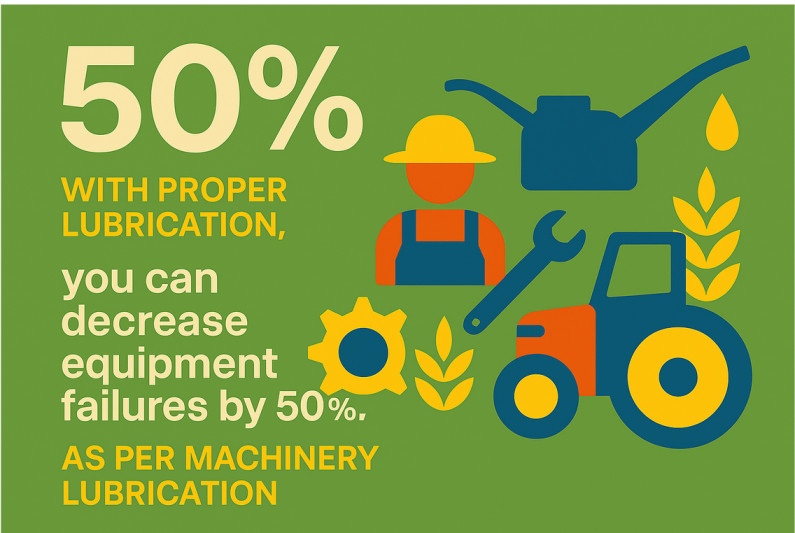
3. Tires & Hitches
Your equipment travels as much as it works, and that puts pressure on tires and hitches. Always check tire pressure and tread before operation. Low pressure not only affects performance but also increases fuel consumption.
Look for cracks or uneven wear, especially after machines have been idle for extended periods. Hitches and pins should be cleaned and lubricated to prevent rust from forming. A bent hitch or loose pin can turn into a dangerous, costly accident if left unchecked.
4. Belts, Hoses & Filters
Belts and hoses often take a beating during peak seasons. Check them weekly for cracks, fraying, or bulging, especially in older machines or during extreme temperatures.
Don't wait until a belt snaps in the middle of a job. Replace weak parts before failure. Similarly, dirty air filters restrict engine breathing. Cleaning them every 50 hours and replacing them every 200 hours can improve both fuel efficiency and performance.
5. Electrical & Lights
Even the toughest machine can't run without power. Clean battery terminals regularly to prevent corrosion and voltage drops. As temperatures shift, especially in colder months, battery performance can take a hit, so testing and maintenance are key.
Don’t forget the wiring. Inspect cables for wear, exposure, or rodent damage, particularly if equipment is stored outdoors. Also, ensure that all lights and indicators are fully functional; they’re critical for safe operation during early mornings and late harvest nights.
6. Storage & Cleaning
Maintenance doesn’t stop at the end of the season. Dirt, moisture, and plant debris left on equipment can accelerate rust, corrosion, and decay. Before storing, give your machines a thorough cleaning, both inside and out.
Apply anti-rust coatings to exposed metal, disconnect batteries, and store everything in a dry, sheltered space. Proper storage ensures your equipment is ready to go when you are and not sitting with hidden damage when spring arrives.
Planning & Record-Keeping Systems That Actually Work
Farm equipment preventive maintenance only works if you remember to do it. And for that, you need a reliable system to plan tasks and track what's been done.
Unfortunately, many farmers still rely on memory or scattered notebooks. That leads to missed oil changes, forgotten filter swaps, and costly surprises.
You don't need anything fancy to start. A simple calendar with reminders, or a shared manual spreadsheet, can all do the job. Some farmers also prefer paper logs. However, the most effective approach is to adopt a hybrid method of manual tracking combined with software like Itefy.
How Itefy Helps in Smart Maintenance Planning
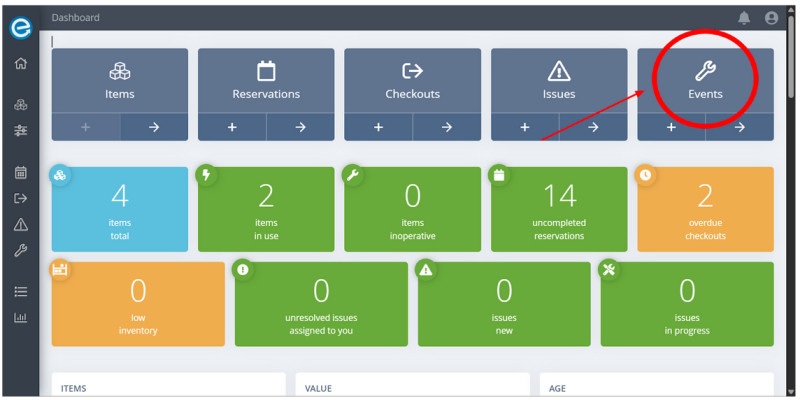
When you're ready to move beyond pen and paper, Itefy's Equipment Management Software streamlines the entire maintenance process. With this tool, you can:
- Log maintenance records for every piece of equipment in one place
- Get reminders for upcoming tasks like oil changes or inspections
- Assign roles, so everyone knows who's responsible for what
- Check live status from your phone, tablet, or laptop
- Avoid equipment loss with location tracking and QR-scanning features
The best part is, you don't need any IT training or a big setup. Itefy works from any browser and can also be accessed through a mobile app.
Common Preventive Maintenance Mistakes on Farms
Despite the best intentions, many farms fall into the same maintenance traps. These oversights might seem minor at the time, but often lead to costly breakdowns and long-term equipment damage.
The good news? They're easy to avoid if you know what to look for.
1. Overrunning Machines
Many farmers run equipment longer than it's defined for, especially during crunch time. While it might feel necessary at the moment, this often leads to unexpected downtime during the next job, when schedules are already tight.
The root cause is usually a lack of backup equipment or poor planning. Instead of pushing one tractor for 14 hours straight, consider rotating usage between machines or building in short recovery periods. It’s a small adjustment that can prevent bigger breakdowns down the line.
2. Skipping Lubrication
Lubrication tasks are easy to delay, especially when you're short on time or tired. But dry joints and ungreased bearings are silent destroyers.
It’s easy to assume, “I greased it last week,” or “I’ll do it after this job.” That mindset turns a five-minute task into a preventable failure, one that could result in hours of repairs and lost productivity.
3. Failing to Record Maintenance Tasks
Relying on memory often leads to mistakes. One team member assumes the oil was changed and another forgets they skipped the last air filter replacement.
Without written records, there's no way to track what has been done or what is overdue. The absence of a system creates confusion, which in turn leads to missed work.
4. Ignoring Manufacturer Guidelines
Manuals often sit unread on shelves. But the details in them matter. Skipping recommended service intervals, using generic parts instead of OEM, or using the wrong type of oil can all shorten equipment life.
These shortcuts may save time now, but they increase repair costs and even void warranties. Many farmers simply don’t revisit these guidelines once the equipment is up and running, assuming one-size-fits-all care will do.
Don't Let Maintenance Failures Cost You Another Season
Farm equipment preventive maintenance isn't about being perfect; it's about being prepared. With the right plan and a tracking tool, you'll spend less time fixing and more time getting work done.
That’s where Itefy comes in.
Built for farms and field teams, Itefy is a cloud-based platform that eliminates the guesswork from maintenance. No more missed checklists. No more “When was that last serviced?” moments. Just better uptime, fewer breakdowns, and complete control.
Start your 14-day free trial today and see how Itefy can help protect your equipment.
Frequently Asked Questions
-
Yes, basic tests, such as checking for unusual vibrations, fluid leaks, overheating, or hard starts, can reveal early issues. Use a handheld infrared thermometer to spot hot zones or listen for abnormal engine sounds. Routine visual inspections and touch-based checks can help prevent more significant breakdowns.
-
Remove batteries from equipment and store them in a cool, dry place. Clean terminals, apply anti-corrosion gel and charge them every 30–60 days to maintain health. Keeping them off and away from moisture prevents discharge and extends battery life.
-
Yes, premium diesel and additives can improve engine performance, reduce carbon buildup, and extend the longevity of the fuel system. Additives help prevent gelling in cold weather and improve lubrication. While slightly more expensive, the benefits often outweigh that by reducing maintenance needs.