Inventory Shrinkage Prevention: 10 Proven Best Practices
Are you struggling with inventory losses? Learn effective inventory shrinkage prevention best practices to protect your stock and improve your bottom line.
In this article:
- What Is Inventory Shrinkage?
- The Real Cost of Inventory Shrinkage for Businesses
- 10 Best Practices for Inventory Shrinkage Prevention
- 1. Implement Regular Cycle Counts
- 2. Use Inventory Management Software with Real-Time Tracking
- 3. Control Who Has Access to Inventory
- 4. Train Employees on Inventory and Theft
- 5. Improve Vendor and Supplier Management
- 6. Conduct Surprise Audits
- 7. Use Smart Inventory Tracking Tools
- 8. Create a Culture of Honesty and Awareness
- 9. Secure High-Theft Items Separately
- 10. Set Up Clear Inventory Handling Procedures
- Take Back Control Over Inventory Shrinkage with Itefy
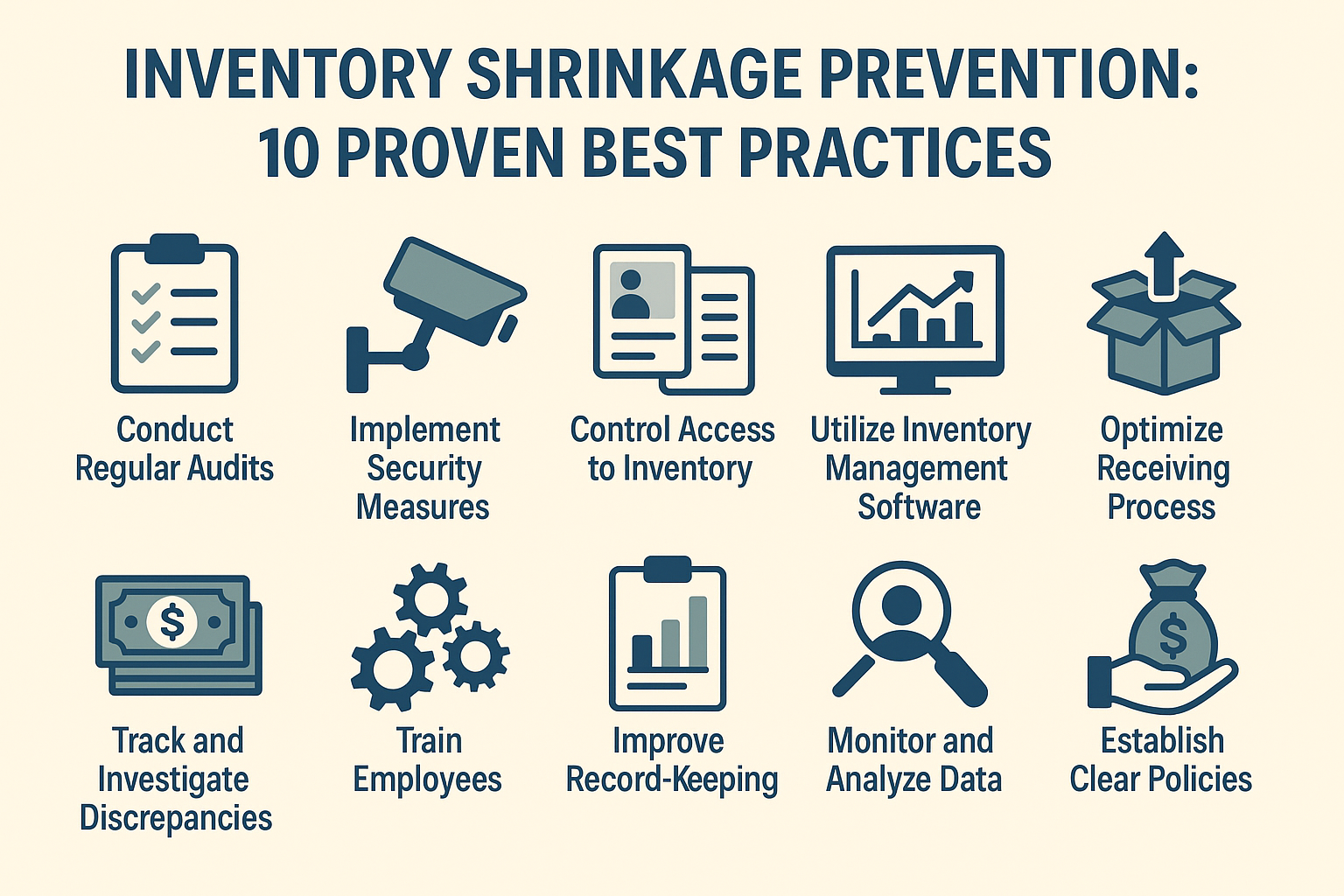
Inventory shrinkage might seem like a minor issue at first—just a few missing items here and there. But over time, it silently reduces profits, disrupts supply chains, and creates gaps in customer trust.
Whether it’s due to theft, damage, or administrative errors, shrinkage is a problem businesses can no longer ignore.
But the good news?
You don’t need a complete system overhaul to fix it. With the right inventory shrinkage prevention strategies, you can significantly reduce shrinkage and regain control over your inventory. Let’s get started.
What Is Inventory Shrinkage?
Before you start considering inventory shrinkage prevention tips, you need to understand what it really means. Inventory shrinkage refers to the difference between the recorded inventory in your system and the actual physical inventory you have on hand.
In simple terms, it’s the missing items that are unaccounted for and not sold, returned, or transferred.
Shrinkage is not the same as expected inventory loss, such as spoilage (for perishables), damage during transit, or planned markdowns. Unlike these known losses, shrinkage usually indicates a problem in your inventory control process.
The Real Cost of Inventory Shrinkage for Businesses
Inventory shrinkage isn’t just a minor loss, but a multi-billion-dollar problem. According to the National Retail Federation, shrinkage reportedly cost U.S. retailers $112.1 billion in 2022. It accounted for nearly 1.6% of total retail sales, and that’s just one sector.
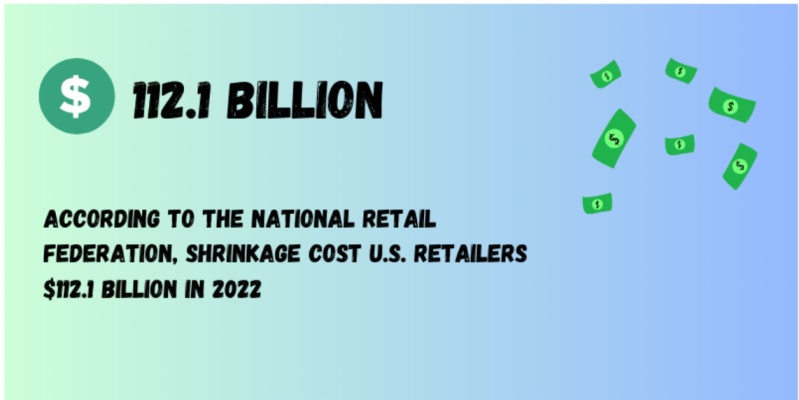
Source: NRF
Here’s how shrinkage can impact your business:
- Revenue loss: Every lost item directly reduces your profitability.
- Higher prices: To compensate, businesses often raise prices, which hurts competitiveness.
- Compliance risks: In regulated industries like healthcare or aerospace, shrinkage can lead to legal or financial penalties.
- Increased operational costs: Extra audits, enhanced monitoring, and lost time investigating discrepancies increase your bottom-line cost.
If you don’t want to face these issues, it’s important to take proactive steps to prevent inventory shrinkage before it spirals out of control.
10 Best Practices for Inventory Shrinkage Prevention
Below are the 10 proven best practices that leading businesses use for inventory shrinkage prevention and to protect profit margins.
1. Implement Regular Cycle Counts
Relying on annual stock counts means errors can go unnoticed for months. Regular cycle counts, where small sections of inventory are audited frequently, help catch discrepancies early.
To apply this concept:
- Use ABC analysis: Count high-value or fast-moving items more often.
- Rotate inventory sections: Rotate sections weekly or monthly based on importance.
- Offer training to your team: Train your team to count items carefully, record what they find, and compare to what’s in the system.
Companies that use cycle counting see fewer discrepancies compared to those relying on annual costs.
2. Use Inventory Management Software with Real-Time Tracking
An inventory management system is a software that helps track your products. It tells you what’s in stock, what’s running low, and what’s missing. It works in real time, so you always know what’s happening in your store or warehouse.
To set it up, choose a system that matches your business size. The best software for this is Itefy. Our inventory management software helps businesses keep track of their products, including maintenance and checkouts.
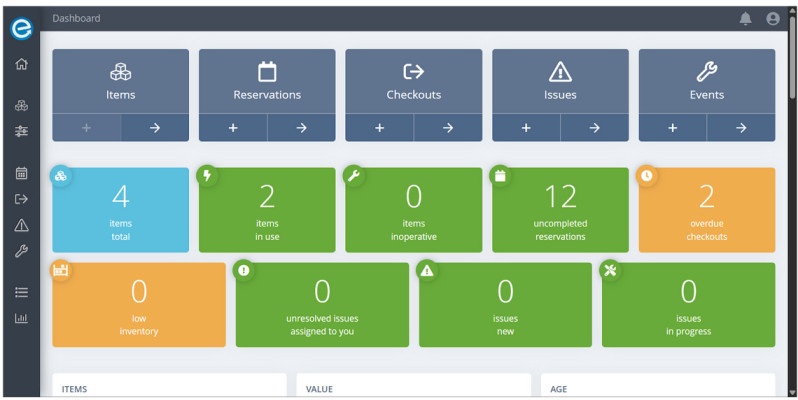
You can also use barcodes and scanners to speed things up and reduce mistakes. The software can also alert you when something doesn’t match. For example, when 100 items were ordered, only 98 were received.
This way, you can catch problems early and act fast before a small mistake becomes a big loss. It also makes your audits easier and less stressful.
3. Control Who Has Access to Inventory
Not all of your employees need access to your storage or stockroom. The fewer people who handle inventory, the easier it is to track problems. This is called access control.
With software like Itefy, managers can limit unauthorized access by using locks, ID cards, or PIN codes. It also keeps track of logging details, allowing you to find the details if something goes wrong.
By doing this, you reduce the risk of internal theft. You also make it easier to manage who’s responsible for what. It’s a simple but powerful way to protect your business.
4. Train Employees on Inventory and Theft
Many inventory problems, such as shrinkage, stem from a lack of training. In some cases, theft can occur if employees think no one will pay attention. You can counter both these problems with effective training.
To train your employees:
- Training during onboarding: Offer training right from the onboarding process.
- Teach about product handling: Show employees how to handle products, scan items, and report mistakes.
- Refresher courses: Lastly, offer short refreshers every few months.
Also, make it clear that your business takes stealing very seriously, and explain what happens if someone is caught. Sometimes, just knowing that there’s a system in place is enough to stop someone from stealing.
Employees who feel trusted and informed are more likely to follow the rules. They also help watch for problems.
5. Improve Vendor and Supplier Management
Vendors and supplies can sometimes cause inventory shrinkage. This could happen through short shipments, damaged goods, or even fraud. That’s why it’s important to manage vendor relationships carefully.
Start by checking all deliveries as soon as they arrive. Count and inspect items. If anything is missing or broken, report it immediately. Use purchase orders and match them with delivery receipts and invoices. This is called a “three-way match.” It helps catch mistakes early.
You should also work only with trusted suppliers. Check their reviews, track records, and how they respond to problems. Build long-term relationships with vendors who are honest and reliable.
Studies show that almost 60% of businesses face a 15% or more revenue loss due to supply chain delays. That’s a lot, considering small businesses usually have small margins.
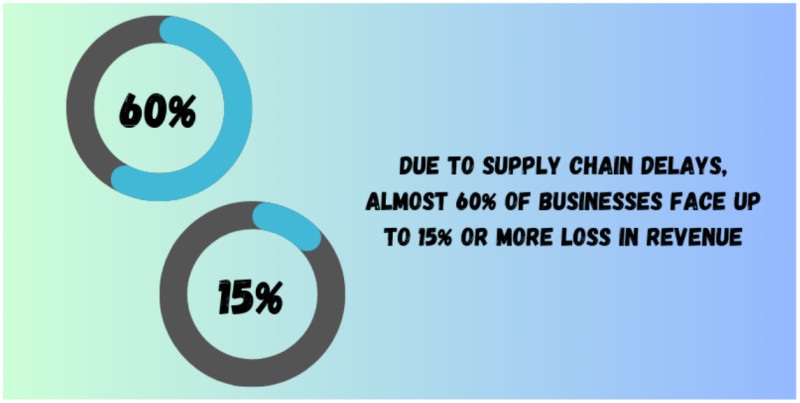
Source: SDCEXEC
6. Conduct Surprise Audits
Surprise asset management audits are random inventory checks without prior notice. They help catch dishonest behavior, mistakes, or system errors that regular audits might miss.
To do this, choose a day when employees don’t expect audits. Check physical stock against what your system says. In the end, look for missing, damaged, or mislabeled items.
You can do this often, but be careful not to become predictable. To keep things fair, let supervisors or third parties handle these audits. Over time, this will build a culture of accountability and accuracy.
7. Use Smart Inventory Tracking Tools
Manual tracking is slow and full of errors. If you’re still using it, it’s time to move on and use inventory tracking software like Itefy. Our tracking software allows you to scan items in and out of storage, so everything is up-to-date in real time.
With it, you can see what’s in stock, where, and how it moves. If something goes missing, you’ll know exactly when and where it happened. In addition to this, you should also use tools like barcodes, RFID tags, or QR codes.
Research shows that 62% of businesses that use RFID improve inventory accuracy to over 95%. That means fewer errors, better restocking, and less shrinkage.
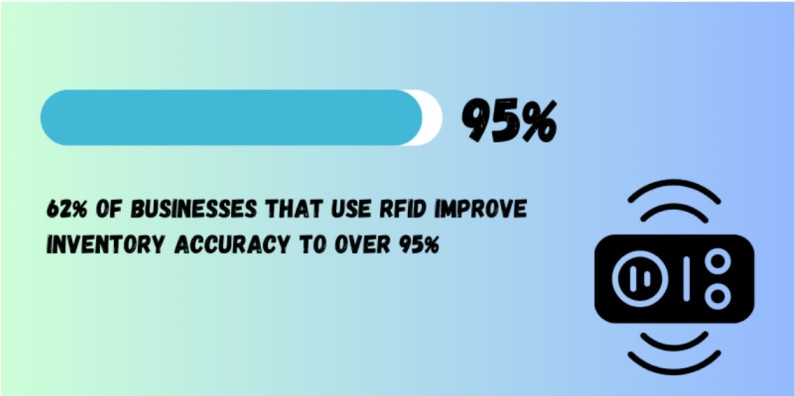
Source: Cybra
8. Create a Culture of Honesty and Awareness
Sometimes, shrinkage happens because people don’t realize its impact. Other times, it’s due to a lack of ethics. That’s why you need to build a workplace culture where honesty matters and shrinkage is taken seriously.
To create an effective culture of honesty:
- How shrinkage affects business: Explain to your employees how shrinkage affects the business and their jobs.
- Explain problem reporting practices: Train them to report problems without fear.
You can also use posters, reminders, and rewards to keep the message alive. Don’t forget to recognize employees who prevent mistakes or report issues.
9. Secure High-Theft Items Separately
Every business or shop has items that are stolen more often than others due to their value and ease of access. These could include electronics, tools, or branded goods, meaning they need extra security.
You can keep them in locked cabinets or behind counters. Use cameras or alarms for added protection. Also, track them with barcodes, RFID tags, or other inventory tagging systems to know their status.
If they’re on the shop floor, limit access. Let only trained staff handle them. If the products are stored mostly in warehouses, store them near supervisors or in high-visibility areas. By focusing on these products, you can reduce losses without spending too much or slowing down operations.
10. Set Up Clear Inventory Handling Procedures
Having clear rules makes everything easier. If everyone follows the same steps for receiving, storing, counting, and moving inventory, there will be less confusion and fewer mistakes.
What you can do is write down procedures for each task. For example:
- How to receive deliveries and check for damage
- Where to place items in storage
- How to label or tag each product
- How to count items and log them into your system
Make sure these rules are easy to understand. Go over them with staff during training and post them in key areas like stockrooms or loading bays.
Take Back Control Over Inventory Shrinkage with Itefy
Inventory shrinkage can silently drain your profits, lower productivity, and erode team trust. But the good news is: it’s preventable with the help of inventory shrinkage prevention strategies and a bit of automation.
If you’re ready to reduce shrinkage and gain complete control over your equipment, Itefy’s Asset Management Software is built for you. Whether you run a warehouse, a rental company, or a growing team, we keep your inventory organized, visible, and protected.
Start your 14-day free trial today and let Itefy do the tracking.
Frequently Asked Questions
-
Shrinkage is inventory loss due to theft, fraud, or errors. Spoilage happens when items expire or become unusable, like perishable food. Spoilage is expected in some industries, while shrinkage is preventable and should be minimized.
-
To prevent shrinkage, use basic inventory software, do weekly counts, limit stockroom access, and train employees. Label all items and keep detailed records. Even without big systems, small changes in routine can reduce errors and discourage theft.
-
A good shrinkage rate is usually 1% of total inventory, depending on your industry. Retail stores have an average of 1.4% to 2%, while manufacturing and distribution aim for lower. Anything above 2% requires stronger controls and better tracking systems.