CMMS vs Manual Spreadsheets: Modern Maintenance Scheduling
Is CMMS better than manual spreadsheets? Discover the real difference in “CMMS vs Manual Spreadsheet” and why it matters for efficiency in modern maintenance.
In this article:
- What is a CMMS?
- How Manual Spreadsheets Handle Maintenance Tasks
- CMMS vs Manual Spreadsheets: Key Differences Explained
- 1. Simplicity vs Complexity in Everyday Use
- 2. Real-Time Work Order Visibility
- 3. Error Rates and Data Accuracy
- 4. Reporting and Decision-Making
- 5. Maintenance Scheduling
- 6. Collaboration and Team Communication
- 7. Compliance and Audit Readiness
- 8. Total Cost of Ownership
- Which One Is Better? CMMS vs Manual Spreadsheets
- Choosing the Right CMMS for Your Business
- 1. Real-Time Equipment Tracking
- 2. Easy Maintenance Scheduling
- 3. Reservation Planning
- Take Full Control of Your Maintenance with Itefy
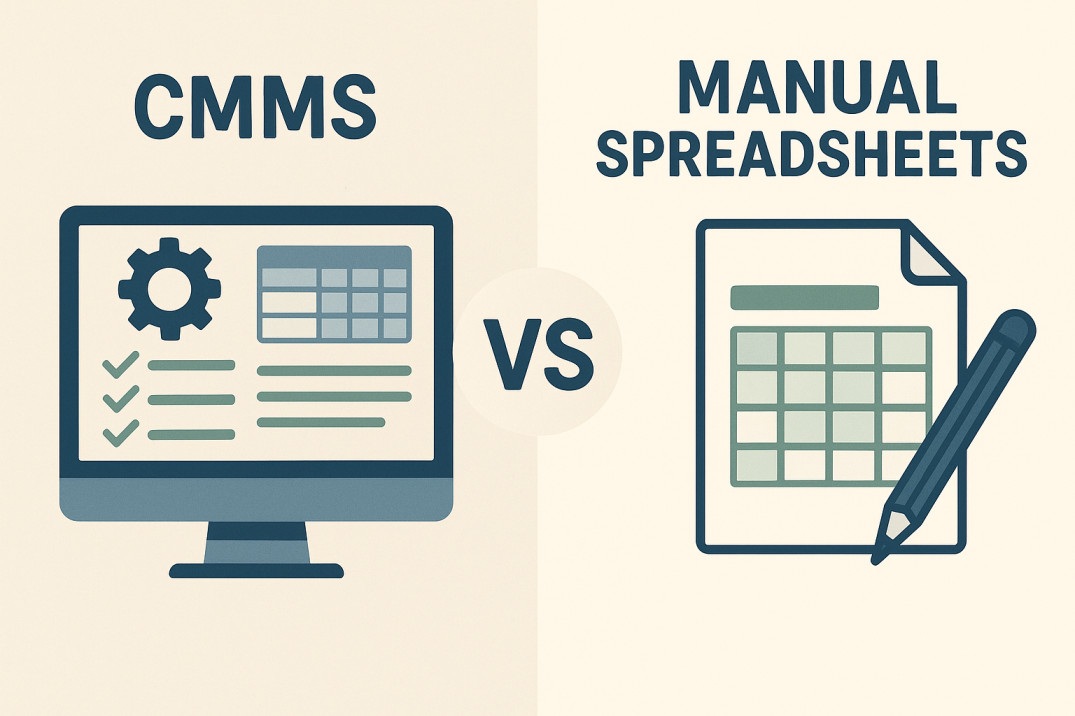
Are your maintenance teams still buried in spreadsheets? If so, you’re part of almost 80% of the companies that rely on manual methods like Excel to manage maintenance.
The real issue here is that outdated methods often lead to missed tasks, more downtime, and higher costs. If you want to avoid that, it’s time to switch to a CMMS. It makes maintenance scheduling incredibly easy and far more productive.
In this blog, we’ll break down CMMS vs Manual Spreadsheets and show you which one truly keeps your operations running smoothly.
What is a CMMS?
A CMMS (Computerized Maintenance Management System) is software that helps businesses manage and automate their maintenance operations. Instead of using paper logs or spreadsheets, a CMMS keeps everything in one place (digitally).
Imagine you’re running a factory and a machine suddenly breaks down. With a CMMS, your technician gets an alert, checks the machine’s history, sees what was fixed before, and follows step-by-step instructions. Once it’s repaired, the system updates everything automatically.
No paper, no guesswork. Plus, the database can be accessed anytime, from anywhere, allowing you to monitor everything in real time.
How Manual Spreadsheets Handle Maintenance Tasks
Before digital systems, most maintenance teams relied on manual spreadsheets, paper logs, and email chains to track equipment and repairs. This method worked for a time, but it was slow, error-prone, and hard to scale.
For example, a maintenance supervisor might use an Excel sheet to list all machines, their service history, and upcoming maintenance dates.
When a technician completes a job, they'd email the supervisor or write the details in a logbook. The supervisor then had to manually update the spreadsheet.
CMMS vs Manual Spreadsheets: Key Differences Explained
Managing maintenance operations efficiently can make or break a business. While some teams still use spreadsheets, modern businesses are shifting to CMMS, with 72% of companies already using it for maintenance.
Let’s break down the major differences between CMMS and manual spreadsheets in a way that shows why switching matters.
1. Simplicity vs Complexity in Everyday Use
Manual spreadsheets are familiar, but familiarity doesn’t mean efficiency. Using Excel or paper logs for maintenance requires every technician to open large, often disorganized files, search through tabs, and constantly update entries.
A CMMS, however, is purpose-built. It’s designed with simple dashboards, mobile access, and user-friendly workflows. Teams don’t have to guess where to log issues or track jobs. Everything is structured, which gives CMMS the upper hand in making things simpler yet perfect.
2. Real-Time Work Order Visibility
With spreadsheets, assigning and tracking work orders is manual and fragmented. You have to rely on someone who remembers to update the sheet or send a follow-up email. If one person forgets, the entire maintenance chain can break down.
In contrast, a CMMS automates this flow. When a task is created, you can assign it to the right technician, log it in the system, and timestamp it. Updates happen in real time, and managers can instantly see who’s performing the task and when it will be completed.
3. Error Rates and Data Accuracy
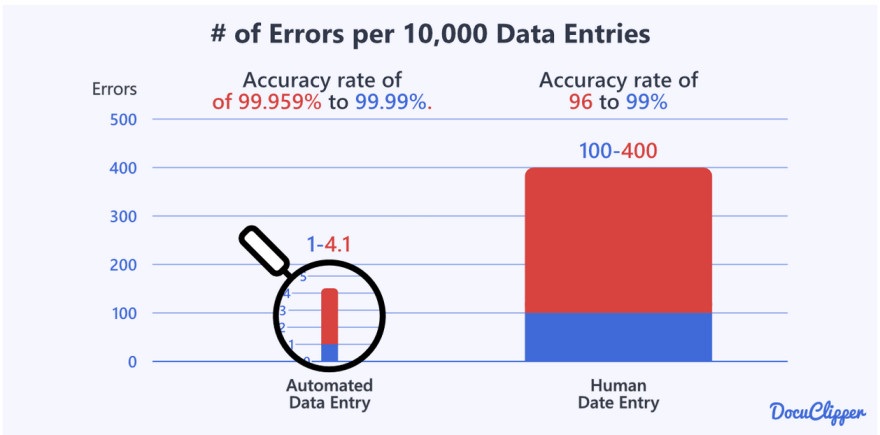
Source: Docuclipper
Human error is inevitable with spreadsheets, accounting for as much as 4% of the entries. From mistyped numbers to accidental deletions, even one small mistake can snowball into asset downtime or compliance risks. The bigger the operation, the higher the risk.
CMMS platforms dramatically reduce this margin of error. With controlled data entry, drop-down menus, and validation rules, input mistakes are minimized. The platform also maintains version control, so there’s no confusion about which file is the latest.
4. Reporting and Decision-Making
Manual spreadsheets make reporting a total nightmare. Generating weekly or monthly reports means pulling data, double-checking numbers, creating charts, and hoping you didn’t miss anything. It’s time-consuming and often incomplete due to the human element.
However, the easiest solution to this is to use a CMMS system. With it, you can generate reports on asset performance, technician productivity, maintenance costs, and downtime with a few clicks. This helps managers make more confident decisions with accurate, up-to-date data.
5. Maintenance Scheduling
Maintenance scheduling with spreadsheets means manually entering dates, setting reminders, and constantly following up. It’s easy to overlook recurring tasks or forget overdue ones, especially when you or your worker is dealing with multiple assets.
You can automate scheduling with CMMS systems with ease. These tools have built-in preventive maintenance plans that send automatic reminders and track service internals. This way, your machines get serviced on time, reducing unplanned breakdowns.
6. Collaboration and Team Communication
Excel was never designed for teamwork. This tool doesn’t always track changes, edits can overlap suddenly, and there’s no version control. This leads to confusion, missed updates, and blame games when things go wrong.
With a CMMS, collaboration is seamless. Everyone logs into the same platform with role-based permissions. Technicians get real-time updates, managers get alerts, and the whole team stays on the same page.
Companies that use CMMS say that their maintenance teams became 44% more productive and coordinated.
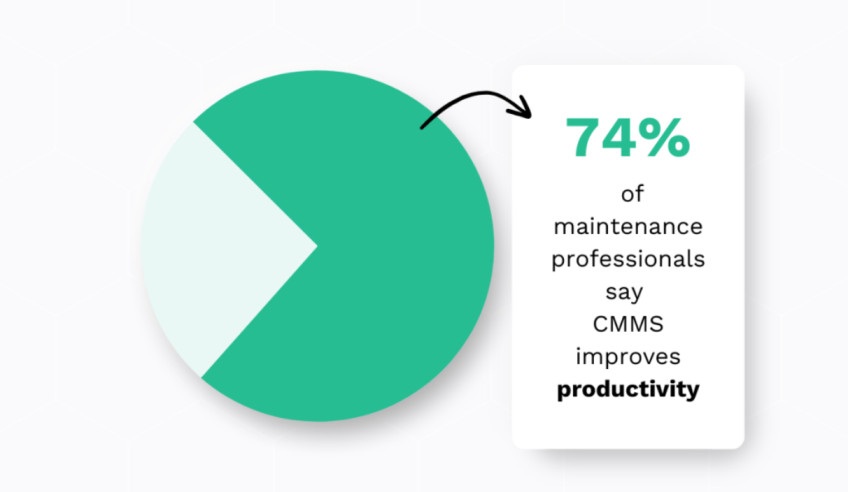
Source: WorkTrek
7. Compliance and Audit Readiness
Keeping up with industry regulations is already hard enough. And spreadsheets make it even tougher. If you use these, you won’t have any audit trail, inconsistent formats, and will keep missing documentation, which will trigger failed inspections and legal issues.
But CMMS systems don’t have to go through any of this. These systems automatically log everything with timestamps, work order histories, compliance checklists, technician notes, etc. This way, when auditors come knocking, you’ll be ready with proof.
8. Total Cost of Ownership
At first glance, spreadsheets seem “free”. But the hidden costs, such as the missed tasks, unplanned downtime, lost data, and labor hours, quickly add up. Moreover, don’t forget the risk of costly compliance violations and asset failures.
For CMMS, you might have to spend some capital on subscription, but the ROI is clear. By reducing downtime, improving scheduling, and automating admin work, it pays for your investment quickly.
According to reports, companies that use CMMS see an average of 15% to 20% reduction in maintenance costs throughout operations.
Which One Is Better? CMMS vs Manual Spreadsheets
CMMS clearly outperforms manual spreadsheets for maintaining equipment and managing tasks. It automates routine scheduling, sends real-time alerts, and stores all assist history in one place. This reduces downtime and minimizes the risk of human errors.
Spreadsheets, as you know, rely on manual input, which slows things down and leads to costly mistakes. When your business grows, it simply can’t keep up.
With a CMMS, teams can save time and improve work accuracy, especially when handling multiple assets or locations. It also makes audits, compliance, and reporting much easier by organizing everything in a few clicks.
Spreadsheets may work for very small teams, but they lack the flexibility and reliability needed in the modern world of maintenance. So, if you're serious about maintenance efficiency, CMMS is undoubtedly the smarter investment.
Choosing the Right CMMS for Your Business
When selecting a CMMS, you need a system that simplifies maintenance and gives you full control. Itefy stands out in this regard.
Its intuitive dashboard brings every feature you need into one easy-to-use platform, whether you're managing equipment from an office or in the field. These include:
1. Real-Time Equipment Tracking
With Itefy, you can effortlessly add, categorize, and locate equipment. Each asset can include detailed specs, depreciation data, and condition logs. The dashboard gives you live status updates, so you'll know instantly if something is missing, overdue, or under repair.
To add assets, go to the “Add Items” tab in the dashboard and add all the relevant details. These include item type, unique ID, category, purchase date, and more.
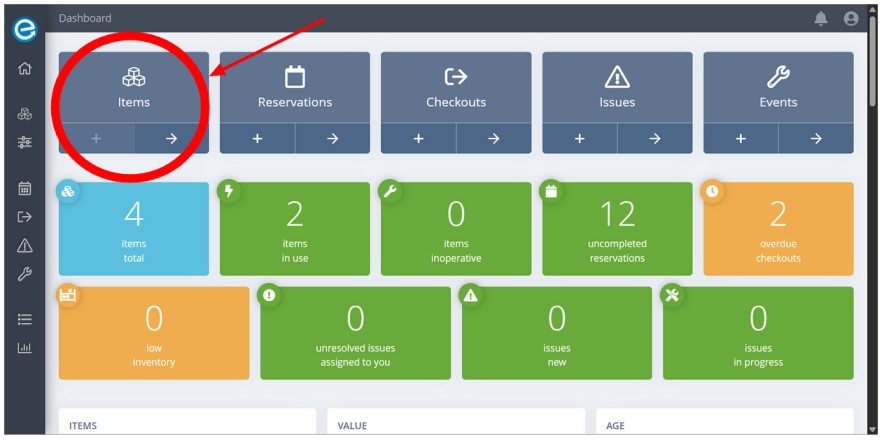
2. Easy Maintenance Scheduling
Maintenance isn’t just about fixing broken things; it’s about preventing issues before they become problems.
Itefy lets you schedule one-time or recurring maintenance, track issues, and view service history for each piece of equipment. You'll receive automatic reminders when tasks are due, making sure nothing slips through the cracks.
To use this feature, click on the “New Event” tab and add all the necessary details like the asset name, last maintenance date, next maintenance date, and other details.
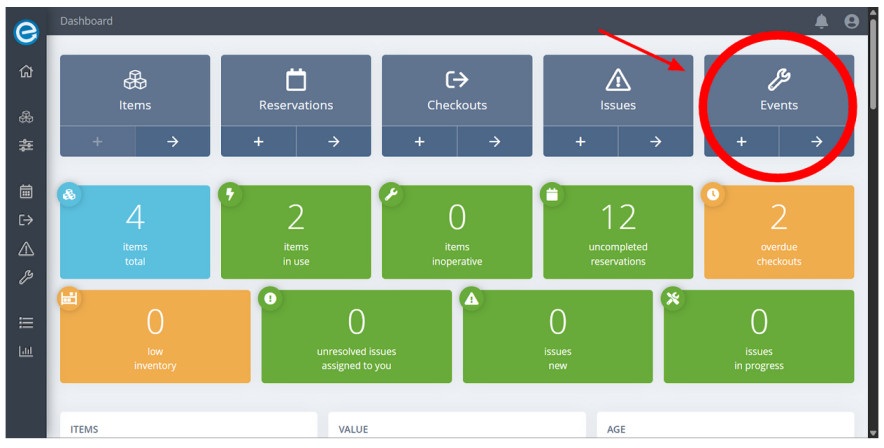
3. Reservation Planning
The checkout and asset reservation system helps you plan who’s using what and when. Whether reserving tools for a job site or managing refills and license renewals, Itefy ensures smooth coordination.
You can even create repeating bookings for predictable tasks. This reduces overlap, prevents double bookings, and maximizes equipment use. To use this feature, go to the “New Checkout” and “New Reservation” tabs and provide the details it asks for.
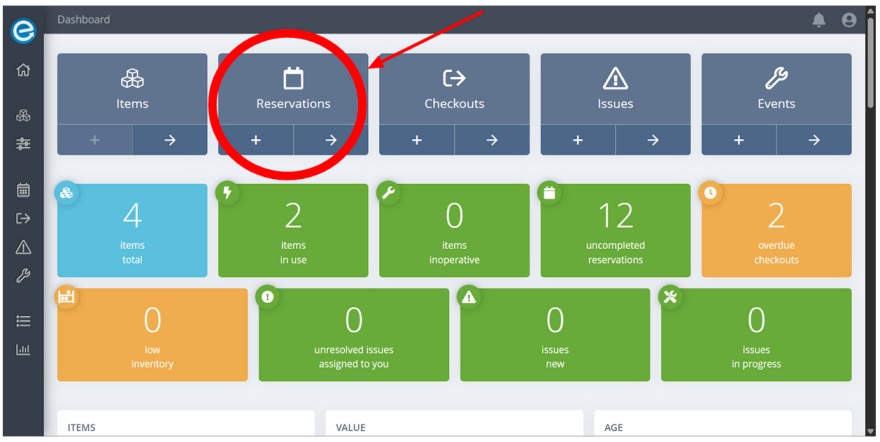
Take Full Control of Your Maintenance with Itefy
As businesses grow and operations become more complex, relying on manual spreadsheets for maintenance tracking just doesn’t cut it. To sum up the CMMS vs. manual spreadsheets debate, CMMS is clearly a better and smarter choice, especially in today’s fast-paced world.
If you’re ready to benefit from a smarter CMMS, make the switch to Itefy. With built-in features like maintenance logs, QR scanning, inventory tracking, and live dashboards, you’ll never wonder where your assets are or what condition they’re in.
Start your 14-day free trial today!
Frequently Asked Questions
-
Yes, most modern CMMS tools offer mobile apps or responsive dashboards. By using a CMMS, maintenance teams in the field can update equipment status, log issues, and check schedules without returning to a desktop.
-
Yes. Even small teams benefit from reduced downtime, better planning, and fewer lost assets. Over time, these savings often exceed the cost of the software, especially when factoring in fewer breakdowns and delays.
-
Spreadsheets are familiar, free, and easy to start with. Many teams stick with them out of habit or budget constraints despite long-term inefficiencies. CMMS adoption often comes once the business scales or compliance demands outgrow spreadsheets.