How Equipment Management Software Reduces Downtime
Don’t know how equipment management software reduces downtime? Read inside, and you’ll know why you should immediately get one for your company.
In this article:
- How Itefy’s Equipment Management Software Reduces Downtime
- 1. Real-Time Tracking
- 2. Proactive Maintenance Scheduling
- 3. Streamlined Reservation System
- 4. QR Code Integration for Error-Free Operations
- 5. Detailed Inventory Management
- The Financial Impact of Reducing Downtime
- 1. Cost Saving Through Proactive Maintenance
- 2. Improves ROI on Equipment Investments
- The Ripple Effect of Downtime Reduction
- How to Use Itefy For Reducing Machine Downtime
- 1. Account Registration
- 2. Add Equipment
- 3. Creating Check-out
- Don’t Let Downtime Control Your Business
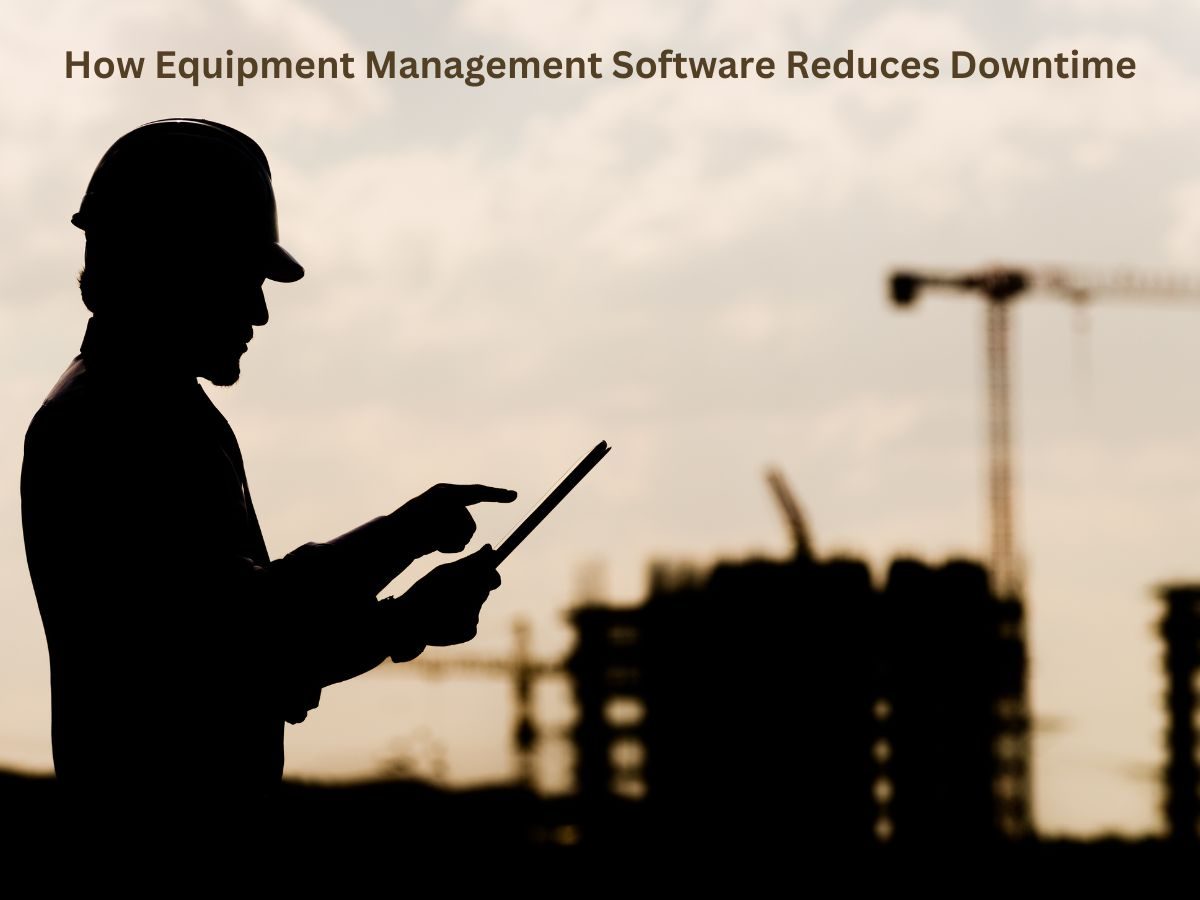
When equipment fails, companies suffer huge losses in terms of lost productivity, reduced revenue, and production capacity. What some companies don’t realize is that equipment downtime can easily be avoided by using the right tools as Itefy equipment management software.
With the right tool in place, you can track maintenance, schedule routine operations, and predict potential failures before they occur. Let’s take a closer look at how equipment management software reduces downtime and keeps your business operations running smoothly.
How Itefy’s Equipment Management Software Reduces Downtime
For industries that rely on equipment for daily operations, downtime can cause several challenges. Thankfully, Itefy is here to make all of that go away. With our tool, you can rest assured that all your equipment will be in optimal condition and ready for use. Here’s how it makes an impact:
1. Real-Time Tracking
One of the main causes of downtime is usually the inability to locate equipment when needed. But that is a thing of the past now, as Itefy eliminates this problem with features like:
- Location Tracking: This allows us to know exactly where the equipment is at all times, whether it's in use or in storage off-site in a facility.
- Checkouts and Reservations: Helps track who has the equipment in real time. You can see the check-out date as well as when it will be returned.
These features ensure that equipment is easily accessible whenever needed. There are no unnecessary delays or idle time, which significantly reduces downtime.
2. Proactive Maintenance Scheduling
The next problem that Itefy solves is unexpected equipment failures. Our tool provides all necessary maintenance management tools to help you stay one step ahead of the problem. These tools include:
- Automate Reminders: Stay informed about the production schedule and regular inspections, and receive alerts before maintenance is due.
- Issue Reporting: Allows users to report problems in real-time so that repairs can be handled immediately.
- Equipment Maintenance Log: For keeping a detailed record of repairs and servicing. It ensures compliance and predicts future maintenance needs.
As a business, when you get the ability to know when equipment can stop working, you can send it for maintenance and get it fixed or buy a new one before you start losing revenue. After all, protecting your revenue is what ultimately drives business success.
3. Streamlined Reservation System
Scheduling conflicts can become a significant problem, leading to equipment unavailability when needed most. However, with help from Itefy’s reservation system, companies can minimize downtime caused by poor scheduling or resource allocation.
Our tool ensures efficient use of all equipment through:
- Self-Service Reservations: Allows team members to book equipment in advance, ensuring it is available when needed.
- Conflict Resolution: Helps prevent double booking with real-time availability updates.
- Utilization Insights: Identifies underused assets and redistributes resources to help track inventory better.
4. QR Code Integration for Error-Free Operations
If there are any errors in tracking or managing equipment, it can delay important operations. So, for smoother flows, companies usually need a solution that simplifies most of the process and reduces the time wasted on administrative tasks and downtime. In such situations, Itefy’s QR code features help with:
- Quick Identification: Managers can check equipment availability, maintenance history, user details, and more by scanning a simple QR code.
- Error-Free Logging: To reduce manual input errors during checkouts and reservations.
- Faster Processing: Helps save time by instantly updating equipment status with a single scan.
5. Detailed Inventory Management
As a large business, managing the large inventory that occasionally comes in can be difficult. This can overwhelm the workers, as manually knowing what’s where is close to impossible. Itefy has covered this part as well, so the asset is always accounted for and available through the physical asset management system.
A couple of features that you can explore are:
- Equipment Database: With it, companies can easily centralize all equipment information in one place for easy access.
- Search and Filtering Tools: Assists in quickly locating specific items. It surprisingly saves a lot of time in urgent situations.
- Item Kits: For creating bundle-related equipment. Ideal for streamlined checkouts and reservations.
The Financial Impact of Reducing Downtime
It’s always great to keep downtime to a minimum, as it ensures optimal returns on investment (ROI) and enhances overall business efficiency. Let’s see what the actual impact would be if there’s no downtime.
1. Cost Saving Through Proactive Maintenance
If you’re not that good with numbers, remember that the average cost of unplanned downtime in manufacturing is $260,000 per hour. This means you’ll be losing this much money if your manufacturing machines stop working suddenly.
However, if you smartly manage your machines with proper maintenance, you’d be making much more than companies that do not. All because proactive maintenance is less expensive than emergency repairs. In fact, studies show that unplanned maintenance can cost around nine times more than planned maintenance.
2. Improves ROI on Equipment Investments
Every piece of equipment represents a financial investment. When equipment is underutilized or suffers frequent downtime, businesses fail to maximize their returns.
The situation is the complete opposite when businesses reduce downtime; it can do a lot of good, especially in terms of ROI. This is because equipment spends more time performing tasks that generate revenue.
Reducing downtime also enhances productivity. Operational efficiency translates to better throughput. For instance, a manufacturing plant operating with minimal downtime can fulfill orders faster and improve customer satisfaction.
Still not convinced? Many studies have been conducted to prove this point, one of which revealed that preventive maintenance can improve ROI by as much as 545%. |
The Ripple Effect of Downtime Reduction
Reducing downtime creates a ripple effect that extends beyond direct financial savings, including:
- Lower Labor Costs: Employees spend less time troubleshooting and more time on productive activities.
- Decreased Energy Waste: Faulty equipment often consumes more energy. It keeps machines in optimal condition and reduces utility expenses.
- Reduced Safety Incidents: Properly maintained equipment is usually safer, which minimizes costly workplace accidents and associated liabilities.
How to Use Itefy For Reducing Machine Downtime
Now that you’re aware of how equipment management reduces downtime, let’s discuss how you can use Itefy’s dashboard in the right way:
1. Account Registration
To test the full benefits of Itefy, click on the red “Try” button in the top right corner. This will take you to the sign-up page.
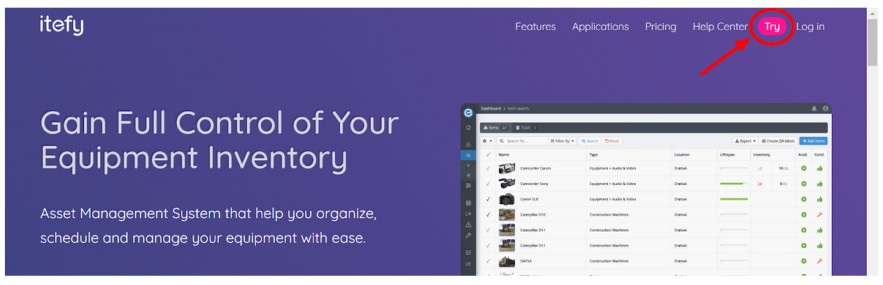
Itefy offers a 14-day free trial, so you have enough time to test it out and see how it can reduce downtime for your business. Enter your email address in the window that opens up and click “Start Free Trial.”
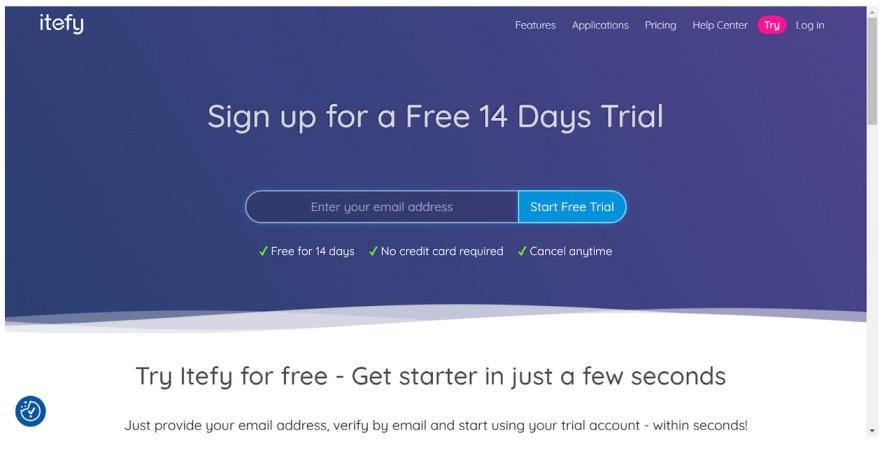
Finally, enter the code Itefy sent to your email address, and you’re in.
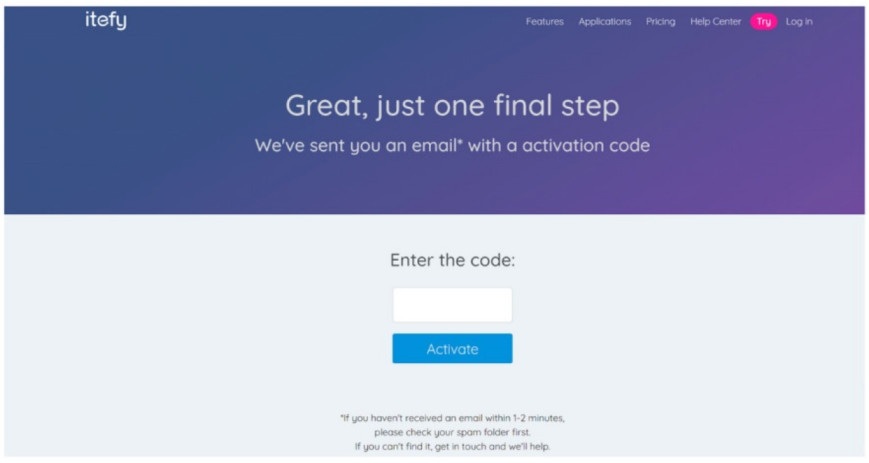
2. Add Equipment
The first step after signing up is to start adding items and creating a list of the equipment you have at hand. To do that, click on the “Add Items” tab with a “+” sign.
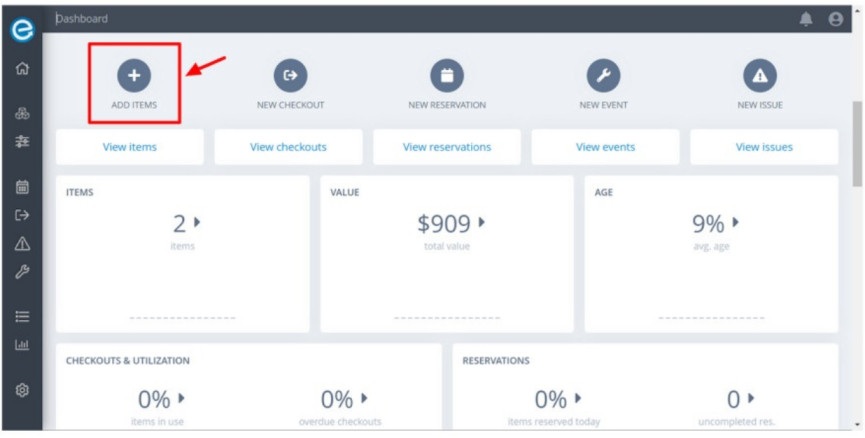
In the popup window, add the equipment's name and Unique ID. Then, under the “Item Type” drop-down menu, select the one that best suits your equipment.
If you cannot find a category that matches your needs, click on the “+” button and add a new one. Make sure to add its image, too, for easy identification later on.
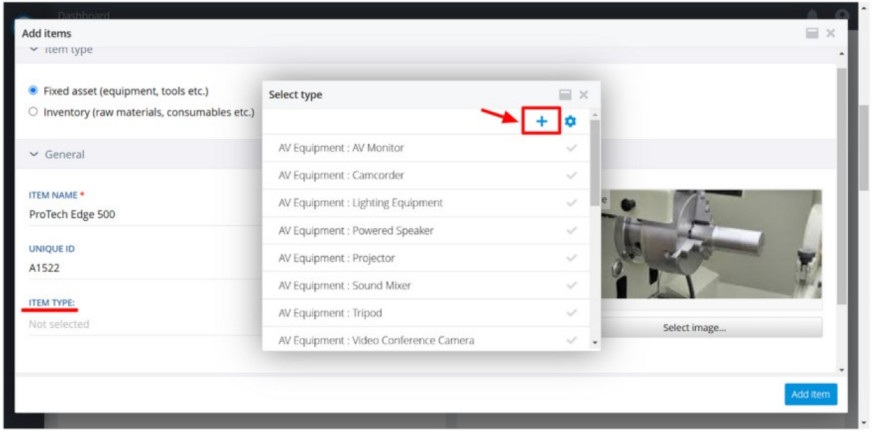
You’ll also have to add the Purchase Date, Expiry Date, Purchase Value, and Salvage Value for your item. It helps keep track of your equipment in emergency situations.
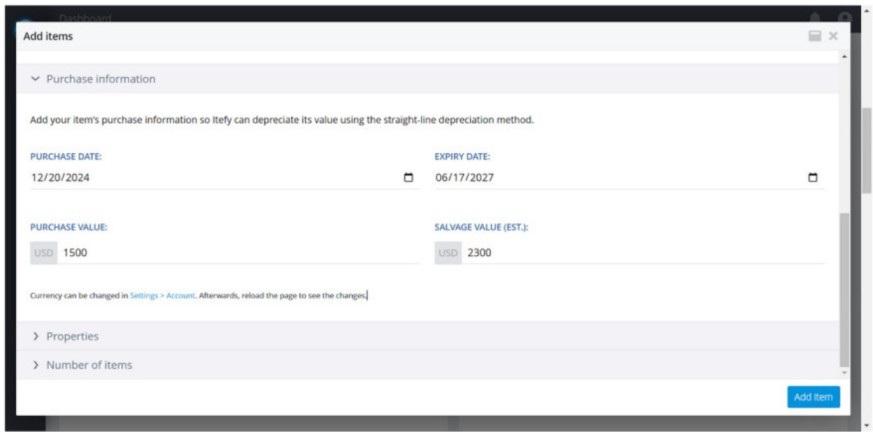
Fill in the other two dropdown menus, Properties and Number of Items, as well. Once you’re done, click the “Add Item” button in the bottom right corner.
3. Creating Check-out
Now, to the right of the Add Items section, you’ll find the “New Checkout” button. Tap on it to create a new checkout for the equipment in inventory.
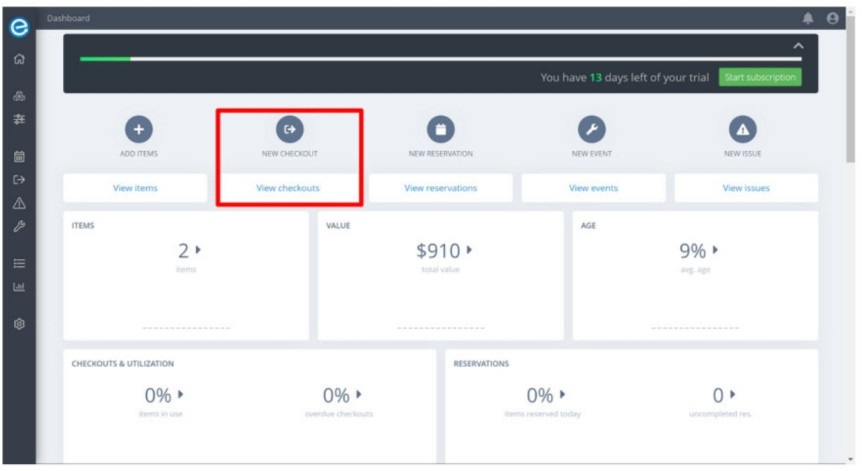
Alt Text: Itefy’s main dashboard.
A page will open where you can view already-created checkouts and create new ones by clicking the blue “Create New Checkout” or “+ New Checkout Buttons.”
In the popup window, add details such as “Reason for Checkout,” “Items to Check Out,” and “Return By Date”. You can also add other details like tags, the person assigned, the checkout location and any important information.

Once all the fields are filled out, click on “Checkout,” and you can send any equipment out of the inventory.
Don’t Let Downtime Control Your Business
That was all about how equipment management software reduces downtime. Remember, downtime is costly for nearly every industry, but it doesn’t have to be inevitable. With Itefy’s Equipment Management Software, you can take charge of your resources and significantly reduce downtime for your organization.
Its user-friendly interface and scalability make it a perfect fit for businesses of any size, which ensures your team has what they need to keep operations running smoothly. So whether you’re managing a single facility or thousands of assets, Itefy helps minimize disruptions and maximize productivity.
Are you ready to optimize your operations? Explore Itefy today and take charge today with Itefy. Request a demo now!
Frequently Asked Questions
-
Yes, advanced systems use predictive analytics based on historical and real-time data to forecast potential equipment failures. This allows organizations to intervene in a timely manner and minimize unplanned downtime.
-
Yes, many solutions, like Itefy, offer scalable pricing that works perfectly with small businesses. This makes it an accessible option for companies looking to enhance their equipment management without large upfront investments.
-
Some solutions provide offline capabilities and allow users to track and log equipment usage even in areas with limited connectivity—data syncs automatically once the connection is stored.