How to Reduce Downtime and Increase Output with Effective Equipment Management?
Want to reduce downtime? Explore how equipment management strategies with Itefy software, enhance productivity and save up to 40% on maintenance.
In this article:
- Why It’s Important to Reduce Equipment Downtime?
- 6 Proven Equipment Management Strategies to Reduce Downtime
- 1. Schedule Regular Preventive Maintenance
- 2. Performing Equipment Audits Timely
- 3. Conduct Routine Inspections
- 4. Track the Downtime Reasons
- 5. Ensure Quick Access to Spare Parts
- 6. Train Your Employees
- Enable Notification Alert for Smart Monitoring!
A study has revealed that one hour of equipment downtime can cost $260,000. Losing such a substantial amount in just one hour is a blow no business can afford, regardless of size or industry. This highlights the importance of reducing equipment downtime.
Fortunately, achieving this goal is now possible by following proven equipment management strategies. These strategies, which include scheduling regular maintenance, tracking downtime, and many more, can be easily executed using equipment management tools such as Itefy. Come with us as we’ll explain how it’s possible to ensure long-term success.
Why It’s Important to Reduce Equipment Downtime?
Equipment downtime, even for an hour, can be incredibly costly for a company, often exceeding the cost of planned downtime by more than tenfold. Unplanned downtime, not only disrupts operations but also impacts deadlines and leads to revenue loss.
All of these disruptions in business operations can erode client trust and make it harder for a company to maintain a good reputation in the market. This is why it's extremely crucial to reduce equipment downtime by following equipment management strategies.
Following the right strategies can help the business identify the potential issues before they become a major obstacle in the future. They contribute in saving repairing costs, and enhance productivity of the employees.
6 Proven Equipment Management Strategies to Reduce Downtime
Here are the six proven equipment management strategies that reduce downtime.
1. Schedule Regular Preventive Maintenance
Preventive management is one of the most successful equipment management strategies for reducing downtime. It not only reduces downtime by an average of 17.8% but also helps businesses save costs up to 40% over reactive maintenance.
The strategy involves scheduling regular maintenance activities to identify and address potential issues before they become a huge problem. With tools like Itefy, this process has become easier than ever.
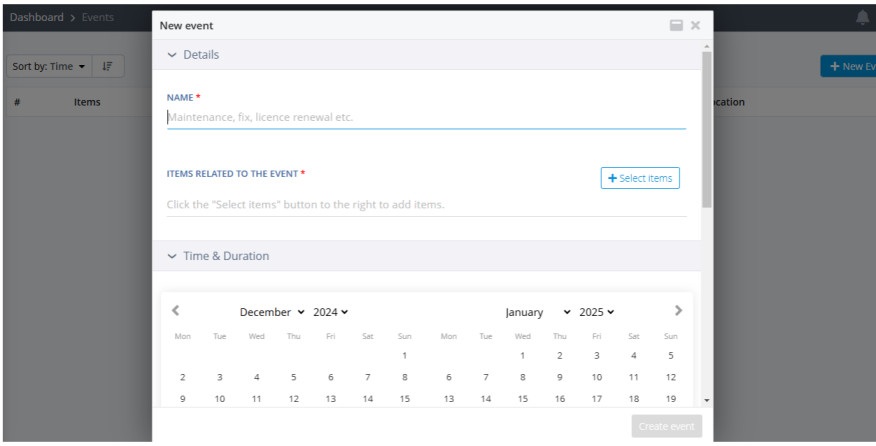
Itefy users can easily set up maintenance events, specifying the date, time, and other details while assigning the task to a team member. When the time comes, the tool will remind assigned team members about the responsibility to ensure maintenance is carried out on time.
2. Performing Equipment Audits Timely
Equipment or asset management audits are the comprehensive inspection of machinery used in the business facility. This ensures equipment is functioning at its best and helps identify what needs maintenance, which equipment should be replaced, and how to extend its lifespan.
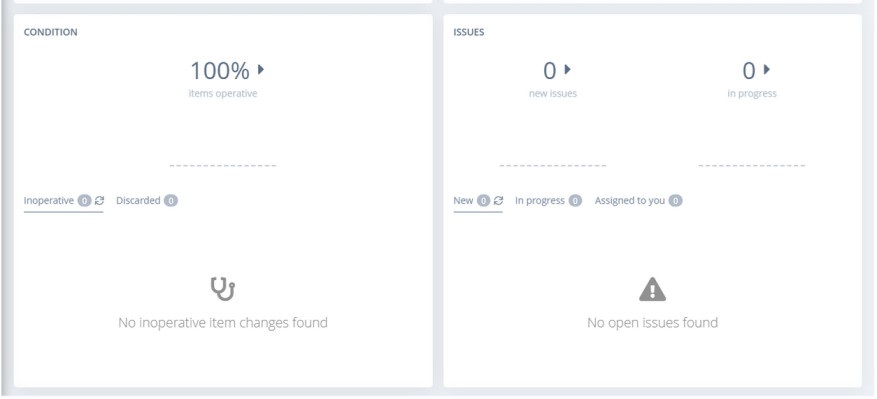
For instance, by performing timely audits using Itefy, you can track the history of your equipment and identify the machines that have required frequent repairs over the past few months. The pattern indicates the equipment may be prone to future breakdowns, allowing you to take proactive measures before it stops working without warning.
3. Conduct Routine Inspections
It’s also crucial to conduct routine inspections to reduce equipment downtime. These routine inspections go beyond regular maintenance and involve detailed checks of all machinery to ensure everything is functioning properly.
During routine inspections, the inspector performs a thorough functional test for equipment to verify all parts are operating optimally. They also assess the overall condition of the equipment and identify any signs of wear or potential issues. All of these findings are then updated in equipment management software to ensure smooth and uninterrupted operations.
4. Track the Downtime Reasons
The next equipment management strategy is tracking the downtime reasons. This process helps businesses understand why equipment fails and what they can do to resolve such challenges. Equipment management software like Itefy simplifies this tedious job by providing features such as ‘Issues.’
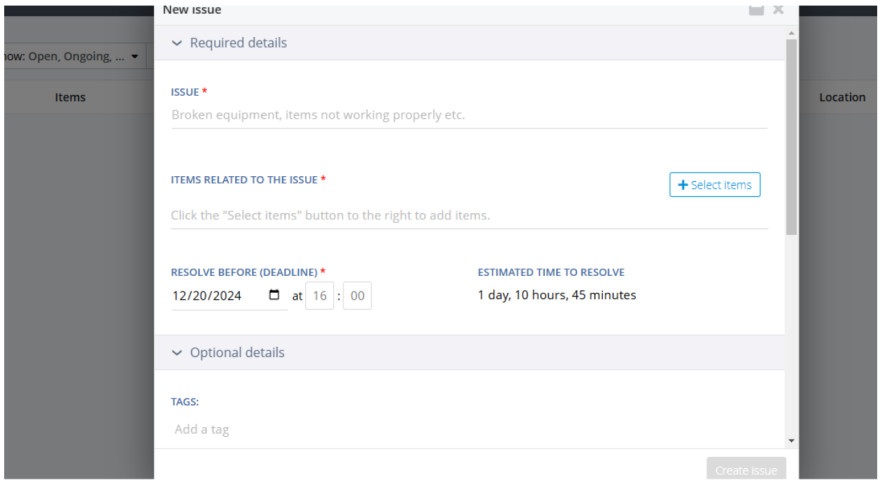
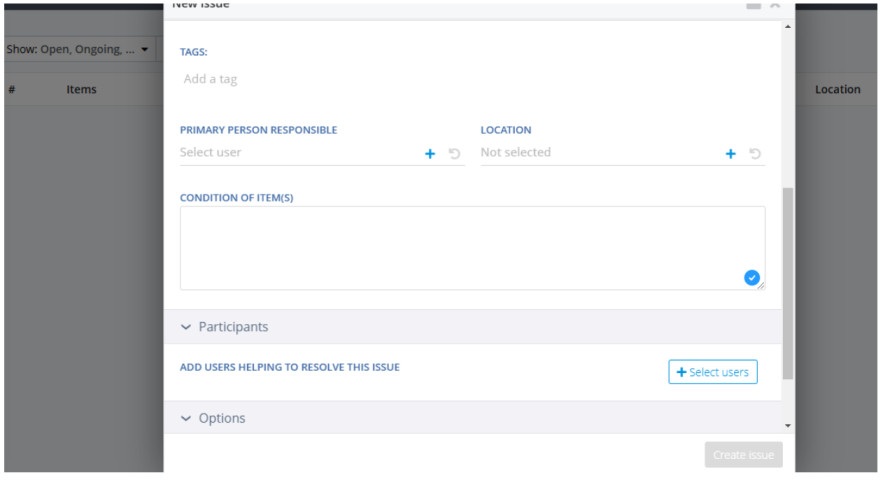
Team members (employees using the equipment) can create detailed tickets (New Issues) to record information for any problem encountered. For instance, naming the issue, adding the date of occurrence, details about the condition of items, the primary person who’s responsible, location, etc.
Once the ticket is created, the information is stored in the system’s database, making it easily accessible to the responsible parties. This allows them to identity the root cause and take the necessary steps to resolve without delay.
5. Ensure Quick Access to Spare Parts
Maintaining quick access to spare parts is also an effective strategy to reduce downtime. Having a readily available inventory of spare parts guarantees that repair technicians can fix the issues promptly without halting operations for hours.
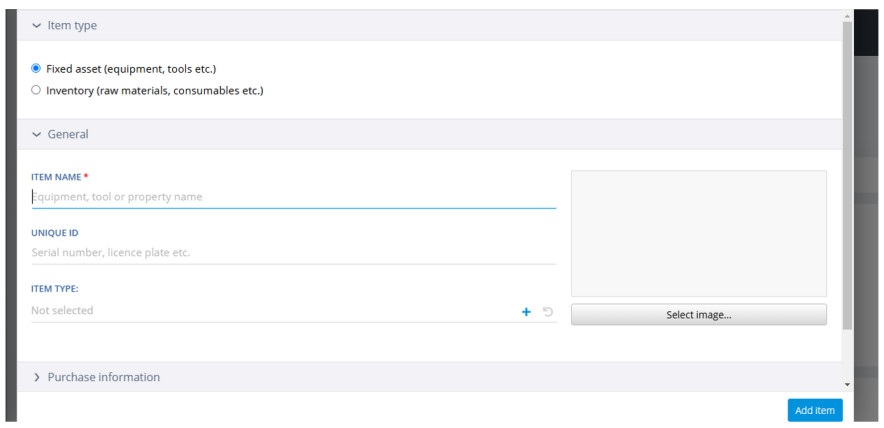
Companies should establish a check-in and check-out system for spare parts using an equipment management tool. Such an approach allows the team to track part usage, monitor stock levels, and plan for replenishment as needed.
6. Train Your Employees
Training employees to use equipment management software and follow best practices are also crucial. Studies show that companies providing proper training see a 17% increase in productivity. By offering training sessions, you ensure your team knows how to update tools and follow rules and regulations. They’ll learn how to track equipment performance, report issues, and carry out maintenance tasks to smooth operations and boost productivity.
Enable Notification Alert for Smart Monitoring!
After discussing the proven strategies for equipment management, here’s an important suggestion: enable Itefy notification feature for real-time insights. This is one of the most effective practices to avoid unplanned downtime, as it ensures you’re reminded about maintenance and repairing at the right time.
Rest assured, the notifications won’t be overwhelming.
Our software offers smart notifications, sending alerts only to the designated team members responsible for the task. This targeted approach ensures that only the right people receive the updates, which makes business operations less stressful and reduces downtime as well.
Sign up today and get notified when it's time for maintenance.
Frequently Asked Questions
-
To keep and maintain equipment effectively, it’s crucial to use equipment management software. These tools allow the employees to keep track of maintenance schedule, monitor equipment performance, and log issues whenever they arise. Additionally, they’re also helpful for repairing technicians, as they can access the history of each equipment with just a simple scan.
-
The correct way to measure equipment downtime is by using this formula:
(Time the asset is not working/Total time) x 100.
For instance, if a machine is available for 80 hours a week and the downtime is 20, the downtime percentage would be (20/80) x 100 = 25%. -
The downtime of equipment means the amount of the time equipment or machinery isn’t used. This can occur for various reasons, including lack of proper maintenance, wear and tear, unexpected breakdowns, or improper usage by employees.