Reactive Maintenance Explained: A Guide to Run-to-Failure Maintenance
Reactive maintenance is a run-to-failure strategy in which repairs are only performed once an asset breaks down. Here’s what this method is all about.
In this article:
- What Is Reactive Maintenance
- Difference Between Planned and Reactive Maintenance
- Planned Maintenance
- Reactive Maintenance
- Types of Reactive Maintenance
- 1. Corrective Maintenance
- 2. Emergency Maintenance
- 3. Deferred Maintenance
- 4. Run-To-Failure Maintenance
- Reactive Maintenance Advantages and Disadvantages
- Conclusion
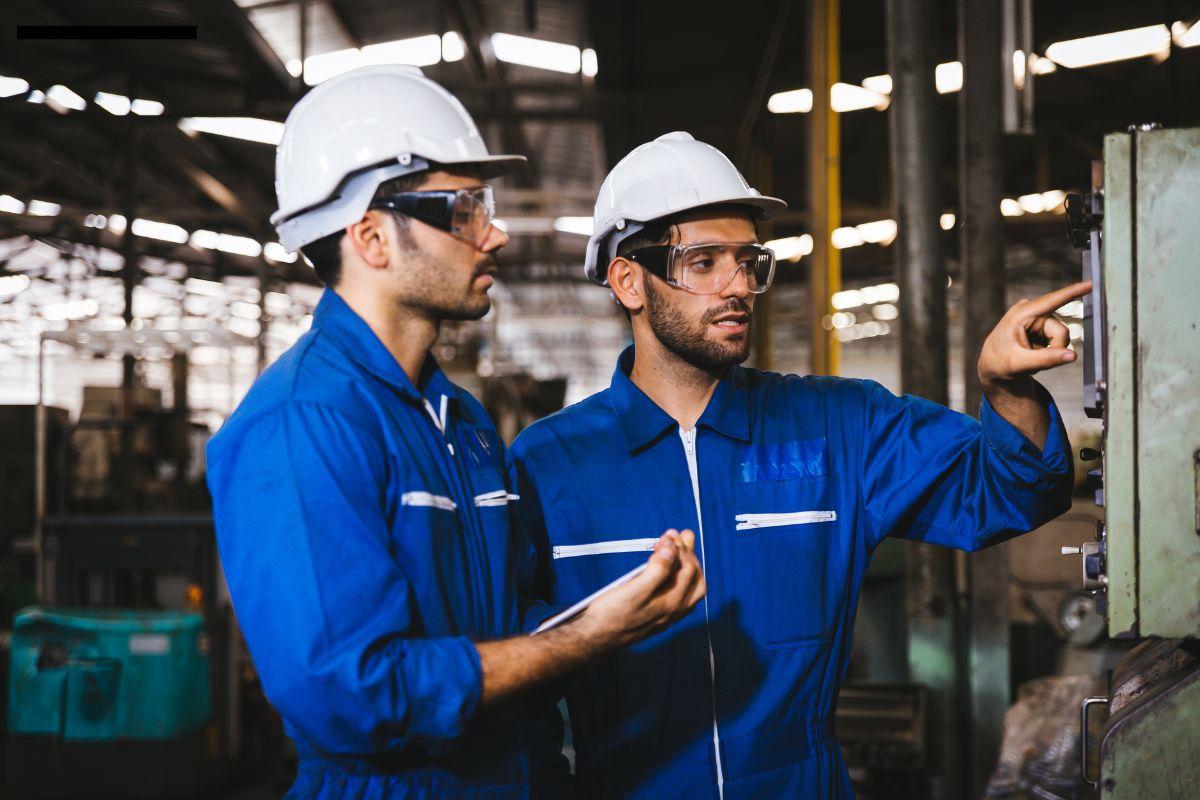
Maintenance is a crucial aspect of any asset management strategy, ensuring that machinery and equipment are always in good working condition. Yet, despite the best-laid plans and predictive maintenance strategies, many companies still find themselves dealing with unexpected breakdowns and malfunctions.
This is where reactive maintenance comes in, a “run-to-failure” approach that believes in fixing things only after they break. It might sound counterintuitive, but the reactive approach is still used in many industries. Around 80% of plant maintenance managers trust reactive maintenance to keep their units running.
This method reduces the need for regular maintenance checks and costs and requires resources only when an issue arises.
What Is Reactive Maintenance
Reactive maintenance, also known as “breakdown maintenance,” is a strategy in which maintenance checks are performed only after equipment or machinery has failed. Unlike preventive maintenance, which is based on anticipating equipment issues before they occur, reactive maintenance is all about fixing problems as they arise. The basic principle here is: “If it isn’t broken, why fix it?”
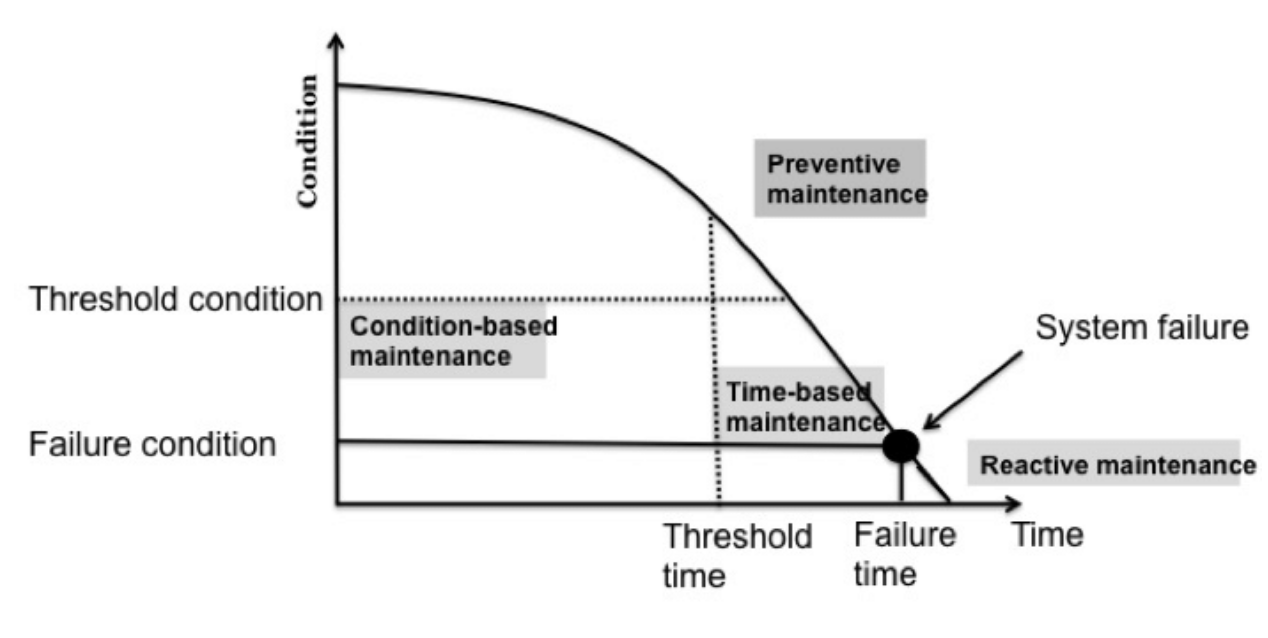
Preventive Versus Reactive Maintenance
In a reactive approach, you wait for machinery to malfunction or break down and then repair or replace it. It works best for low-cost or non-critical assets not directly tied to your production or safety. For example, it might make more sense for an office printer to experience a paper jam before replacing it rather than conducting a detailed investigation (preventive method).
Difference Between Planned and Reactive Maintenance
Planned Maintenance
Planned or preventive asset maintenance focuses on avoiding unexpected failures and asset breakdowns through predictive and preventive strategies. In a planned approach, technicians use work orders, maintenance history, and performance records to spot problems before they lead to asset breakdowns. For example, regular oil changes and servicing of vehicles, software updates for IT systems, and routine cleaning of HVAC units.
Planned maintenance uses asset health monitoring, machine learning, and data analytics to perform regular and systematic inspections, servicing, and upkeep of equipment. Because it helps you detect problems in advance to improve the life of assets, this method is also called “proactive maintenance”.
Reactive Maintenance
Reactive maintenance, also known as breakdown or run-to-failure maintenance, involves performing repairs after an asset malfunctions or stops working. A reactive maintenance example may be fixing an elevator once it stops working or repairing a conveyor belt on a productive line only after it snaps.
The reactive approach is based on the belief that:
Downtime Costs + Repair Costs < Preventive Maintenance Costs
Reactive maintenance states that the costs incurred during asset downtime (lost productivity, revenue loss, labor costs) and repair are less than those of preventive maintenance.
Aspect | Planned | Reactive |
Definition | Addresses potential problems before they lead to failures | Focuses on fixing equipment breakdowns after they occur |
Downtime | Shorter, scheduled downtimes | Longer, unpredictable downtimes |
Cost Analysis | Regular costs for inspection and upkeep, but saves money in the long run | Lower ongoing costs but higher expenses due to emergency repairs |
Risk | Lower risk of sudden failures; improves reliability | Higher risk of unexpected breakdowns; impacts operations |
Planning | Scheduling routine checks, servicing, and replacements even without a failure | No prior scheduling or planning |
Safety | Improves workplace safety through regular maintenance checks | Higher safety risks due to sudden malfunctions |
Types of Reactive Maintenance
1. Corrective Maintenance
Sometimes, equipment shows signs of wear and tear that have not yet escalated into malfunction or breakdown. For example, a motor in an industrial machine begins to overheat because of a problem with the cooling fan. In this case, the motor failure has not occurred yet, and correction can be implemented to restore the optimal condition of the asset.
2. Emergency Maintenance
This is a type of reactive maintenance where urgent and immediate repair sessions need to be scheduled to address sudden failures. These tasks demand high priority and often have a higher cost due to the urgent allocation of resources, like overtime labor. Here’s when a routine reactive maintenance task receives the “emergency” status:
- Safety Hazards: Any failure that poses a safety risk to the office personnel, customers, or the public. For example, a chemical leak in a manufacturing plant.
- Operational Disruption: Breakdowns that pause high-priority business operations or disrupt the workflow (and productivity), like a conveyor belt failure in a production line.
- Critical Equipment: Equipment failures that are essential to the core operations of an entity, such as the malfunction of refrigerators in a food storage unit.
- Compliance Issues: Asset breakdowns that lead to non-compliance with industry standards, potentially leading to fines (eg, fire suppression systems in a high-risk area).
3. Deferred Maintenance
Deferred maintenance is when necessary repairs or maintenance checks are postponed (or deferred) by an organization to a later date. The reasons may vary, from a lack of resources and budget constraints to prioritization of other pressing issues. In deferred maintenance, you delay the repair of non-critical assets or implement temporary band-aid fixes — and repair later.
However, this type of reactive maintenance may reduce the service life of an asset and prevent optimal performance. It also increases the long-term maintenance costs of an asset by up to 4 times, with a $4 expense for every $1 saved.
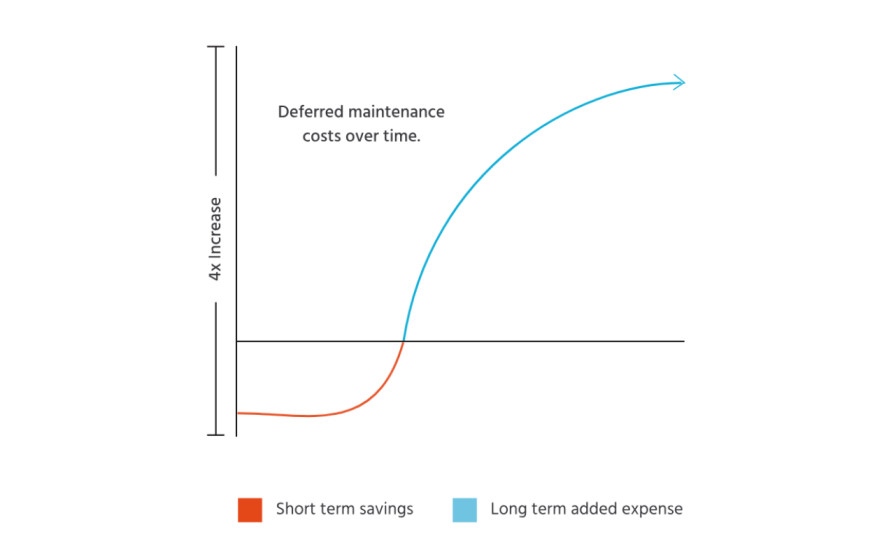
Increasing Cost of Maintenance When Doing Deferred Maintenance
4. Run-To-Failure Maintenance
In a run-to-failure approach, equipment is intentionally allowed to operate until it fails. Once an asset stops running, repairs or replacements are scheduled to restore functionality, but no prior maintenance is performed in advance. This maintenance method is usually used in low-cost or non-critical assets whose downtime doesn’t have a major impact on operations. It’s wise to let fax machines and light bulbs operate until they no longer can — rather than scheduling routine maintenance and absorbing the subsequent costs.
Reactive Maintenance Advantages and Disadvantages
While a reactive management style helps companies avoid the short-term cost of asset upkeep and maintenance, it leads to high long-term expenses. These are caused due to unplanned breakdowns, subsequently leading to a loss of productivity and revenue with increased labor costs. Let’s look at the advantages and disadvantages of reactive maintenance in a table:
Advantages | Disadvantages |
Less planning required for staff training and maintenance checks | Requires immediate and often unplanned strategies after failure |
Resources are only used when necessary | Needs quick access to spare parts and skilled labor |
No planned downtime or disruptions for maintenance | Potentially prolonged, unpredictable downtime post-failure |
Lower implementation costs due to no regular inspections or servicing | Predicting and budgeting for maintenance costs can be difficult |
No need for scheduling regular maintenance checks, saving on admin and labor costs | Regular breakdowns and emergency repairs may shorten the life of an asset |
Ideal for managing low cost or non-critical assets not directly related to production | Sudden equipment failures can pose safety risks to workers |
Conclusion
Reactive maintenance involves a “fix it after it breaks” approach that eliminates the need for routine servicing and inspection of equipment. Although the approach simplifies management and has lower initial costs, the disadvantages are worth considering too. A reactive maintenance strategy leads to unplanned downtime, higher long-term expenses, and even safety risks.
If you want to manage your assets efficiently and avoid the drawbacks of a purely reactive outlook, choose advanced asset management solutions like Itefy. The platform is home to a comprehensive suite of tools that help you organize, schedule, and manage your assets on the go. With Itefy, you can keep your equipment from breaking down and extend asset lifespan while improving asset utilization.
So, start your free trial with Itefy today to ensure your assets are always up and running!