A Complete CMMS Implementation Guide
Uncover the exact steps, insider tips, and common mistakes you should avoid for a smooth CMMS implementation and successful rollout.
In this article:
- What is CMMC Implementation and Why It Matters
- How Does CMMS Implementation Work?
- Step #1: Define Clear Goals and Success Metrics
- Step #2: Build Your Implementation Team
- Step #3: Audit and Clean Your Existing Maintenance Data
- Step #4: Choose the Right CMMS Software for Your Needs
- Step #5: Configure the System for Your Workflows
- Step #6: Migrate and Verify Your Data
- Step #7: Train Your Team the Right Way
- Common CMMS Implementation Challenges
- 1. Lack of Planning
- 2. Poor Data Quality and Migration
- 3. Inadequate Training and Support
- 4. Lack of Post-Implementation Evaluation
- Put Your CMMS Plan into Action with Itefy
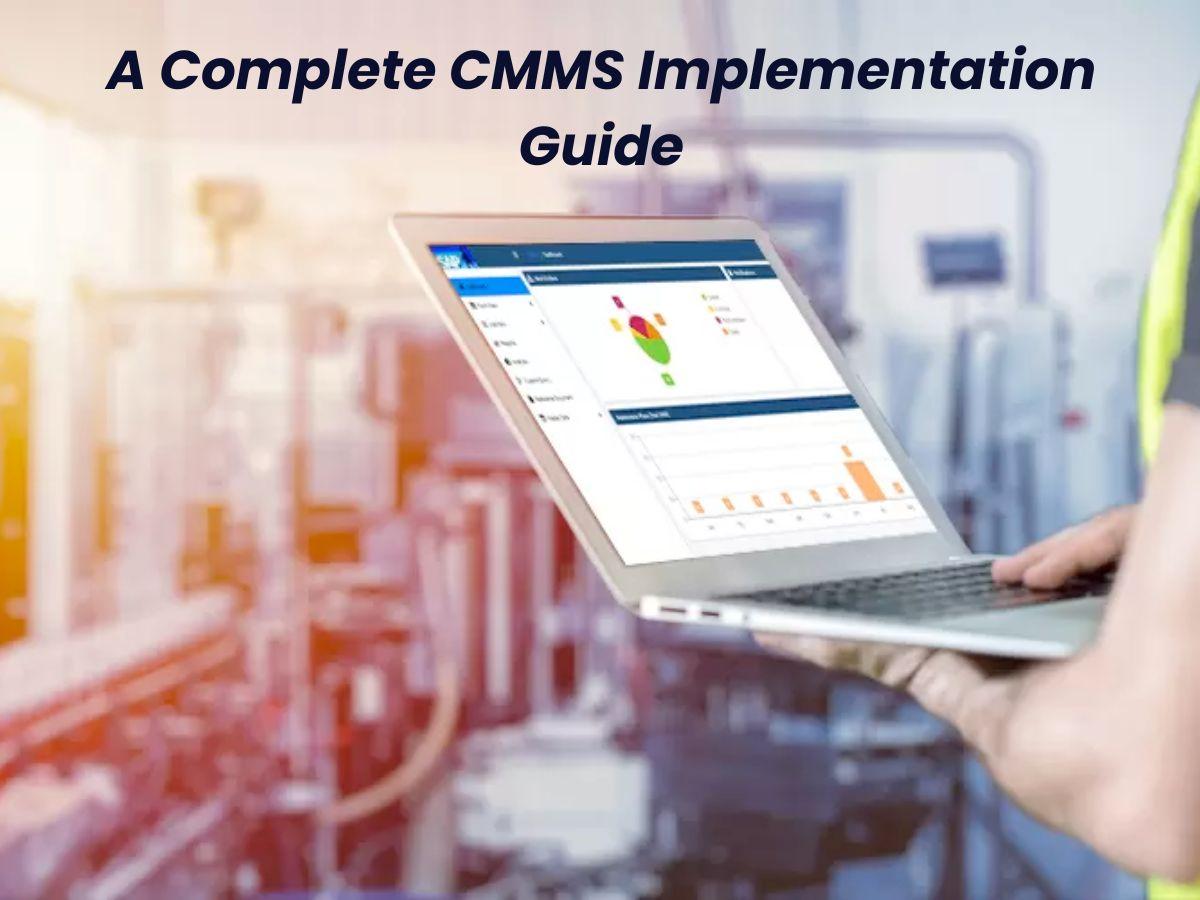
CMMS implementation can feel like an overwhelming task. Between day-to-day operations and backlogged work orders, where do you even start?
You’re not the only one asking that question. A survey showed that over 50% of organizations said their biggest challenge in adopting a CMMS was poor implementation planning. And the truth is, without a clear strategy, even the best software won’t deliver results.
But here’s the good news: It doesn’t have to be that way.
By the end, you'll know exactly what to do, when to do it, and how to make your CMMS work for you.
What is CMMC Implementation and Why It Matters
Implementing a CMMS (computerized maintenance management software) is the process of setting up, configuring, and launching your system so that it actually supports your daily workflows and long-term goals. It includes everything from defining your maintenance objectives, cleaning your data, training your team, and monitoring adoption.
It matters because poor implementation is the number one reason CMMS tools fail. In fact, up to 70% of CMMS installations underperform or fail outright — not because of the software but because of issues during setup and adoption.
In short, CMMS implementation is the foundation of your entire maintenance strategy. Do it right, and your team runs smoothly, reacts faster, and plans smarter.
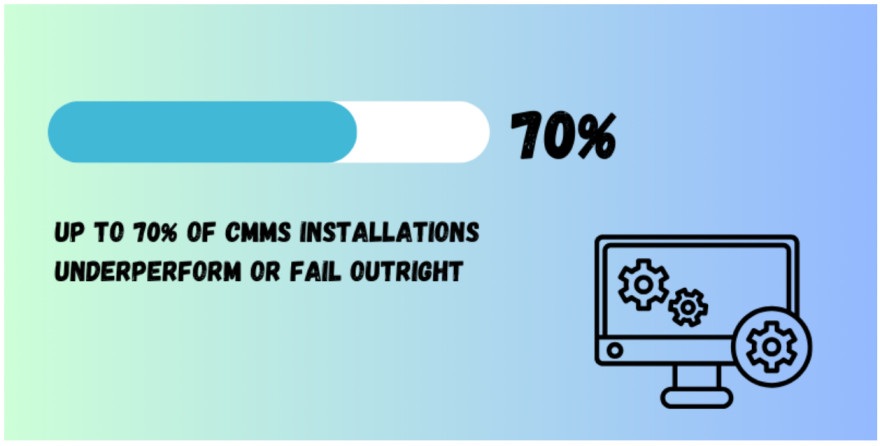
Source: Click Maint
How Does CMMS Implementation Work?
Here’s how you can implement a CMMS software in your business and make things smooth:
Step #1: Define Clear Goals and Success Metrics
Before you even touch your CMMS software, take a step back and ask: What exactly do we want this system to do for us?
Without clear goals, you risk setting up a system that doesn’t align with your team’s expectations and ends up underused or misconfigured.
The best way to approach this is by setting SMART goals. It means the goals you’re setting should be Specific, Measurable, Achievable, Relevant, and Time-bound.
It will help you:
- Choose the right features to configure
- Determine which users need what level of training
- Evaluate the return on investment (ROI) over time
- Keep your team focused and motivated through rollout
Step #2: Build Your Implementation Team
Once your CMMS goals are set, it’s time to bring the right people together. A successful implementation is never a one-person job; it requires input from multiple departments, each with different responsibilities.
Think of this as assembling your "project launch crew." Everyone needs to know their role from day one. Start by listing the key departments affected by the CMMS, including maintenance, IT, operations, and more. Choose a representative for each department who can help with setup and testing.
After selecting a team, host a project kickoff meeting. In this meeting, review the goals, assign clear responsibilities, set a timeline, and align expectations.
Step #3: Audit and Clean Your Existing Maintenance Data
Before entering anything into your new CMMS, take time to clean up your current asset maintenance data. If you move forward with outdated, inconsistent, or incomplete info, your system will never work the way it should, no matter how good the software is.
To do this, follow the steps below:
- Collect existing records: This includes spreadsheets, paper logs, or previous systems. Make sure to focus on assets, PM schedules, parts lists, and open work orders.
- Delete duplicates and outdated assets: Remove anything no longer in use or that won’t be tracked going forward.
- Standardize your naming: Make sure assets, locations, and parts follow a clear format.
- Fill in the blanks: Add missing info like model numbers, install dates, warranty status, and assigned locations.
- Start small if needed: If cleaning everything at once feels overwhelming, start with your most important equipment first.
Step #4: Choose the Right CMMS Software for Your Needs
Now it’s time to find a system that actually fits your workflows. You can either start by shortlisting CMMS vendors or directly go to Itefy and test one of the best CMMS tools currently available.
Make sure to look for must-have features based on your use case, e.g., preventive maintenance scheduling, mobile access, parts tracking, asset hierarchies, or reporting tools.
Also, check for integration options, such as if it would connect to your ERP, building systems, or the IoT sensors. Afterward, compare support and training to analyze whether it’s the best solution or not.
Bonus tip: Don’t just buy the biggest name. Choose the software that your team will actually use and benefit from.
In fact, a study revealed that 74% of maintenance professionals believe that CMMS improves productivity. That’s why it’s important to choose a reliable and highly-rated CMMS like Itefy.
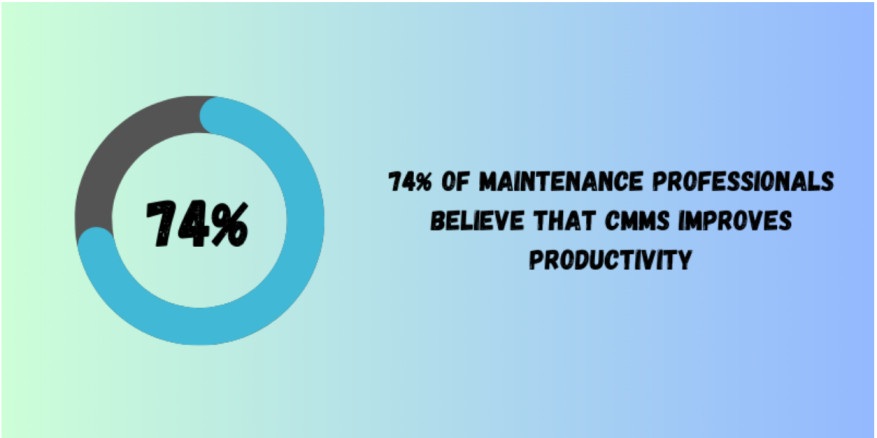
Source: WorkTrek
Step #5: Configure the System for Your Workflows
It’s important to configure the software according to how you want it to work, and not the other way around. With Itefy, you can easily add inventory, schedule maintenance, add asset reservations, and much more.
To add an inventory item, go to the dashboard and click on the “New Item” button (just like in the image below). After that, fill in all the required details, and you’re all set up. It’s the same steps for every other button, “New Checkout”, “New Reservation”, and others.
Here’s how you can perform this step:
- Set up your asset hierarchy: Start with locations → buildings → systems → equipment. Keep it clean and logical.
- Set up standard work order types: Create order types such as PM, emergency repair, inspections. Predefined fields to avoid guesswork.
- Add users and roles: Assign permissions based on responsibilities (techs, managers, admins).
- Load your preventive maintenance schedules: Use manufacturer recommendations or your intervals.
- Input spare parts and suppliers: Include part numbers, stock levels, reorder points, and vendors.
Step #6: Migrate and Verify Your Data
Begin with core items like assets, users, and locations. Add PMs, parts, and work orders next. Moreover, use templates from your vendors, as most of them offer import spreadsheets. Stick to their format to avoid upload errors.
Then, spot-check a sample of assets and PMs in the live system. Make sure the right data shows up in the right places. If something is imported incorrectly, fix it before adding more.
Step #7: Train Your Team the Right Way
Even the best CMMS won’t deliver results if your team doesn’t know how to use it. The key here is role-based, hands-on training that’s simple, relevant, and consistent. Here’s how you can succeed:
- Train by role: Techs need to know how to receive, update, and close work orders. Managers need to run reports and schedule PMs. Don’t overload everyone with features they won’t use.
- Use real tasks: Don’t rely on generic demos. Give your team hands-on experience with their daily workflows.
- Keep it short and simple: Break training into small sessions. A 20-minute targeted session is more effective than a 2-hour lecture.
- Document the process: Create a simple internal how-to guide or screen recording for future use and new hires.
- Offer support after training: Be available for questions in the first few weeks. The more supported your team feels, the faster they’ll adopt the system.
Common CMMS Implementation Challenges
Even with the best plans, many CMMS projects run into issues that delay rollout or limit long-term success. By recognizing the common mistakes early, you can save time, money, and the frustrations that come with it.
1. Lack of Planning
Jumping into CMMS implementation without thorough planning often leads to misaligned objectives and resource misallocation. Without a clear roadmap, organizations may encounter scope creep, budget overruns, and missed deadlines.
Research also indicates that more than 31% of IT software implementation projects are canceled before completion, often due to inadequate initial planning.
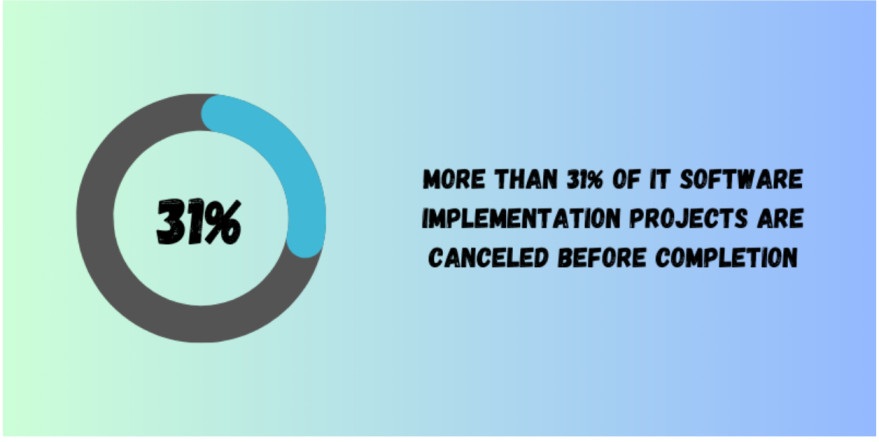
Source: Empaxis
2. Poor Data Quality and Migration
Migrating inaccurate or incomplete data into the new CMMS can compromise system reliability and decision-making processes. Issues such as data duplication, outdated information, and inconsistent formats can hinder system performance.
3. Inadequate Training and Support
Insufficient training can leave users unprepared to utilize the CMMS effectively, leading to errors, frustration, and decreased productivity. Ongoing support is also crucial to address issues as they arise.
4. Lack of Post-Implementation Evaluation
Failing to monitor the CMMS’s performance after implementation can result in unnoticed issues and missed opportunities for optimization. Without regular evaluations, the system may not evolve with the organization’s changing needs.
Many organizations do not establish key performance indicators (KPIs) during the planning phase, which is why they often struggle to assess the system’s effectiveness.
Put Your CMMS Plan into Action with Itefy
By now, you should know that CMMS implementation isn’t just about installing software, it’s about building a smarter, more accountable maintenance operation.
But here’s the truth: Even the best-planned implementation can fall flat without the right tool in place.
And that’s where we come in.
Itefy can help you track assets, schedule maintenance, manage inventory, and streamline equipment checkouts — all in one easy-to-use platform.
Start your free trial today and see how Itefy can turn your CMMS goals into measurable results!
Frequently Asked Questions
-
Definitely. With mobile access, your technicians can update work orders, add notes, and check parts from the field. This way, they save time and ensure the data is accurate in real time. So, always choose a CMMS that has a powerful mobile app.
-
Yes, even small teams with just a few technicians can gain huge benefits by using CMMS. These include better scheduling, fewer surprises, and strong reporting. Many modern CMMS tools are lightweight and built for small operations as well.
-
It depends on your organization’s size, but most CMMS implementations take 1 to 3 months. Clean data and solid team coordination can speed this up. Make sure not to rush things and test the software thoroughly before its official launch.