Manual Asset Location Tracking: A Simple Way SMBs Can Monitor Assets
Want to track assets without pricey GPS tools? Discover how manual asset location tracking provides SMBs with an affordable and reliable way to stay in control.
In this article:
- Key Takeaways
- What is Manual Asset Location Tracking?
- Benefits of Manual Asset Location Tracking for SMBs
- 1. Affordability
- 2. Flexibility in Any Environment
- 3. Accountability and Ownership
- 4. Simplicity and Speed
- 5. Customizable for Your Needs
- Why do SMBs Lose Track of Assets in the First Place?
- How SMBs Can Apply Manual Asset Location Tracking Daily
- 1. Field Service Teams
- 2. Retail or Warehousing
- 3. Logistics and Delivery
- 4. Construction and Contracting
- Tools That Make Manual Tracking Easier
- 1. Digital Spreadsheets
- 2. Paper Logs
- 3. Team Communication Tools
- Common Mistakes to Avoid and How
- 1. Not Assigning Accountability
- 2. Overcomplicating the System
- 3. Forgetting to Review Logs
- 4. Failing to Train the Team Properly
- How Far Can Manual Tracking Really Take You?
- Take Control of Your Assets Before It Costs You
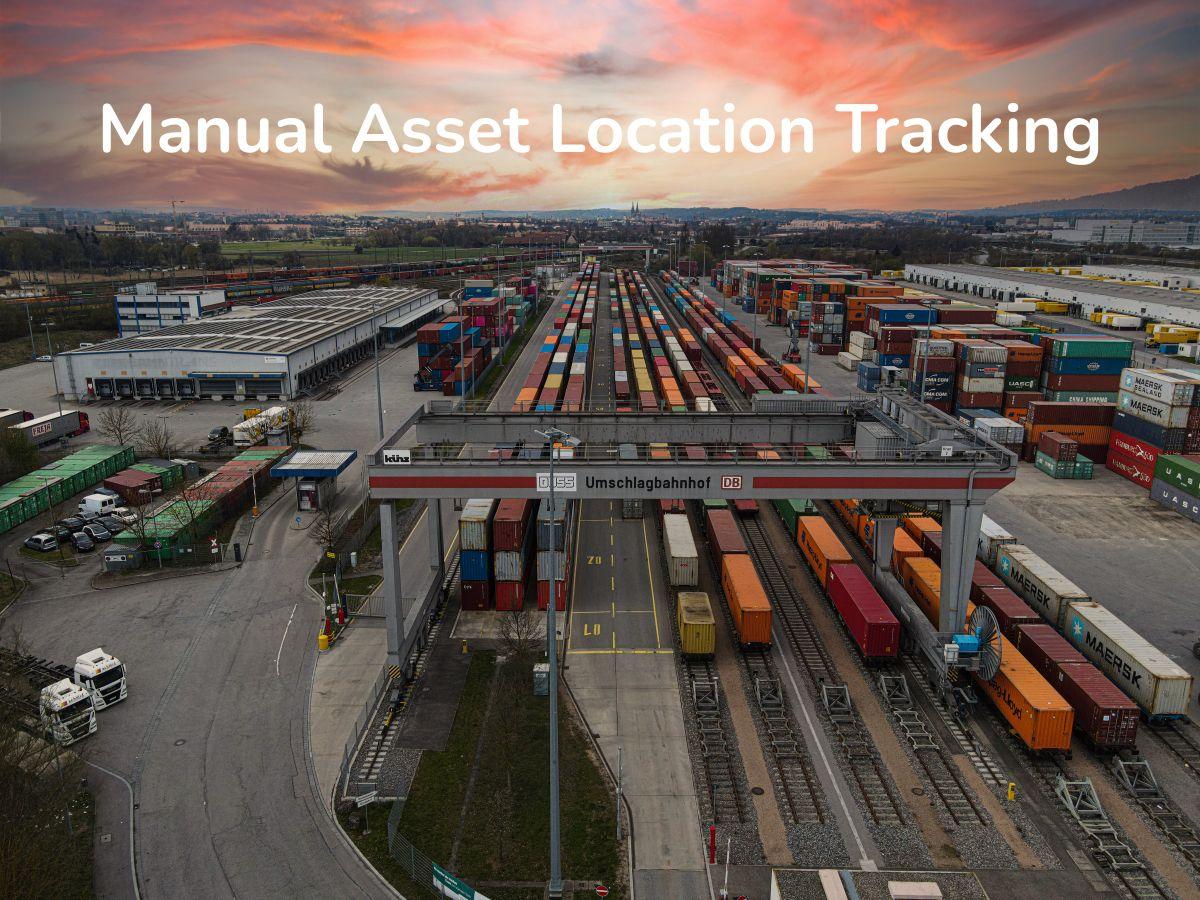
Manual asset location tracking may sound old-school, but for small businesses, it's often the most effective approach. Especially when GPS tools are too costly, unreliable in low-signal areas, or simply overkill for the job. Surveys show that over 30% of SMBs don't track their assets at all.
This is likely because they either lack sufficient resources for tools or are unfamiliar with manual asset tracking. The best move here is to start tracking manually, which represents a significant improvement from not tracking at all.
Let’s break down how manual asset location tracking works, why it’s practical for SMBs, and how you can get started with minimal investment.
Key Takeaways
- What It Is: Manual asset location tracking involves recording asset movements without the use of GPS. It uses checklists, spreadsheets, or logs, making it ideal for low-tech, low-budget environments.
- Why It Works for SMBs: For small teams, manual tracking is affordable, flexible, and easy to customize. It works well in offline areas, builds accountability, and avoids the complexity of expensive automated systems.
- How to Apply It Daily: From job site check-ins to warehouse tool logs, manual tracking fits naturally into daily workflows. Whether via paper, spreadsheets, or simple messages, it helps prevent asset loss and delays.
- When to Upgrade: Manual systems have limits. As your business grows, switching to a platform like Itefy helps automate tracking, improve accuracy, and save hours every week.
What is Manual Asset Location Tracking?
Manual asset location tracking is the process of recording the location of assets, personnel, or equipment without the use of GPS. It's a simple system where updates are made manually through logs, forms, or messages.
Instead of relying on automated technology, manual tracking relies on human input. A team member might check in by phone, mark a delivery on a paper log, or complete a brief form in a spreadsheet.
This approach is especially useful in low-signal environments, such as construction sites, rural delivery routes, or warehouses with poor connectivity. It's also ideal for small teams that don't need complex software and want more control over their operations.
Benefits of Manual Asset Location Tracking for SMBs
Manual tracking might seem basic, but for many small and mid-sized businesses, it's the most practical and efficient way. It is beneficial when tech-heavy systems create more problems than they solve.
Here are the benefits of manually tracking your assets’ location:
1. Affordability
Most GPS or automated tracking systems come with high upfront costs, monthly fees, and integration headaches.
For SMBs running on lean budgets, those costs add up fast. Manual tracking eliminates those expenses. All you need is a checklist, a spreadsheet, or a simple form.
2. Flexibility in Any Environment
Manual tracking doesn't depend on mobile data, Wi-Fi, or even electricity. Whether your team is operating from a warehouse, on a remote job site, or delivering in rural areas, it still works. This makes it ideal for industries like logistics, construction, and agriculture, where reliable connectivity isn’t always guaranteed.
3. Accountability and Ownership
When employees log data manually, they take more responsibility for their actions. It's no longer about blaming faulty systems; each check-in or entry reflects real human involvement. This accountability builds a culture of trust and accuracy.
4. Simplicity and Speed
Manual systems require no training, IT support, or complicated interfaces. A five-minute walkthrough is often enough to get your team onboard. This simplicity reduces delays and resistance from staff, especially those who aren't tech-savvy.
5. Customizable for Your Needs
When you track assets manually, you can modify the workflow as needed. You decide what's logged, when, and how. From tool checkouts to delivery stops, you control the format, either paper or digital.
Why do SMBs Lose Track of Assets in the First Place?
Most asset loss in small and mid-sized businesses comes down to one issue: a lack of reliable systems. Many teams still rely on memory, verbal updates, or informal habits that leave too much room for error. A worker might take a tool off-site and forget to log in.
A delivery driver might skip a stop, and no one knows until a customer complains. Without clear records, tracking becomes guesswork. Only 6% of companies report having full visibility of their supply chain and how it’s working. This is actually concerning.
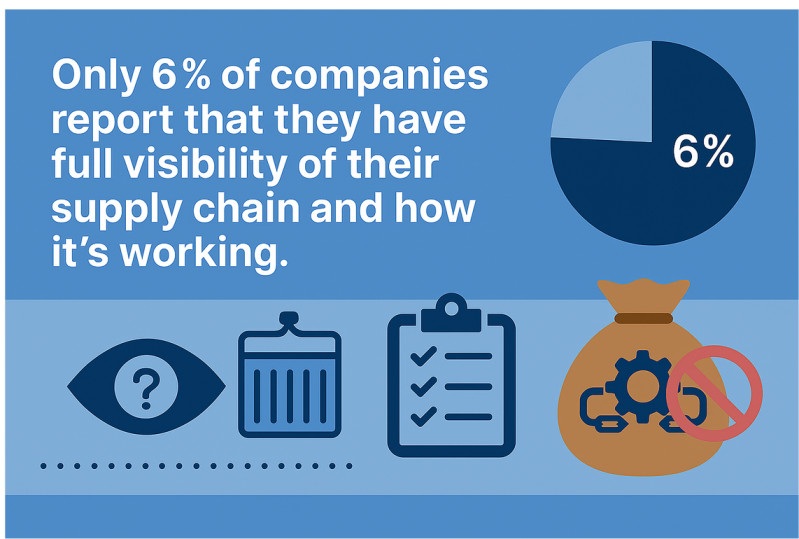
Another reason is an overreliance on technology that doesn’t always fit. GPS systems and auto-tracking software sound great. But, they often require stable connectivity, regular maintenance scheduling, and a team trained to use them.
Lastly, lack of accountability plays a big role. If no one is directly responsible for tracking, then everyone assumes someone else is doing it.
How SMBs Can Apply Manual Asset Location Tracking Daily
Manual location tracking integrates seamlessly into daily operations, more smoothly than most people think. For small and mid-sized businesses that lack the resources or need for automated systems, it offers a hands-on approach to maintaining accountability.
Here's how it can be applied in real-world scenarios across different industries:
1. Field Service Teams
Electricians, plumbers, pest control workers, and maintenance crews often move between job sites. Instead of relying on GPS check-ins, teams can simply call in, text their location, or update a shared log after each visit.
A quick message, such as "Arrived at Site A – 10:05 AM," provides enough detail to track job flow and time spent on-site. It keeps managers in the loop without requiring expensive apps or spotty GPS signals.
2. Retail or Warehousing
SMBs managing tools, handheld devices, or inventory in retail or warehouse settings can use manual check-in/check-out sheets to avoid loss and disorganization. Each item is logged with a date, time, and employee name when it is borrowed or returned.
3. Logistics and Delivery
Delivery drivers often operate in rural areas where GPS signals are weak or unreliable. Manual notes at each stop, written or messaged, can log time, customer confirmation, and any delivery issues. Not only does this provide a record for disputes, but it also helps businesses identify delays or routing inefficiencies.
4. Construction and Contracting
On fast-paced job sites, equipment like drills, ladders, or generators is shared between teams. Without a system, tools disappear. Manual equipment maintenance logs, maintained at the site entrance or with team leads, track who took what and when.
Tools That Make Manual Tracking Easier
Understanding how manual asset location tracking works is just the start; knowing which tools to use makes all the difference. Let’s look at a few simple tools that make manual tracking faster, more organized, and easier for your whole team to use.
1. Digital Spreadsheets
Google Sheets and Excel templates are among the easiest tools to start with. You can set up shared logs where team members manually enter time, location, and notes. The majority of businesses still rely on spreadsheets as compared to CMMS for operational tracking.
The best way to utilize these sheets is by using filters, color-coding, and simple formulas to keep records clear and searchable.
2. Paper Logs
For businesses with offline environments or limited digital access, paper-based tracking remains effective. Use clipboards, daily sheets, or wall-mounted boards to log location updates, tool check-outs, or delivery confirmations.
These are ideal for warehouses, construction sites, or mobile teams with no consistent internet access.
3. Team Communication Tools
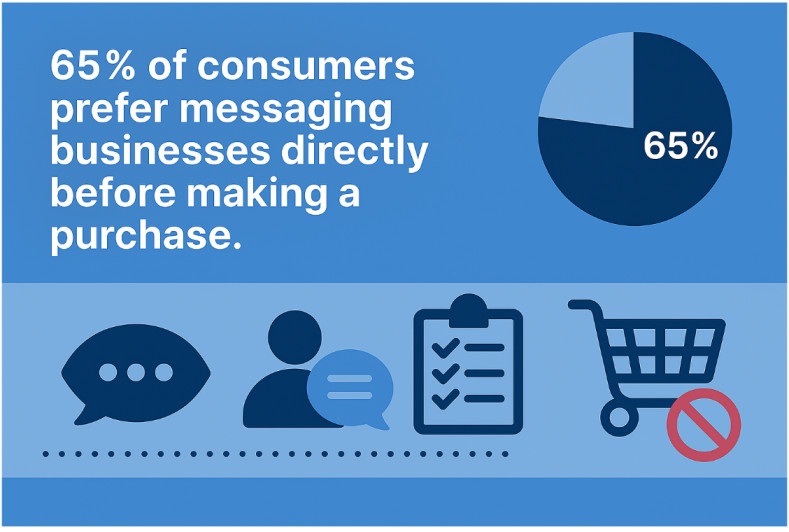
WhatsApp, Slack, or SMS can double as tracking tools. A quick message, such as "Delivered to client two at 3:30 PM," creates a real-time log. Interestingly, 65% of consumers prefer to message businesses directly rather than email them. This is where WhatsApp becomes invaluable.
Common Mistakes to Avoid and How
While manual tracking is simple, it's easy to get it wrong if not managed well. The common mistakes SMBs make include:
1. Not Assigning Accountability
When no one is clearly responsible for tracking, everyone assumes someone else is doing it. This leads to missing updates and confusion. Ensure that specific individuals are assigned per shift, location, or task to handle tracking. Additionally, include it in the employees' daily checklist to prevent it from being forgotten.
2. Overcomplicating the System
Trying to track too many details or using complex templates can overwhelm your team. If the system takes more time than the task, people will avoid it. So, keep it simple and track only what's essential. This includes time, place, item, and person responsible.
3. Forgetting to Review Logs
Logs that are filled out but never checked become useless. Reviewing helps you spot trends, missing entries, or recurring issues. Set a weekly or bi-weekly review process. Even a quick 10-minute scan can reveal valuable insights.
4. Failing to Train the Team Properly
Assuming everyone knows how to use the system often leads to inconsistent entries. Small mistakes pile up fast. You must train your team clearly, even if the process feels obvious. Use visual guides or simple videos to show exactly how and when to log updates.
How Far Can Manual Tracking Really Take You?
Manual location tracking can be incredibly effective for small and mid-sized businesses, especially in the early stages. With a limited number of assets and a tight budget, using checklists, spreadsheets, or logbooks gives teams a practical and low-cost way to stay organized.
It builds a habit of accountability and helps employees stay aware of where tools, equipment, or deliveries are at any given moment.
But as the workload grows, so does the strain on your team. More jobs mean more movement, more assets, and more room for things to fall through the cracks. That’s when manual tracking starts to slow you down.
At this point, a tool like Itefy becomes a wise investment. It automates location tracking, sends reminders, and stores everything in one place, so no one has to manage it manually. Your team can focus on what they do best, while Itefy handles the tracking in the background.
Take Control of Your Assets Before It Costs You
Manual asset location tracking provides a simple and effective way to keep your operations visible, organized, and productive.
When you're ready to level up from spreadsheets and checklists, Itefy is the smart next step.
With Itefy, you can track asset locations, maintenance, checkouts, and reservations, all from one easy-to-use dashboard. It's a cloud-based equipment management platform built for real-world businesses that need clarity and control, not complexity.
Start your 14-day free trial with Itefy today.
Frequently Asked Questions
-
No. You can begin with a paper logbook, whiteboard, or free spreadsheet. If you want to go digital, tools like Google Sheets, WhatsApp, or basic check-in apps can support manual entry. You can also switch to Itefy, as it's one of the most affordable and easy-to-use asset tracking software options.
-
Human error is always a possibility, especially when tracking is rushed, unclear, or inconsistent. However, using simple formats and assigning clear responsibilities can significantly improve accuracy. Many SMBs find that when team members know their entries are visible and reviewed, they naturally become more careful and consistent.
-
It depends on your business size and environment. Manual tracking offers more control, especially in low-signal areas or when your team prefers a simple workflow. For SMBs, it's often more cost-effective and easier to implement than GPS systems, which can be overkill for smaller operations.
-
Yes, when done consistently and with a simple system in place, manual tracking is highly reliable. It avoids common GPS issues, such as signal loss and app crashes. By assigning responsibility and using tools, small teams can maintain accuracy across daily workflows.