Create an Equipment Inventory Database : A Step by Step Guide
Keeping track of equipment inventory can be tedious and hard if you don't know where to begin. We're created a step by step guide on how to create an equipment inventory list that will help you gain full control of your equipment.
In this article:
- What's information should an equipment inventory list contain?
- Optional information to add to an equipment inventory list
- What kind of assets can be added to an equipment inventory list?
- Spreadsheet, dedicated equipment management system or text document - what to choose?
- Okay, let's dive in
- How to separate multiple equal items from each other?
- Keeping track of where your equipment is
- How to find out if the equipment is available
- How to keep track of equipment condition
- Is there a free spreadsheet template I can use to get started?
- Can I begin with a spreadsheet solution, but advance to a dedicated equipment inventory management system later?
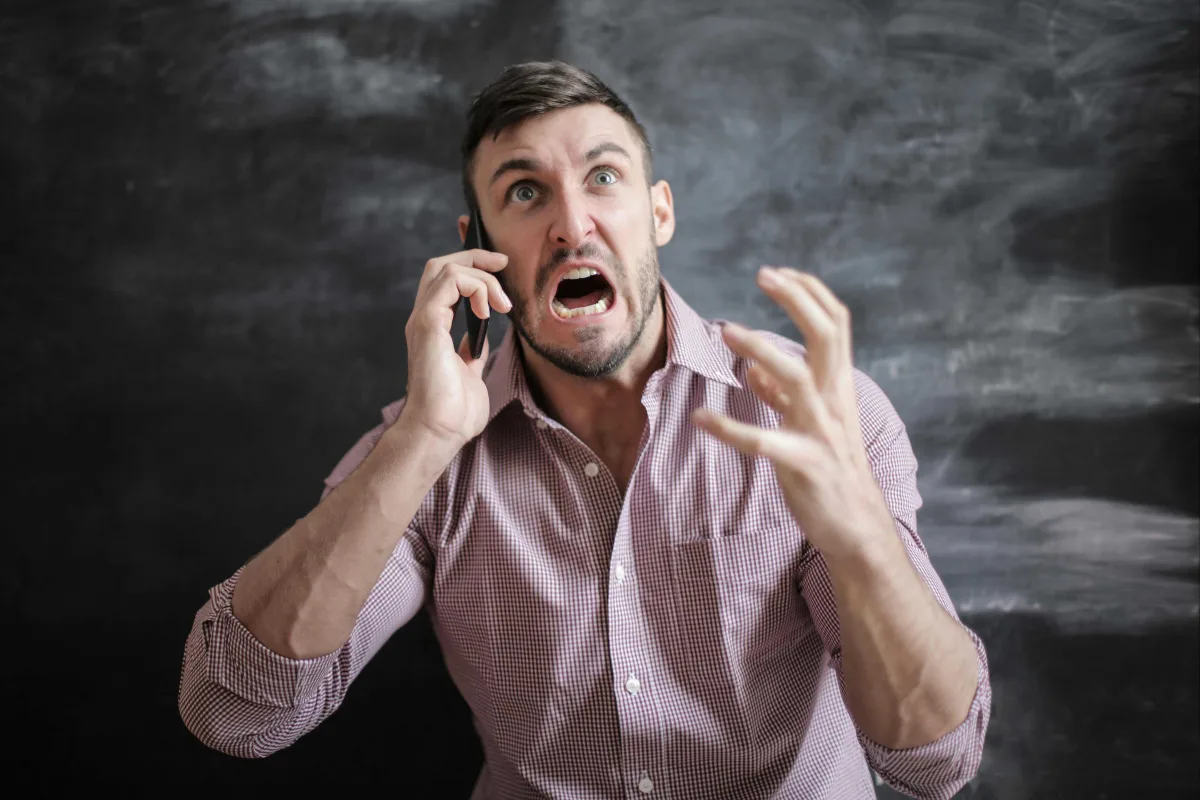
You probably know the feeling; You're in urgent need of this particular piece of equipment you know your business owns, but it is not located where it is supposed to.
You start calling around to figure out if one of your co-workers know where it is, and perhaps you are in luck because someone knows where it is. Or you might as well end up where you started, without that crucial asset you need to do your job.
Keeping track of all the equipment inventory your business owns can be challenging without some kind of list is challenging, and it doesn't take long before you loose track of what you have, who is currently in charge of it, where it is etc.
Just think about the equipment each of your employees uses, like laptops and cellphones. If you don't have some kind of list of the equipment with information on usage, you will most likely loose track of it, and end up spending money buying redundant equipment.
What's information should an equipment inventory list contain?
An equipment inventory list should contain essential information to accurately identify, track, and manage each piece of equipment.
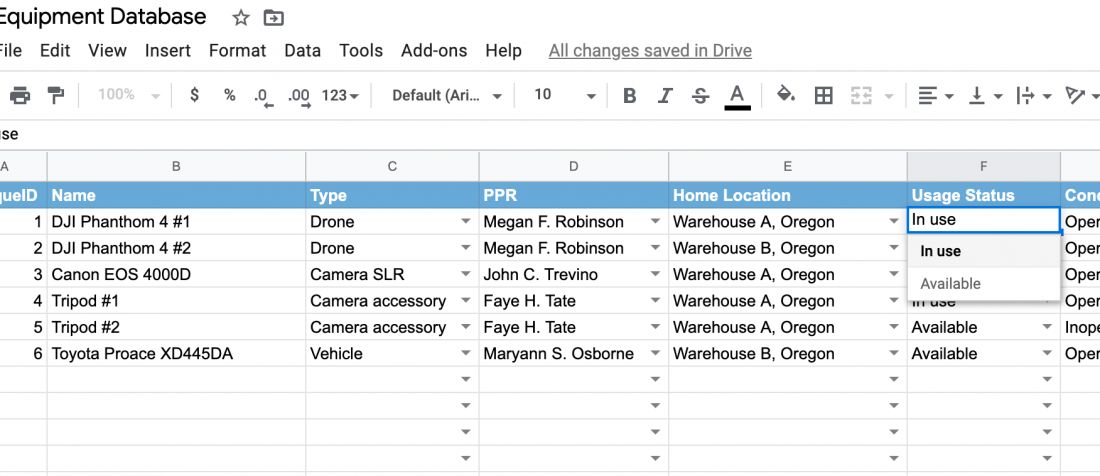
While the specific details may vary depending on the organization's needs and industry, the following are commonly included in an equipment inventory:
Item Name/Description: A clear and concise description or name of the equipment to easily identify it.
Serial Number/Asset Tag: A unique identifier assigned to each piece of equipment for tracking purposes. This could be a serial number provided by the manufacturer or an asset tag generated by the organization.
Acquisition Date: The date when the equipment was acquired or put into service.
Location: The physical location where the equipment is currently located, whether it's a specific room, department, or facility.
Owner/Department: The department or individual responsible for the equipment, aiding in accountability and maintenance management.
Purchase Cost/Value: The initial cost or current market value of the equipment for financial tracking and reporting purposes.
Warranty Information: Details of any warranties or service agreements associated with the equipment, including expiration dates and coverage terms.
Maintenance History: A record of maintenance activities performed on the equipment, including dates, types of maintenance, and any issues encountered.
Usage History: Information on how often the equipment is used and for what purposes, helping to assess its productivity and lifespan.
Depreciation: The depreciation schedule or method used to calculate the decrease in value over time, important for financial reporting and asset valuation.
Supplier/Vendor Information: Contact details of the supplier or vendor from whom the equipment was purchased, facilitating communication for repairs, replacements, or additional purchases.
User Manuals/Documentation: Accessible links or attachments to user manuals, technical specifications, and other relevant documentation for reference and troubleshooting.
Responsible Personnel: Names or roles of individuals responsible for maintaining, servicing, or using the equipment, ensuring clear accountability.
Status: The current operational status of the equipment (e.g., in use, under repair, decommissioned), providing visibility into its availability and condition.
Notes/Comments: Additional comments or notes relevant to the equipment, such as special requirements, known issues, or future upgrade plans.
Optional information to add to an equipment inventory list
Depending on the specific needs and goals of the organization, there are several optional pieces of information that can be added to an equipment inventory list:
Usage Metrics: Detailed usage metrics such as hours of operation, cycles completed, or mileage for equipment like vehicles or machinery. This information can help in assessing equipment performance, predicting maintenance needs, and optimizing usage.
Calibration Records: For equipment requiring calibration, recording calibration dates, results, and next calibration due dates ensures compliance with quality standards and regulatory requirements.
Certifications and Compliance: Documentation of certifications, compliance with industry standards, and regulatory requirements specific to the equipment, demonstrating adherence to safety and quality protocols.
Lease/Rental Agreements: Details of lease or rental agreements for equipment acquired through leasing or rental arrangements, including contract terms, expiration dates, and leasing company contacts.
Insurance Information: Information related to equipment insurance coverage, including policy numbers, coverage limits, and contact information for the insurance provider.
Disposal/End-of-Life Plans: Plans for equipment disposal or end-of-life management, including methods of disposal, recycling, or resale, and associated costs or procedures.
Energy Consumption: Tracking energy consumption data for equipment to identify opportunities for energy efficiency improvements and cost savings.
Integration with Maintenance Management Systems: Integrating equipment inventory with maintenance management systems to automate work order generation, track maintenance schedules, and monitor repair history.
Asset Condition: Detailed descriptions of the equipment's condition, including any wear and tear, damage, or defects observed during inspections.
Supplier Performance: Evaluation of supplier performance, including feedback on product quality, delivery times, and customer service, to inform future purchasing decisions.
Training Requirements: Identification of training requirements for operating or maintaining specific equipment, ensuring personnel are adequately trained and certified.
Emergency Procedures: Emergency procedures or protocols related to the equipment, such as shutdown procedures, emergency contacts, and evacuation plans, to ensure safety in case of emergencies.
Including these optional pieces of information in the equipment inventory list can provide a more comprehensive view of asset management, enhance decision-making processes, and improve overall operational efficiency.
What kind of assets can be added to an equipment inventory list?
In addition to physical equipment, various types of assets can be added to an equipment inventory list to comprehensively manage resources and facilitate efficient operations. These assets may include:
Tangible Assets:
Furniture: Office furniture such as desks, chairs, cabinets, and workstations.
Fixtures: Built-in fixtures and fittings within a facility, such as lighting fixtures, shelving, and partitions.
Tools and Instruments: Hand tools, power tools, measuring instruments, and specialized equipment used for specific tasks or projects.
Vehicles: Company vehicles, including cars, trucks, vans, and forklifts, along with vehicle-related equipment like GPS devices or vehicle tracking systems.
Machinery: Industrial machinery, equipment, and tools used in manufacturing, production, or construction processes.
IT Equipment: Computers, laptops, servers, printers, scanners, routers, switches, and other hardware devices used for information technology purposes.
Medical Equipment: Medical devices, diagnostic equipment, and healthcare technology used in clinical settings.
Intangible Assets:
Software Licenses: Licenses for software applications, operating systems, databases, and other digital tools used for business operations.
Intellectual Property: Intellectual property assets such as patents, trademarks, copyrights, and trade secrets that contribute to the organization's value and competitiveness.
Digital Assets: Digital content, media files, databases, website assets, and other digital resources used for marketing, branding, or information management.
Contracts and Agreements: Legal contracts, agreements, and licenses related to business partnerships, vendor relationships, and client engagements.
Infrastructure Assets:
Facilities: Buildings, structures, offices, warehouses, and other physical facilities owned or leased by the organization.
Land: Owned or leased land parcels used for business operations, real estate development, or investment purposes.
Utilities: Infrastructure assets such as power distribution systems, water supply systems, telecommunications networks, and transportation infrastructure.
Financial Assets:
Investments: Stocks, bonds, mutual funds, and other investment instruments held by the organization for financial growth or liquidity.
Cash and Cash Equivalents: Cash reserves, bank deposits, short-term investments, and liquid assets available for immediate use or investment.
Human Capital Assets:
Employee Skills and Expertise: Skills, qualifications, certifications, and training records of employees, highlighting their contributions to organizational capabilities and performance.
By including these diverse types of assets in the equipment inventory list, organizations can effectively track, manage, and optimize their resources to support strategic goals, and ensure compliance.
Spreadsheet, dedicated equipment management system or text document - what to choose?
Choosing between a spreadsheet, dedicated equipment management system, or text document depends on the specific needs, resources, and objectives of your organization. Here's a comparison to help you make an informed decision:
1. Spreadsheet:
Pros:
Cost-Effective: Spreadsheets like Excel or Google Sheets are often readily available and cost-effective solutions for small businesses with limited budgets.
Flexibility: Spreadsheets offer flexibility in terms of customization, allowing users to design their own formats, columns, and formulas to suit their needs.
Familiarity: Many employees are already familiar with spreadsheet software, requiring minimal training for adoption.
Accessibility: Cloud-based spreadsheets facilitate real-time collaboration and accessibility from multiple devices and locations.
Cons:
Limited Functionality: Spreadsheets may lack advanced features for comprehensive equipment management, such as automated notifications, barcode scanning, or integration with other systems.
Data Integrity: Version control issues and human errors can compromise data integrity, leading to inaccuracies and inefficiencies.
Scalability: As the organization grows and the volume of data increases, spreadsheets may become cumbersome to manage and prone to performance issues.
2. Dedicated Equipment Management System:
Pros:
Comprehensive Functionality: Dedicated equipment management systems offer specialized features tailored for managing equipment inventories, maintenance schedules, service history, and compliance requirements.
Automation: These systems often automate repetitive tasks such as maintenance scheduling, notifications, and reporting, saving time and reducing manual errors.
Scalability: Designed to handle large volumes of data, dedicated systems can scale with the organization's growth and evolving needs.
Data Security: Centralized databases with robust security measures ensure data confidentiality, integrity, and availability, reducing the risk of unauthorized access or data loss.
Cons:
Cost: Dedicated systems may involve upfront costs for software licenses, implementation, and training, making them less accessible for small businesses with limited budgets.
Learning Curve: Users may require training to familiarize themselves with the system's features and functionality, potentially impacting adoption and productivity initially.
Customization Limitations: While many systems offer configurable options, customization may be limited compared to spreadsheets, restricting adaptability to unique workflows or requirements.
3. Text Document:
Pros:
Simplicity: Text documents like Word or Notepad provide a straightforward way to record equipment information without the complexity of spreadsheet formulas or dedicated software.
Accessibility: Text documents are universally compatible and easily accessible on various devices without the need for specialized software.
Low Barrier to Entry: Minimal setup or technical expertise is required to create and maintain text documents, making them accessible to users with basic computer skills.
Cons:
Limited Functionality: Text documents lack the structured format and functionality of spreadsheets or dedicated systems, limiting their utility for organizing and analyzing data.
Data Management Challenges: Managing large volumes of data in a text document can be challenging, leading to issues with organization, searchability, and data retrieval.
Collaboration Constraints: Text documents are not designed for real-time collaboration or concurrent editing, making it difficult for multiple users to update or access information simultaneously.
Ultimately, the choice between a spreadsheet, dedicated equipment management system, or text document depends on factors such as budget, complexity of equipment management needs, scalability requirements, and user preferences.
Small businesses with simple inventory tracking needs and limited resources may start with a spreadsheet or text document, while organizations with more complex requirements and growth aspirations may benefit from investing in a dedicated equipment management system for enhanced functionality and scalability.
Okay, let's dive in
If you're using a spreadsheet, each unique equipment item should use one row or line in the spreadsheet. You can add as much or little information as you want, but the least information to begin with should be:
- Item name, e.g. Apple iPhone 15 Pro
- Unique ID, e.g. the license plate number (for vehicles), serial number, or a custom numbering
How to separate multiple equal items from each other?
Many businesses standardize by using for example the same kind of laptops or smartphones, however, this may cause some challenges in separating each equipment item from each other. While some assets, like vehicles is easy to distinguish by the license plate ID, most other assets like laptops, cellphones, cameras, tools etc. do not have a unique and easy to spot identifier.
The easiest way is simply to label each item by separate numbers. Each item should have a unique number, not only within the same category but for all kind of assets, so that one camera and one laptop doesn't end up having the same number.
Dedicated equipment management systems usually have a QR code based system where you just scan a QR code label off of the equipment with a mobile app, in order to easily and quickly identify it.
Keeping track of where your equipment is
It's (almost) no use in knowing what equipment you have, if you don't know where it is. For this you should add 2 columns or pieces of information in your equipment list:
- Current location
- Home location
While the current location is where each equipment item is at the moment, the home location information is useful when someone is finish using the item. By knowing the home location of an item, everyone will know where to place the item after it has been used.
Also, unless the items are stationary, if the current location and home location is the same, if would most likely mean that the equipment is available. However, we'll come back to a better method for this during the next steps.
Most dedicated equipment inventory management systems will handle this by default, making it easy to both find out where all your equipment is, but also to see what equipment items that are located in each location.
How to find out if the equipment is available
In most dedicated asset management systems, users will be able to reserve, check out and check in equipment. These features will automatically keep track of the availability of each equipment item, who is or has been using it, and the plans for future usage.
You can make this work in a spreadsheet as well, however probably not as smooth as in a dedicated software, but it's better than not keeping track of this at all.
For this, you will need a few more columns:
- Availability
This should be a dropdown with the following options:- Available
- In use
- Unknown
- Used by
It's possible to have a dropdown that has a reference to another sheet, where you can add staff so that it's easy to simply select the person currently using the item, if in use. Otherwise, you can you enter the name of that person. - Checkout date
The date of when the equipment has ben checked out. Change the column to date fields. - indefinitely
The date of when the equipment is suppose to be returned. Change the column to date fields.
If you want to add the ability to plan the next time of usage, you may also add:
- Next reservation
Short description of the next reservation - Reserved by
The person who is in charge of the reservation. This may be configured the same way as the "Used by" column for simplicity. - Reservation start
The date of when the reservation is supposed to start. Set the column type to date. - Reservation end
The date of when the reservation is supposed to end. Set the column type to date.
The way this will work is that when a reservation is about to begin, you should basically move the reservation information over to the checkout information fields.
Although the spreadsheet system is easy to get started with, it has a few downsides compared to a dedicated equipment inventory management system:
- You can only add the next upcoming reservation for each asset in a spreadsheet (unless you add more columns for more reservations). In a dedicated system, each item will have its own calendar where you can plan ahead indefinitely.
- You will be able to reserve and check out multiple items in one go with a dedicated system, however, it's a bit more work using a spreadsheet system.
- Out of the box you will not be able to keep track of the usage and reservation history, which is kept automatically by default in almost any equipment inventory management system.
- An equipment inventory management system will be able to notify the person in charge of each equipment item if a checkin is overdue.
How to keep track of equipment condition
There is no point having equipment easily available if it's not operational. Also, keeping damaged equipment idle without fixing it is also not great.
However, many times it's not possible to get equipment fixed right away, so keeping track of the condition of each equipment item in addition to a way of getting it fixed is crucial.
Let's add a few more columns that are useful for this:
- Condition
Make it a dropdown with the following options:- Operative
- Inoperative
- Discarded
- Primary Person Responsible
The main person who is in charge of the asset. This may be configured the same way as the "Used by" column for simplicity. - Condition change date
The date of when the condition was changed. Set the column type to date. - Est. repair date
If the condition is inoperative, this is the estimated date of when the asset should be fully operational. Set the column type to date.
The condition field has an option called discarded. This is for equipment that is beyond repair, but not yet gotten rid of. Every time the list is reviewed and items with this condition is found, the people in charge will have to decide what to do with this item.
A dedicated equipment inventory management system will have some additional advantages you may benefit from:
- The condition history is being kept for each item. This is useful both for knowing the history and performance of each equipment item, but it can also help in resolving issues if there is a recurring problem with certain equipment.
- The person responsible for each item will get notified if there is an issue with an item, and will be able to take action to resolve the problem more quickly.
- It's easier to get a full overview of the current state of all your equipment assets and the over-all condition.
Is there a free spreadsheet template I can use to get started?
Yes, we have created a spreadsheet template for both Google Sheet and Microsoft Excel that is available for download a the end of this other blog article.
Can I begin with a spreadsheet solution, but advance to a dedicated equipment inventory management system later?
Yes, it's not problem to begin with a spreadsheet, and you can easily import all your equipment items into a dedicated equipment inventory management system such as Itefy, within just a few minutes. However, you may loose some information. On the other hand, you will be able to enrich your equipment item records easily with more information quite quickly.