How to Calculate Total Manufacturing Cost: A Simple Guide
Are you thinking about how to calculate total manufacturing cost? Here’s a detailed guide about everything you need to know about TMC and its importance.
In this article:
- What Is Total Manufacturing Cost
- The Importance of Total Manufacturing Cost
- 1. Accurate Pricing Strategy
- 2. Budgeting & Financial Planning
- 3. Cost Control and Efficiency
- 4. Inventory Valuation
- How to Calculate Total Manufacturing Cost
- 1. Gather Cost Data
- 2. Calculate Direct Material Costs
- 3. Calculate Direct Labor Cost
- 4. Calculate Manufacturing Overhead
- 5. Use the Total Manufacturing Cost Formula
- Comparing Total Manufacturing Cost, COGM, and COGS
- 1. Total Manufacturing Cost (TMC)
- 2. Cost of Goods Manufactured (COGM)
- 3. Cost of Goods Sold (COGS)
- Conclusion
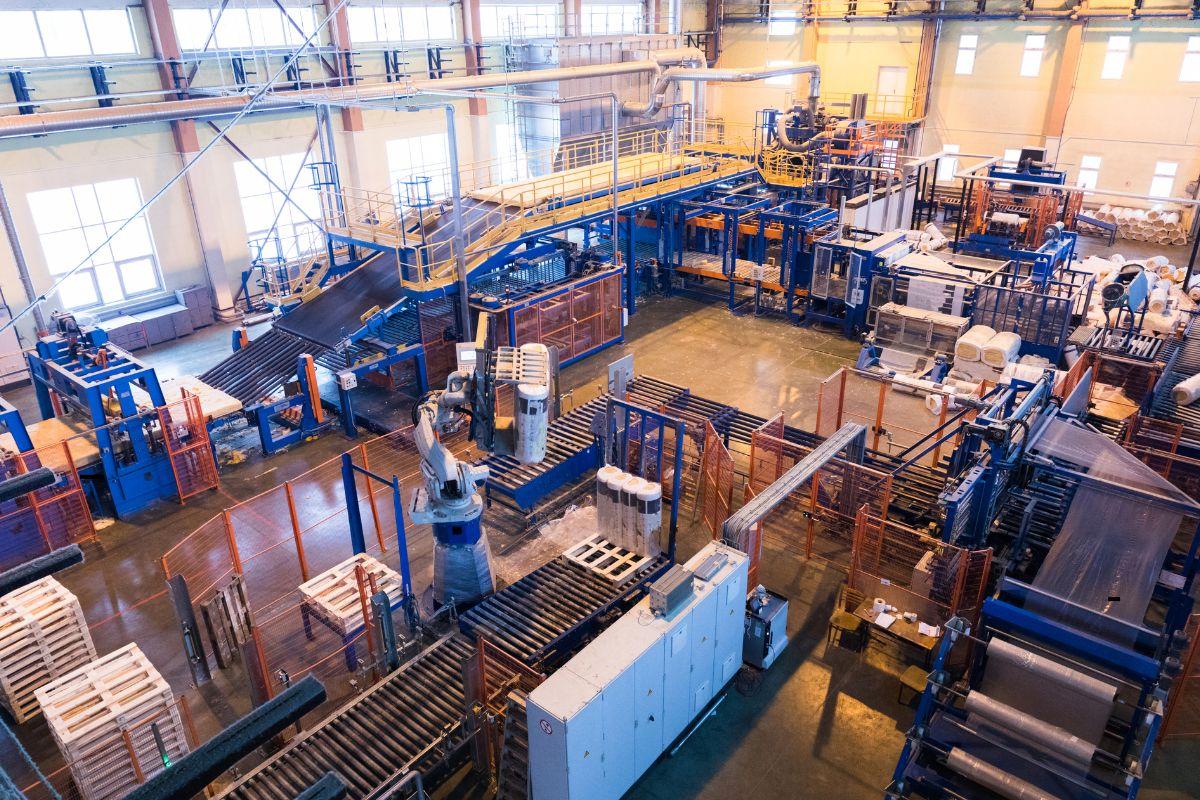
A successful production line takes three things: quality materials, skilled labor, and, most importantly, calculated manufacturing costs. Without a clear idea of costs, pricing can turn into a guessing game. This may lead to underpricing, which absorbs profits, or overpricing, which repels customers away — both of which harm your company's bottom line.
Having a clear idea of the total manufacturing costs (TMCs) helps avoid these instances, leading to better budgeting and financial planning. Defined as the sum of all expenses incurred during production, this metric enables you to spot areas for cost-cutting and efficiency improvements. But how to calculate total manufacturing cost?
What Is Total Manufacturing Cost
Total Manufacturing Cost (TMC) is the sum of all expenses incurred by a company to produce a finished product. In other words, it represents the total resources consumed to bring an item from raw materials to a market-ready state. This financial metric includes three different cost groups: direct material, direct labor, and manufacturing overheads.
Besides being a figure on the balance sheet, total manufacturing cost gives valuable insights into the efficiency of your production processes. This information, then, helps companies identify areas where a few dollars can be saved, or operations can be streamlined. It also ensures that products are priced competitively while still allowing for a healthy profit margin.
Does the TMC show that labor costs are unusually high? Shift to automation tools to cut down on these expenses. Are material costs rising disproportionately? Look into alternative suppliers or negotiate better terms. This kind of actionable feedback helps companies make informed decisions, leading to a happier, more favorable bottom line.
The Importance of Total Manufacturing Cost
Understanding the total manufacturing cost (TMC) is essential for any business with production-based operations. This financial metric gives businesses a detailed picture of their production expenses, leading to more informed decision-making and better financial management. Here’s why the total manufacturing cost is so important.
1. Accurate Pricing Strategy
One of the primary reasons for understanding TMC is to set appropriate prices for your products. When you have a clear understanding of the production costs, you're likelier to set a price that covers all expenses while providing enough profit margins. This helps your company stay competitive in the market by hitting the sweet spot between overpricing and underpricing.
2. Budgeting & Financial Planning
Usually, the second biggest expense for businesses is inventory (coming only after labor), which accounts for 25% to 35% of a company’s budget. Having a clear idea of the total manufacturing cost helps you manage these expenses wisely through budgeting and financial planning.
By understanding the complete cost structure, companies can allocate resources better, predict future expenses, and set realistic financial goals. This helps in creating detailed budgets that cover all aspects of production, thereby avoiding “surprise” costs and ensuring financial stability.
3. Cost Control and Efficiency
When companies regularly track the total manufacturing cost, they get a better idea of areas to save expenses and eliminate wasteful spending. For example, if the figure is higher than expected, there may be inefficiencies in the production process. These may include excessive waste, high labor costs, or outdated machinery, among others.
Likewise, if you see a high direct materials cost, its better to negotiate better terms with suppliers, like wholesale prices or purchasing in bulk. In case manufacturing overheads exceed the normal range, analyze the “why” behind the hike in expenses. Is it due to high utility bills or inefficient maintenance scheduling? Or is the factory space not utilized efficiently?
4. Inventory Valuation
Besides cost control and financial planning, TMC also helps companies with inventory valuation. It helps calculate the cost of goods manufactured (COGM) and, subsequently, the cost of goods sold (COGS). Accurate inventory management and valuation is a necessary component of financial reporting and helps companies comply with accounting standards.
The practice ensures that financial statements reflect the true value of inventory, which is necessary for both internal decision-making and external reporting to stakeholders. Here are some decisions well-maintained financials (with the true cost of inventory) help you make:
- Maintain optimal stock levels without overstocking or stockouts
- Competitive and profitable pricing strategies based on the true cost of goods
- Identify cost-saving areas like negotiating better terms with suppliers
- Helps in better cash flow management by reflecting the company’s financial position
- Informs decisions about whether to invest in more inventory or new product lines
How to Calculate Total Manufacturing Cost
If you run a production-based business, calculating total manufacturing cost is a fundamental part of your operations. It gives a clear idea of the expenses involved in producing goods, allowing for better financial planning and decision-making. Here’s a step-by-step guide to help you understand how to calculate total manufacturing costs.
1. Gather Cost Data
The first step for calculating total manufacturing cost is gathering cost data. This means collecting all relevant cost information that directly or indirectly contributes to the production of goods. After all, the accuracy of your TMC calculation depends on the precision of the data you gather. Incomplete or inaccurate financials may lead to a flawed cost analysis, affecting everything from profitability and budgeting to planning.
2. Calculate Direct Material Costs
Direct material costs are the expenses on raw materials that are directly traceable to the finished product. These are the physical components that become part of the final item. For example, the wood, textile, and timber used to create chairs and tables would be considered direct material in a furniture manufacturing unit.
Conversely, glue, sandpaper, or lubricants are indirect materials because they’re used across multiple products and do not become part of the finished good. As a result, these material expenses are accounted for in manufacturing overheads, not material costs. To calculate the direct material costs for a particular period, add the beginning inventory and purchases made during that interval. Then, subtract the ending inventory (or raw materials left at the end).
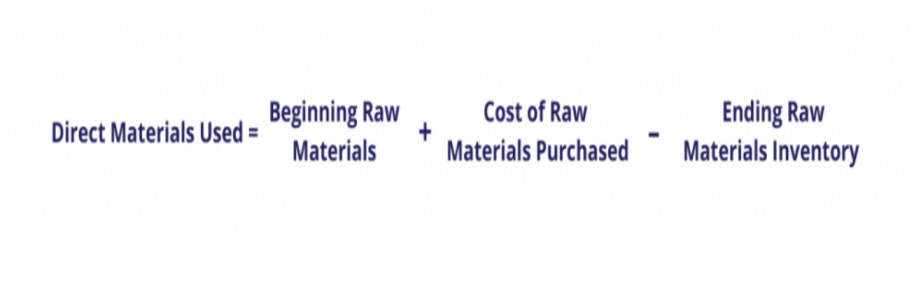
Calculating Direct Material Cost
Source: mtdmfg
3. Calculate Direct Labor Cost
The second part of the manufacturing cost equation is composed of direct labor costs. These costs are the wages paid to employees who are directly involved in the production of goods. In simple words, direct labor costs include all expenses related to the employees who physically convert raw materials into goods. This includes:
- Wages and Salaries: The basic pay for production workers.
- Overtime Pay: Additional wages for hours worked beyond the standard workweek.
- Bonuses and Incentives: Performance-based pay that is directly tied to production.
- Benefits: Health insurance, retirement contributions, holiday pay, sick leaves in cash.
To identify direct labor costs, you need to separate employees who play a direct role in the production line. These include machine operators, assemblers, quality control staff, and line workers. Team members not handling the production process — like supervisory staff, accountants, cleaning staff, and maintenance workers — are included in indirect labor.
Here’s the formula for calculating direct labor costs:
Direct Labor Cost = Total Hours Worked x Hourly Wage Rate
4. Calculate Manufacturing Overhead
If you want to calculate total manufacturing costs, the last thing you need is the manufacturing overheads. Also known as factory overhead or production overhead, this group includes all the indirect costs incurred during the production process. Here’s a list of things that are counted as manufacturing overheads in the manufacturing cost formula:
- Utilities: Electricity, water, and gas used in the production unit.
- Depreciation: The gradual reduction in the value of machinery and equipment.
- Maintenance and Repairs: Costs for keeping machinery and equipment in order.
- Factory Supplies: Items like lubricants, cleaning supplies, and small tools.
- Salaries of Indirect Labor: Wages for production managers, cleaners, and supervisors.
- Rent and Insurance: Costs of leasing and insuring the facility.
To calculate the manufacturing overheads, add all the indirect costs and allocate them to each product unit. The basis for allocation could be any relevant measure that reflects the activity level of production, like total labor hours, total machine hours, or sales. Here’s the formula for calculating manufacturing overheads.
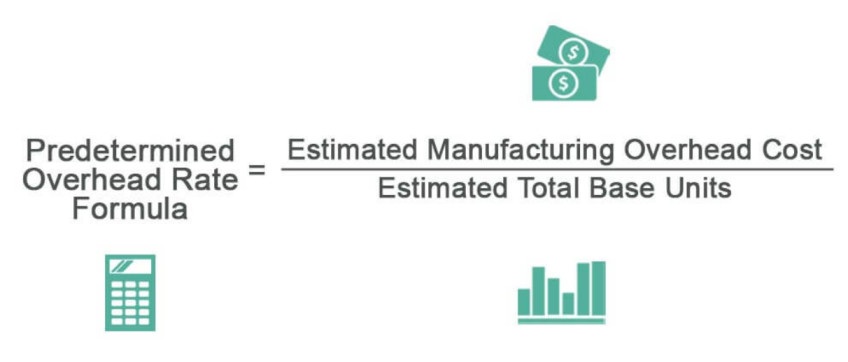
Predetermined Overhead Rate Formula
Source: WallStreetMojo
Note: Manufacturing overheads do not include expenses unrelated to the production process, like office rent, admin salaries, or marketing expenses. These are fixed costs of running a business and are accounted for separately.
5. Use the Total Manufacturing Cost Formula
Once you have calculated the direct labor, direct material, and manufacturing overhead costs, it’s time to sum these figures up. Here’s how to calculate total manufacturing cost using the formula:
Total Manufacturing Cost = Direct Material + Direct Labor + Manufacturing Overheads
Using the total manufacturing cost, you can calculate the profitability of your business by comparing it with your net revenue. The higher the production-related expenses, the narrower your profit margins are likely to be. By applying this formula to calculate your direct, indirect, and overhead costs, you can work out where the inefficiencies lie in your production process.
If the direct labor costs are high, analyze the efficiency of your employees and introduce training programs to help boost their skill set. Likewise, if the manufacturing overhead represents a major chunk of the TMC, check your utility usage, rent, and maintenance to identify areas for potential savings.
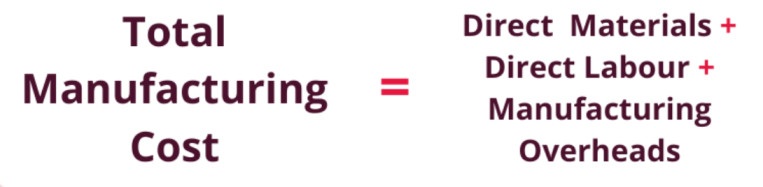
Formula for Total Manufacturing Cost
Source: Unleashed
Comparing Total Manufacturing Cost, COGM, and COGS
While total manufacturing cost is a valuable financial metric on its own, it also helps companies calculate other equally important KPIs. These include the Cost of Goods Manufactured (COGM) and Cost of Goods Sold (COGS), both of which reflect your company's bottom line. But what is the difference between these three metrics?
1. Total Manufacturing Cost (TMC)
The total manufacturing cost (TMC) shows the total production cost during a specific period, including all direct and indirect expenses. This metric does not consider whether the goods were completed by the end of the period or not, as it reflects the cumulative cost of production.
2. Cost of Goods Manufactured (COGM)
The Cost of Goods Manufactured (COGM) represents the total cost of goods that were finished and ready for sale during a specific period. This means that if you subtract the unfinished goods (or Work in Process) inventory from TMC, you’ll be left with the COGM. In other words, if all goods were finished at the end of the production period, COGM and TMC would be equal.
The formula for COGM includes the Total Manufacturing Cost plus the beginning inventory of goods still in production (work-in-process) minus the ending inventory of those same goods.
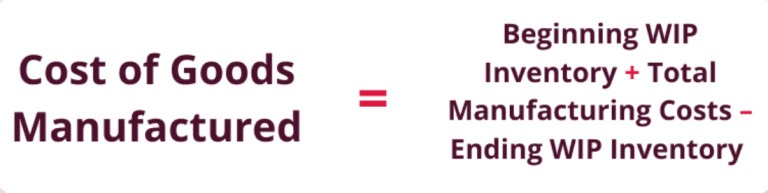
Formula for Calculating Cost of Goods Manufactured
Source: Unleashed
3. Cost of Goods Sold (COGS)
The Cost of Goods Sold (COGS) includes the cost of finished products that were actually sold during a given period. COGS is recorded on the income statement, where it is subtracted from revenue to calculate the gross profit. For manufacturers, COGS can only be calculated once you have the COGM.
If all the finished goods were also sold during a specific period, COGS would be equal to COGM. To calculate the Cost of Goods Sold (COGS), all you need to do is add the beginning inventory of finished goods into the purchased inventory or Cost of Goods Manufactured (COGM). Then, subtract the ending inventory of finished products from the result.
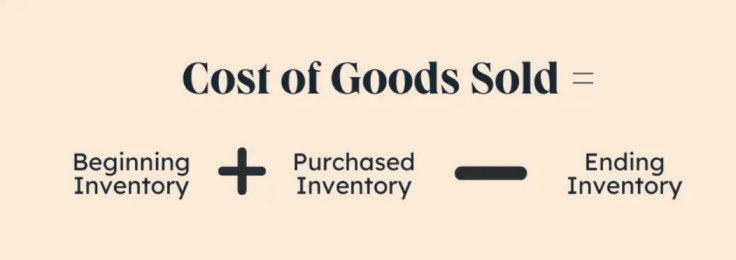
Formula for Calculating Costs of Goods Sold
Source: HubSpot
Conclusion
The total manufacturing cost (TMC) gives businesses a detailed view of their production expenses, guiding pricing and budgeting strategies. This financial metric also helps companies identify areas of overspending or underutilization, which aids in controlling costs and optimizing profit margins. However, managing manufacturing costs requires more than just knowledge.
You also need powerful tools to track and optimize resource utilization to boost your organization’s profit margins. This is where Itefy’s Manufacturing Equipment Management Software comes in. This one-stop solution keeps all your manufacturing assets and resources in one centralized, always up-to-date system.
With features like maintenance management, cloud equipment database, and location tracking, Itefy helps you gain full control over your manufacturing resources. It helps you manage your assets on the go, control your production costs, and optimize your overall production efficiency. So, try Itefy for free today and feel the difference in your operations!