Maintenance Scheduling: The Importance in Asset Management
Don’t let asset breakdowns halt your operations. This detailed guide explains how maintenance scheduling keeps your equipment in optimal form and saves you money.
In this article:
- Maintenance Schedule - An Overview
- Benefits of Maintenance Scheduling
- 1. Proactively Identifies Issues
- 2. Prevents Costly Repairs
- 3. Prevents Downtime
- 4. Increases Asset Lifespan
- 5. Enhances Workplace Safety
- 6. Better Budgeting
- 7. Improves Regulatory Compliance
- 8. Helps the Environment
- Signs That You Need Maintenance Scheduling
- 1. Increasing Breakdown and Repair Costs
- 2. Frequent Unplanned Downtime
- 3. More Aging Assets
- Scheduling Maintenance: The Best Practices
- 1. Highlight Assets that Need Maintenance
- 2. Analyze the Current and Previous Condition
- 3. List the Purpose of An Asset
- 4. Pick Your Maintenance Strategy
- 5. Monitor Asset Performance
- 6. Invest in the Right Team and Technology
- Conclusion
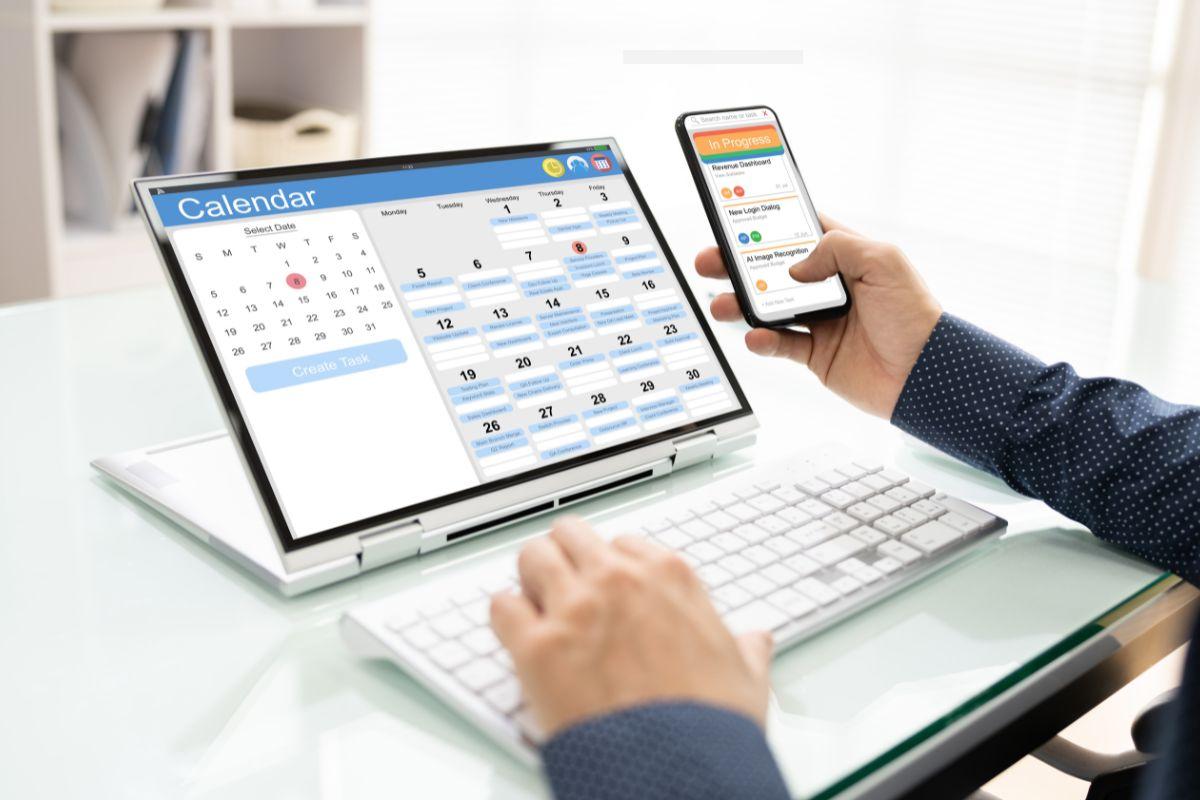
The equation for any business is simple: they use equipment to run operations and stay productive. No matter what type of equipment a company uses, it requires frequent maintenance for optimal performance and operational execution. Not doing it can be detrimental: just one hour of equipment downtime can cost $260,000.
Now can you perform maintenance of any kind without a well-defined schedule? The simple answer is no. That's why maintenance scheduling is so critical, as it helps organize and coordinate all of your maintenance activities.
Let's help you understand the significance of asset maintenance planning and how it can improve your firm’s productivity and performance.
Maintenance Schedule - An Overview
Every manager should have a robust understanding of maintenance scheduling.
It is the mechanism that ensures all of your equipment is optimized and helps you perform operations smoothly. It brings all the required resources together, helps you understand the maintenance process, and carries it out with minimal operational disruption.
Benefits of Maintenance Scheduling
After understanding what maintenance scheduling is, it's time to discuss why you should adopt it and how it benefits your firm.
1. Proactively Identifies Issues
Maintenance mostly involves minor inspections and repairs, but nobody can deny their significance. Maintenance scheduling allows you to stay ahead of time and resolve problems before they occur. Nobody wants their equipment to run sub-optimally, so why wait for that to happen?
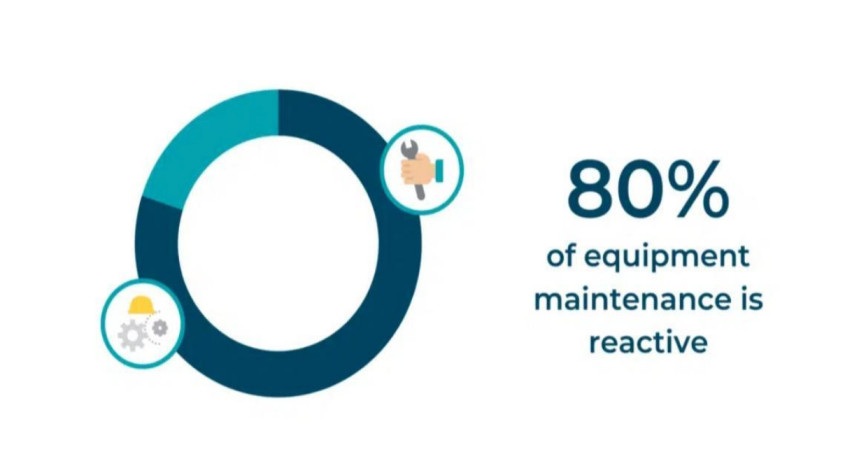
Most companies do reactive instead of proactive maintenance.
Everything from computer software to pencils has recommended life spans from its providers. Once their time is up, they should be updated or replaced. You can only do this if you have a robust maintenance schedule that keeps you on track.
2. Prevents Costly Repairs
A company is the sum of its parts, and every single part should be in perfect synchronization for operational efficiency. Maintenance services ensure that all of your equipment stays in pristine condition, so that small-scale problems don't turn into full-blown crises.
Usually, that happens when a system has been neglected for too long, mainly because there is no maintenance schedule. Instead of ordering new, expensive equipment, you can maintain the existing items and keep them running optimally till their end of life. By scheduling inspection and repair services, you can look for trouble even when it's not apparent and fix it immediately.
3. Prevents Downtime
Surprisingly, more companies are prone to downtimes than most people think. According to a report, 82% of businesses across all sectors have experienced at least one downtime outage in the last three years. With such high levels of outages, your company needs to do everything to prevent such a situation.
Thankfully, maintenance scheduling is one such tool that can be a lifesaver in this regard. By keeping an eye on the equipment, you ensure that there's zero operational disruption and downtime. The ripple effects of this intervention can be pretty significant: your teams hit their targets consistently, and your firm's overall productivity improves.
4. Increases Asset Lifespan
One stitch in time saves you nine in the long run, and that applies to your valuable assets too. Maintenance scheduling allows you to stay updated on the equipment to keep it in top shape for a very long time.
The average cost of equipment has risen sharply in recent years, so every company wants to make the most of it. Having a maintenance schedule helps extend the lifespan of your equipment because you can repair it instantly if there's any issue. No more wasted power and hefty energy bills, as your equipment will only use the energy it needs.
5. Enhances Workplace Safety
Workplace safety should be a top priority for any firm. According to the International Labour Organisation (ILO), around 2.3 million workers encounter workplace accidents each year.
When was the last time you checked your equipment, backed it up, or replaced worn-out parts that could be hazardous? If the answer isn't clear, it's time to craft a maintenance schedule that helps you keep track of everything in your inventory.
According to the National Institute for Occupational Safety and Health (NIOSH), direct contact with equipment and objects is one of the three leading causes of workplace accidents. You can avoid this situation by maintaining your equipment.
6. Better Budgeting
Running a business is never cheap, not least because you have to bear significant maintenance costs on top of everything else. But there's something even more expensive: not investing in maintenance and paying hefty sums for full-blown repairs and new equipment down the line.
That is why it is essential to have a maintenance schedule in place. It is a no-brainer for managing your finances effectively and allocating valuable resources where they are needed most. With a well-designed plan, you know when and where maintenance is required.
It enables you to set aside a nominal sum to cover maintenance costs and makes you strategic about timing. Instead of doing everything at one time, you can spread out the timeframe and costs by doing large-scale maintenance work during slower periods.
7. Improves Regulatory Compliance
From governmental regulations to industry standards, rules are rules, and you have to follow them. Not complying with them results in accidents, fines, penalties, and in rare instances, complete shutdowns. Why take that risk when you can learn about the relevant regulations and stay compliant?
One of the major requirements of any regulation is equipment maintenance, so that it meets the minimum safety standards. The American National Standards and Technical Reports contain three dozen documents detailing machine safety requirements. Similarly, there are some popular industry standards that every company must follow.
You can create a detailed equipment maintenance plan for your teams with all the critical regulatory checklists. With regular maintenance, they can cross them off as they go.
And if an audit comes knocking your way, you have detailed maintenance records. Record-keeping is critical to prove that you have followed the safety standards. As long as your maintenance schedule is aligned with regulations, you'll avoid legal headaches down the line.
8. Helps the Environment
Equipment maintenance isn't just economically beneficial for your company; it also helps the environment. When your equipment runs efficiently and for long periods, you don't have to buy new items frequently. Companies without robust maintenance scheduling end up producing more hazardous electronic and non-electronic waste.
Electricians and plumbers can quickly analyze excessive energy and water leakages. Electricity problems can become seriously dangerous if not addressed timely. Maintaining an electrical system not only keeps you safe but also prevents future repair costs.
Signs That You Need Maintenance Scheduling
Lack of maintenance scheduling can result in several discrepancies and inefficiencies. Let's discuss some signs that indicate you need a robust maintenance schedule.
1. Increasing Breakdown and Repair Costs
Physical assets deteriorate over time if you don't focus on their maintenance. It hurts their efficiency and doesn't provide the optimal output. If there is no equipment maintenance calendar, your assets will definitely suffer. It can include the following issues:
- Engineer call-outs
- Spare parts orders
- Production dips
If you're experiencing frequent breakdowns and massive repair bills, it means something is wrong with your maintenance planning. The best solution is to create a detailed maintenance plan.
2. Frequent Unplanned Downtime
Planned downtime allows your engineers to upgrade machines and replace defective parts, but unplanned downtime is a serious headache. It occurs when your equipment breaks down unexpectedly. It is a double-edged sword because it halts production and requires emergency repairs, which might not always be financially viable. If you're facing frequent unplanned downtime, finding refuge in maintenance scheduling is the best choice.
3. More Aging Assets
Aging is a natural process for any equipment since all have a limited lifespan. When an asset has reached its end of life, it's disposed of and replaced because it's too costly to repair. On the contrary, assets aging before their natural limits is a serious concern—a direct result of not scheduling maintenance.
Scheduling Maintenance: The Best Practices
Here are some of the best practices for creating a maintenance schedule.
1. Highlight Assets that Need Maintenance
The first and most important step in an asset maintenance schedule is creating a detailed asset register. This register provides instant access to valuable data and tells you which assets require maintenance. It also tells you the location of various assets, how they are being utilized, and by whom.
You can deploy modern asset management software for this purpose, which also tells you the running costs of your equipment.
2. Analyze the Current and Previous Condition
A robust maintenance plan requires detailed data on the historical and current condition of your assets. When you understand the lifecycle of an asset, you can also identify the kind of maintenance it needs for optimal performance. Following are some of the questions this analysis can answer:
- How much wear and tear has your equipment endured?
- How many operational cycles has it gone through?
- How many times has it been serviced and repaired?
3. List the Purpose of An Asset
Every asset is meant for a specific purpose that should be visible at all times. This information helps you make better decisions and lets everyone know about its significance. Providing this information is critical so that everyone knows the possible outcomes when that asset is temporarily disabled due to maintenance or replacement.
Having this data can be a game changer for any asset manager. It helps them create detailed maintenance plans, how long the process of maintenance will take, how costly the downtime will be, and much more.
4. Pick Your Maintenance Strategy
There are many maintenance strategies to choose from, including reactive, preventative, and predictive. The best strategy is the one that fits your business context, depending on various factors. It is also possible to take a particular strategy, modify it, and focus only on some of its elements.
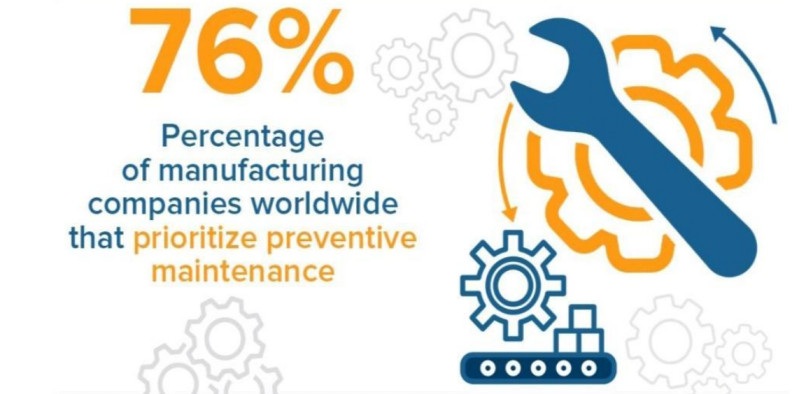
Preventive maintenance is the most popular maintenance strategy.
For instance, preventive maintenance scheduling has various types, such as time-based, usage-based, and failure-finding. A quality maintenance strategy needs the right data alongside the following:
- Quality spare parts
- A clear set of instructions
- In-house maintenance engineers or contractors
- A well-defined downtime time frame
5. Monitor Asset Performance
Once you have created a maintenance plan and started implementing it, you should consistently monitor it. Doing that will tell you whether your plan is actually working. You can divide an asset's usage into multiple periods and compare them to see the performance difference. Similarly, you can compare the maintenance costs during these periods to understand if an asset is losing its efficiency.
6. Invest in the Right Team and Technology
Maintenance schedules are excellent, but they're not good enough without technology that supports them. The right team and technicians will ensure top-notch maintenance work and keep a perfect record.
Every quality manager knows that their team needs quality training to perform well, but training goes far beyond knowing maintenance techniques. Quality training also involves educating your team about how, where, and when technology can aid its work.
What's better than a computerized maintenance management system (CMMS) for your team? It provides everything an asset manager can ask for in one place, including maintenance scheduling, asset performance tracking, and much more.
Integrating maintenance scheduling software into traditional maintenance processes reduces stress and minimizes time spent on task scheduling, data analysis, and resource allocation.
Conclusion
We have learned that maintenance scheduling and planning play a critical role for organizations in any industry. By planning maintenance, companies ensure that their assets have longer lifespans, provide optimal output, use less energy, enhance productivity, and have lower operating costs.
As mentioned, maintenance scheduling is possible only when you have robust software backing it all up. Itefy brings you its advanced Asset Management System that not only schedules your maintenance but also organizes your assets so that you can manage them with ease. It also helps you enhance asset utilization and prevents redundancy.
So, it's your time to enter a new era of maintenance scheduling. Contact us today and get a free 14-day trial before picking your favorite bundle.