What is Industrial Maintenance? Types, Benefits, and Best Practices
Industrial maintenance keeps your factory running smoothly. Learn the types, benefits and how to plan an effective maintenance strategy to save money and avoid downtime.
In this article:
- What is Industrial Maintenance?
- Types of Industrial Maintenance
- 1. Corrective/Reactive Industrial Maintenance
- 2. Predetermined Industrial Maintenance
- 3. Condition-Based Industrial Maintenance (CBM)/Predictive Maintenance
- 4. Preventive Industrial Maintenance (PM)
- Benefits of Industrial Maintenance
- 1. Extend Asset Lifespan
- 2. Lower Breakdown Risks
- 3. Improved Efficiency
- 4. Economic Lift
- 5. Security and Compliance
- Industrial Maintenance: Best Practices
- 1. Evaluate Downtime Costs With Data
- 2. Analyze and Optimize Operational Variables
- 3. Analyze the Value of Maintenance
- 4. Use Technology
- Industrial Maintenance With Itefy
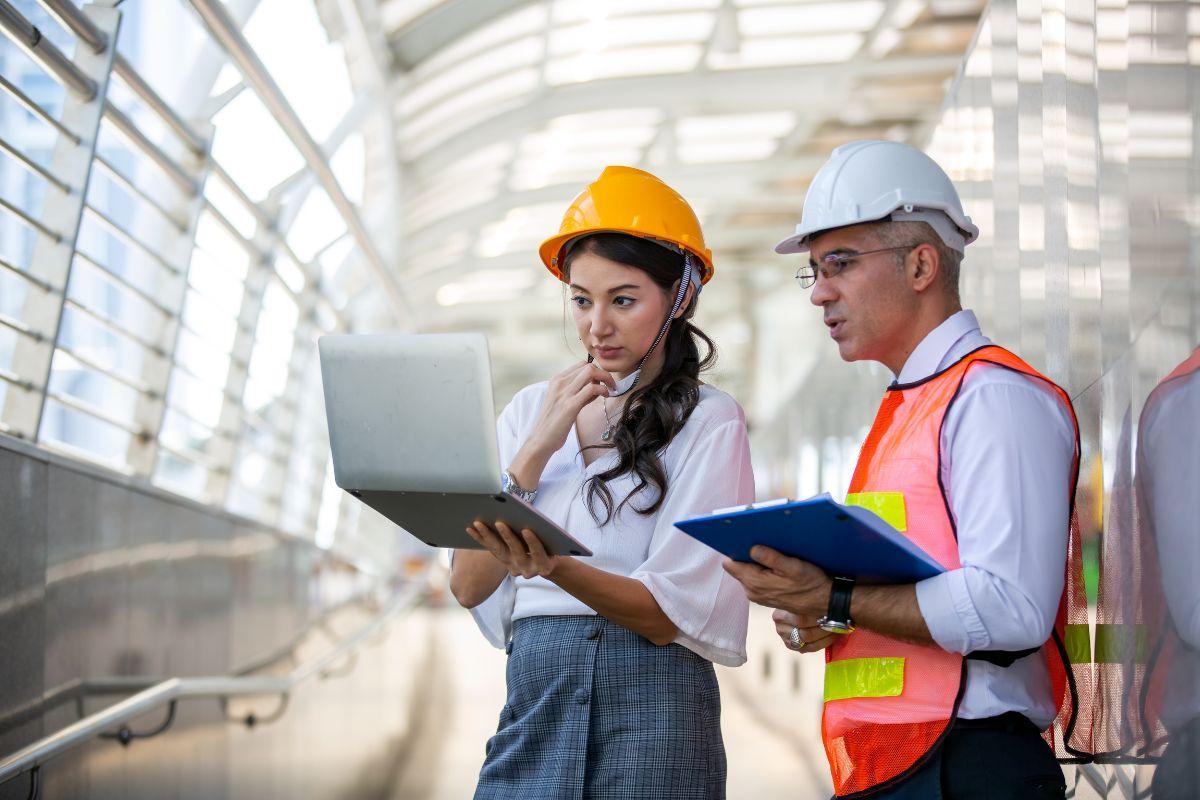
Whether small and medium enterprises (SMEs) or large conglomerates, every business understands the importance of operational efficiency and high productivity. Time is money in any industry, and asset managers know it better than anyone else. After all, regular maintenance keeps your equipment running reliably.
The question then isn't just about the significance of maintenance but also about how and when to conduct it, which is a much more complex affair. Getting it right means you save a lot of money, minimize operational disruptions, and increase productivity.
Luckily, it isn't as complicated as most people think. Once you read our detailed guide, you'll have a deep understanding of industrial maintenance.
What is Industrial Maintenance?
As the name suggests, industrial management simply refers to managing and maintaining machinery and other crucial assets for operational continuity. The concept doesn't just revolve around physical maintenance itself but also involves the analysis and strategies that help devise maintenance and management plans.
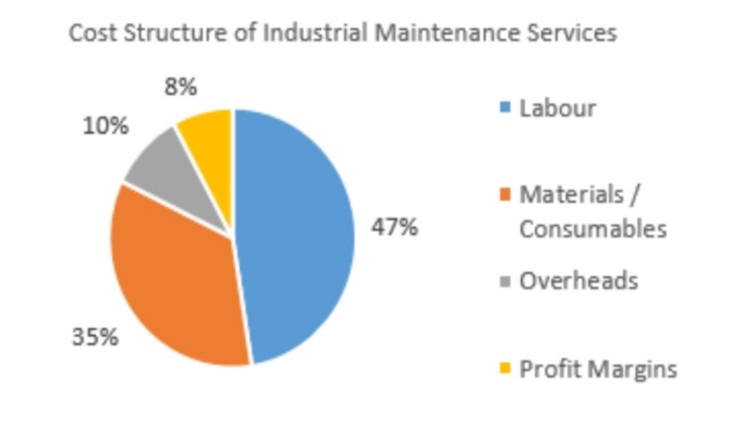
Materials/Consumables have the largest share in industrial maintenance costs.
Most companies nowadays use asset maintenance software to manage their maintenance activities because the old-school spreadsheet method is no longer efficient or practical. Its usage is increasing, as indicated by the fact that the global computerized maintenance industry will hit $1.26 billion by 2026.
A capable asset manager teams up with service specialists to develop a detailed, efficient, cost-effective, and comprehensive maintenance plan. Industrial equipment maintenance matters because its absence results in frustrating downtimes and inefficiencies when equipment fails.
By creating a comprehensive maintenance plan, you ensure that your equipment gives maximum output during working hours, reducing expenses and shutdowns and maximizing profits.
Types of Industrial Maintenance
The maintenance process you follow decides how efficient your production is. Experts have developed various types of maintenance to help manufacturers optimize their operations. Each firm has a different set of priorities and maintenance requirements, so their maintenance strategy also differs.
Let's discuss some of the major maintenance models adopted by the industry and understand how they work.
1. Corrective/Reactive Industrial Maintenance
Reactive maintenance is the maintenance methodology for rectifying and repairing faulty systems. Its purpose is to reinstall or restore systems that have stopped working. Corrective maintenance is also often called reactive or breakdown maintenance since it occurs as a reaction to a breakdown.
The need for corrective industrial maintenance and repair arises when technicians discover an additional problem during maintenance. For instance, if the technician performs emergency repairs or regular maintenance and identifies more issues, they can create a corrective maintenance order. That maintenance is scheduled for the future when the affected asset is repaired or replaced.
Benefits of Corrective Maintenance
- Minimal monthly maintenance costs.
- Less time spent on maintenance and management.
- A simpler maintenance program.
- Also focuses on non-critical assets.
2. Predetermined Industrial Maintenance
People often confuse predetermined maintenance with proactive maintenance, but there is a significant difference between the two. The former follows a plan of action created by the equipment manufacturer. Instead of creating a schedule of their own, the maintenance team or manager sticks to the manufacturer's predetermined plan.
For instance:
- The manufacturer might recommend an oil change every 4 months.
- Transmission service after X number of hours of run time.
- Check Parts A, B, and C for wear after one year.
- Replace the engine after X number of years.
One important thing to note here is that predetermined maintenance is based on timeframes and not functionality. For instance, the oil will be replaced after 4 months even if the machine is idle.
Benefits of Predetermined Maintenance
- Easier to manage and schedule.
- The plan comes from the manufacturer, so you don't have to brainstorm.
- Hire technicians temporarily instead of having a regular maintenance team.
3. Condition-Based Industrial Maintenance (CBM)/Predictive Maintenance
Condition-based maintenance is based on outcomes through measurement or observation. All machines operate within a normal range, as determined by the manufacturer. The operation of machines is acceptable within that range, but things change near the edges of that range.
In simpler words, it means that a CBM strategy examines an asset and decides whether it needs maintenance. CBM means that an asset is maintained only when specific indicators show a drop in performance.
These indicators usually include visual inspection, performance data, scheduled tests, and the like. Once the manager decides which indicators to work with, they can gather condition data continuously or at specific intervals through sensors.
A good example of CBM is an engine that suddenly uses more energy to perform at previous levels. You'll notice it in fuel tanks emptying sooner than before or sudden spikes in electrical usage.
Benefits of Condition-Based Maintenance
- Less energy consumption.
- Equipment runs in optimal ranges for longer periods.
- Swift maintenance when performance drops to ensure equipment stays in top shape.
4. Preventive Industrial Maintenance (PM)
Preventive maintenance might be the most hectic maintenance strategy but is usually the most effective. It involves routine maintenance of assets to prevent costly downtime later.
A quality preventive maintenance strategy involves a detailed record of previous inspections and services. Since industries have a large number of assets, most companies deploy asset management software to keep track of them and when to maintain them.
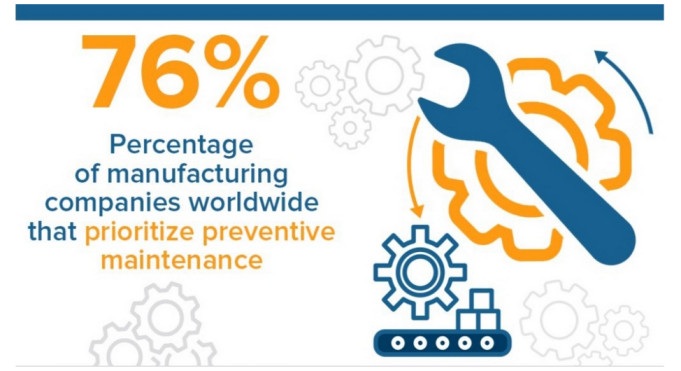
Preventive maintenance is a favorite of most companies.
Preventive maintenance is usually divided into three main types:
1. Mandatory/Non-Mandatory Tasks
Mandatory tasks, often related to safety checks, need to be dealt with as soon as they are raised. On the contrary, non-mandatory tasks are less important and can be delayed for a while without compromising safety or performance. When you create a PM checklist, divide it into mandatory and non-mandatory tasks.
2. Pyramiding / Non-Pyramiding Tasks
Pyramiding tasks occur when the scheduled maintenance on a particular date doesn't happen and overlaps with later maintenance. When it happens, the new maintenance is completed, while the previous is canceled.
The manager adds a cancellation note to explain how overdue the original maintenance is. Some companies prefer non-pyramiding techniques in which the original delayed maintenance is completely removed, and the new maintenance date is considered the baseline.
Benefits of Industrial Maintenance
Regular maintenance ensures your equipment runs efficiently, enhances productivity, and offers you peace of mind. Let's discuss the main benefits of industrial maintenance.
1. Extend Asset Lifespan
The most notable advantage of industrial maintenance is that it extends the lifespan of your assets. All kinds of machinery demand care to keep working optimally for long periods. Mean time between failures (MTBF) is a popular KPI many asset managers use to make critical maintenance decisions. Using a KPI like MTBF allows managers to catch a problem before it results in a breakdown.
2. Lower Breakdown Risks
Breakdowns can be a real barrier to productivity, which can be minimized through maintenance. In fact, most benefits of industrial maintenance are directly linked to breakdown prevention. It's important to note that breakdowns can be sudden and devastating, so you shouldn't wait for them to happen. Undo their roots by anticipating them through asset maintenance software so they don't become a significant headache.
You might be surprised to know that most industrial equipment doesn't break down because of use. Most mechanical problems that your machinery encounters can easily be controlled by preventive maintenance. If you proactively schedule your maintenance, the risk of equipment failure goes down significantly.
3. Improved Efficiency
Giving your equipment an extended lifespan means nothing if it doesn't run efficiently and consumes extensive amounts of energy. If that happens, you pay for maintenance and higher energy bills. The most common KPI used in equipment efficiency is Overall Equipment Effectiveness (OEE), which is based on three categories: availability, performance, and quality.
- Availability: The maintenance technique you adopt should ensure maximum equipment availability. Preventive maintenance is usually the top choice in this regard.
- Performance: Availability without optimal performance doesn't mean anything, so maintenance strategy should also ensure that your equipment performs well in all conditions.
- Quality: It refers to the quality of output provided by machinery. For instance, cleaning an HVAC unit's coils and air filters produces cleaner air and heats or cools more effectively.
4. Economic Lift
As an asset manager, you have two choices: let the equipment break down and pay massive costs down the line, or spend a small amount on maintenance and keep the equipment in excellent shape. If one thinks rationally, the choice seems obvious. It's not just about repair costs: breakdowns result in unplanned downtimes that hurt productivity and significant financial losses.
If your company manufactures products and sends them out regularly, downtimes could result in some unexpected costs, such as customers claiming compensation. The general loss of confidence is also extremely detrimental to your market value.
5. Security and Compliance
Regular industrial maintenance helps you stay aware of potential hazards that could endanger lives and properties. Heavy machinery could get unhinged and fall to the ground, or a broken piece from a machine might fly and hit a worker.
Workers regularly get injured while operating industrial machinery, and that's mostly because of a maintenance lapse. A robust maintenance schedule can effectively tackle many of these problems.
In the United States, the Department of Labor oversees industrial safety through its regulatory agency, the Occupational Safety and Health Administration (OSHA). It administers various penalties for violations of safety regulations.
Recently, OSHA fined a battery manufacturer in Georgia $77,200 after it found at least five safety violations. One of the most significant violations was a fire that erupted in October 2023, where several workers suffered permanent respiratory damage. Other violations included the following:
- Failure to train on-site emergency responders.
- Failure to train workers on hazardous chemicals.
- Exposing workers to inhalation hazards.
Industrial Maintenance: Best Practices
Following these principles can help any firm establish world-class maintenance strategies. They reduce operational costs and downtime and improve productivity. Let's explore them in detail here.
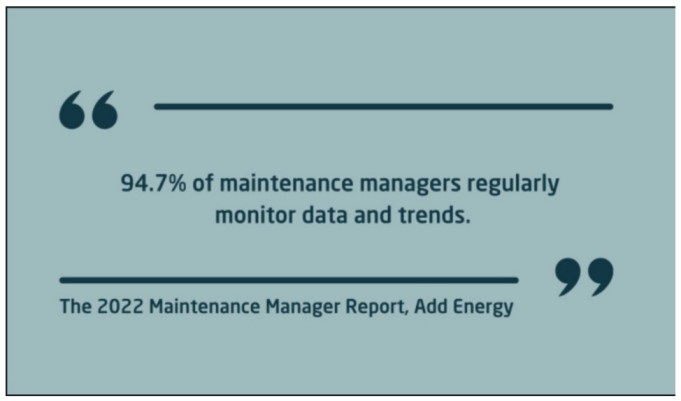
Evaluating data is one of the best industrial maintenance practices.
1. Evaluate Downtime Costs With Data
As an equipment manager, it's critical to justify the maintenance costs by showing that downtime costs are much higher. To do that, you need quality data provided by asset maintenance software, which gives you as much data as possible. The following information is the most important in this regard:
- Replacement parts costs
- The time period between machine failures
- Response time by technicians
2. Analyze and Optimize Operational Variables
Optimizing variables in your maintenance operations can save costs, and the asset manager should calculate how much. It is true that maintenance improves machine availability, but the firm can benefit even more by optimizing the mechanics of operations. Here are the things you can improve upon:
- Handling spare parts
- Work orders and flows
- Technician's response time
3. Analyze the Value of Maintenance
By determining the per-hour downtime costs, managers can easily calculate the money they save by improving maintenance. You should also calculate the productivity gains achieved through equipment availability and add them to the final analysis. Here's a simple equation to help you calculate it:
One-hour downtime = savings from cutting downtime + one-hour production
Even if you don't get a full one-hour production as a result, it'll still improve revenues.
4. Use Technology
Digital tools like the computerized maintenance monitoring system (CMMS) can help you achieve efficiency and optimization in your maintenance processes. This software helps identify opportunities to save costs.
It also provides delayed work order information to help improve technicians' response time and reduce downtime. Through CMMS, you can check the status of each asset, track critical parts, create checklists, and schedule preventive maintenance.
Here's what CMMS for industrial maintenance can also do:
- Quickly retrieves work orders and eliminates paperwork. It also shows a detailed history of asset maintenance.
- Provides faster issue management with help from detailed history.
- Give reminders when maintenance is due.
- Improves people management.
Industrial Maintenance With Itefy
Industrial maintenance is critical for various reasons: it improves productivity, helps you stay compliant, keeps workers safe, reduces downtime, and much more. Without a detailed plan, your maintenance efforts won't provide the expected results. To implement your plan, you need reliable software with all the bells and whistles.
Itefy provides a class-leading Asset Management System with features that fit the needs of any industry. Worried about equipment loss? Our System helps you track the usage and location of each asset. Want to extend equipment lifespan? We help you achieve optimal maintenance rates with robust scheduling. These and many other features help you create a stellar maintenance plan.
So, start today with a free trial and experience modern industrial maintenance like never before.