Construction Asset Management: Reduce Downtime, Increase Profits
Our detailed guide will help you level up your construction firm. Learn everything about construction asset management to minimize downtime and increase profits.
In this article:
- What is Asset Management in the Construction Industry?
- The Lifecycle of Construction Asset Management
- Major Challenges in Construction Asset Management
- 1. Stolen Assets
- 2. Invisible Assets
- 3. Broken Assets
- 4. A Lack of Replacement Parts
- Best Construction Asset Management Strategies
- 2. Maintenance and Inspection
- 3. Software Solution
- 4. Employee Training and Accountability
- 5. Predictive Analytics
- The Significance of an Asset Management Software
- 1. Location Tracking
- 2. Tracking Maintenance and Repairs
- 3. Full Lifecycle Tracking
- 4. Compliance Regulations
- Manage Your Construction Assets With Itefy
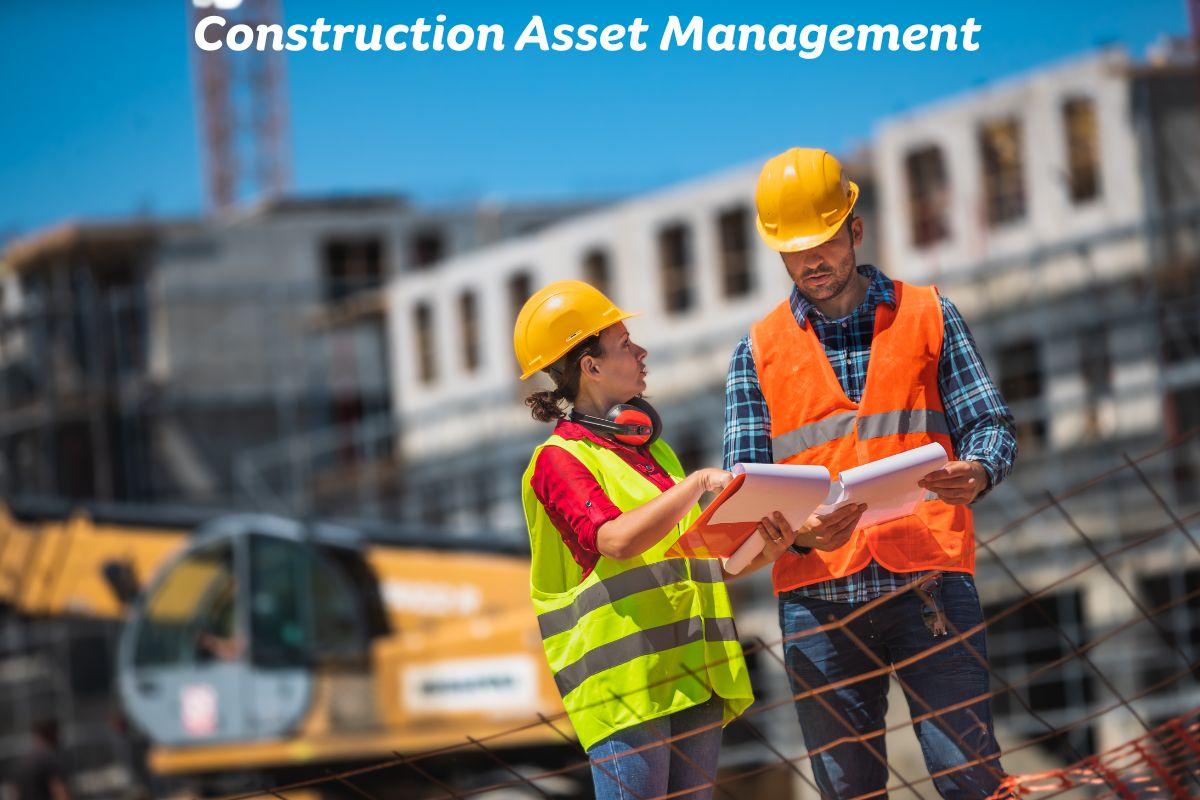
If you look at the industrial landscape today, construction is one of the areas where innovation hasn't penetrated as deeply. Even today, many construction companies rely on traditional asset management methods that result in excessive downtimes and suboptimal profit rates.
It doesn't have to be this way - you can vastly improve the productivity of your business and increase returns on investments by following effective asset management principles.
To help you improve construction equipment asset management and increase profits, we have prepared a detailed guide. Read on to discover asset management strategies and they can reduce downtimes and increase profits.
What is Asset Management in the Construction Industry?
Construction asset management refers to monitoring and managing all the assets, tools, and equipment your company uses to complete its projects. It includes everything from tagging your assets to maintenance to disposal. Using a quality asset management system gives you a clear picture of your existing inventory and the assets you may need in the future, reduces loss or theft, and ensures that your crew has the equipment they need to execute projects.
The Lifecycle of Construction Asset Management
Effective construction asset management has five interlinked stages that ensure you make the most of your assets.
- Acquisition: In this first stage, companies assess their requirements and objectives to procure assets accordingly.
- Planning: After acquisition, the next step is to plan the usage of assets. It details resource allocation, maintenance strategy and schedule, and performance targets.
- Utilization: This step involves deploying assets according to the already developed plan and tracking their performance.
- Maintenance: Maintenance involves corrective and preventative actions to ensure that your assets keep functioning reliably.
- Disposal: This stage involves getting rid of assets by disposing or replacing them. It must be done by adhering to environmental regulations and maximizing value.
Major Challenges in Construction Asset Management
Before we tell you how to manage your assets effectively, it's crucial to explore the challenges construction companies face while doing that.
1. Stolen Assets
Stolen assets are a major problem for many construction companies, according to authentic statistics. The National Insurance Crime Bureau (NICB) says that the cost of construction equipment stolen each year reaches $1 billion. To add insult to injury, most of that equipment is rented, which puts additional financial and reputational burden on the borrower.
The most commonly stolen items include copper, lumber, power tools, and even heavy machinery. The rate of recovery is just 25%, so if your equipment gets stolen, you're more likely not to see it ever again. Surprisingly, heavy machinery is targeted by thieves because it's usually not well secured. Not keeping detailed records and a lack of standardized identification numbers make matters even worse.
2. Invisible Assets
It's not always thieves that are the problem. Sometimes you just cannot find an asset, even when it isn't stolen. It hurts productivity, which is why construction asset tracking should be at the top of the list for any equipment manager.
Construction equipment keeps moving from one location to the other, as that's the nature of this work. Sometimes the manager might not locate an asset and end up purchasing it again, only to find out later that they had it in their inventory all along.
3. Broken Assets
Construction is one of those industries where equipment goes through some serious grind, so breakdowns are common. Managers must have a holistic picture of everything from maintenance to repairs to costs to prevent spending extensive amounts on maintenance. The managers who don't do preventive maintenance are the ones who end up spending obscene amounts on repairs and replacements.
4. A Lack of Replacement Parts
Replacement parts are an essential element of any maintenance and management strategy. Managers deal with two kinds of scenarios here:
- Assets that are prone to frequent breakdowns.
- Parts of assets that break down.
In both scenarios, managers need quick replacement to minimize downtimes and disruption to projects. And for that, managers need to have a thorough understanding of the most common problems to arrange replacements.
Best Construction Asset Management Strategies
Managing construction assets becomes much more efficient and reliable if you follow the right protocols. It requires a multi-pronged approach, the elements of which we'll discuss below.
1. Asset Tagging
A good start for your asset management system is to tag each item with unique identifying tools, taking them from complete anonymity to being trackable assets. Thankfully, several asset tagging technologies are available today, and you can pick one that fits your budget and preferences.
- Barcode: Barcodes are one of the most popular and effective tagging options available today. It requires a scanner to capture the unique identifier. Although it's a reliable and well-tested method, it can get a bit hectic if you have a lot of equipment.
- RFID (Radio Frequency Identification): This is a modern technology that uses radio waves to monitor assets. It is known for improving efficiency in operations because of its contactless scanning. Just waving the reader by a tool can easily capture the unique identifier, unlike barcode scanning where you need to align it perfectly with the barcode.
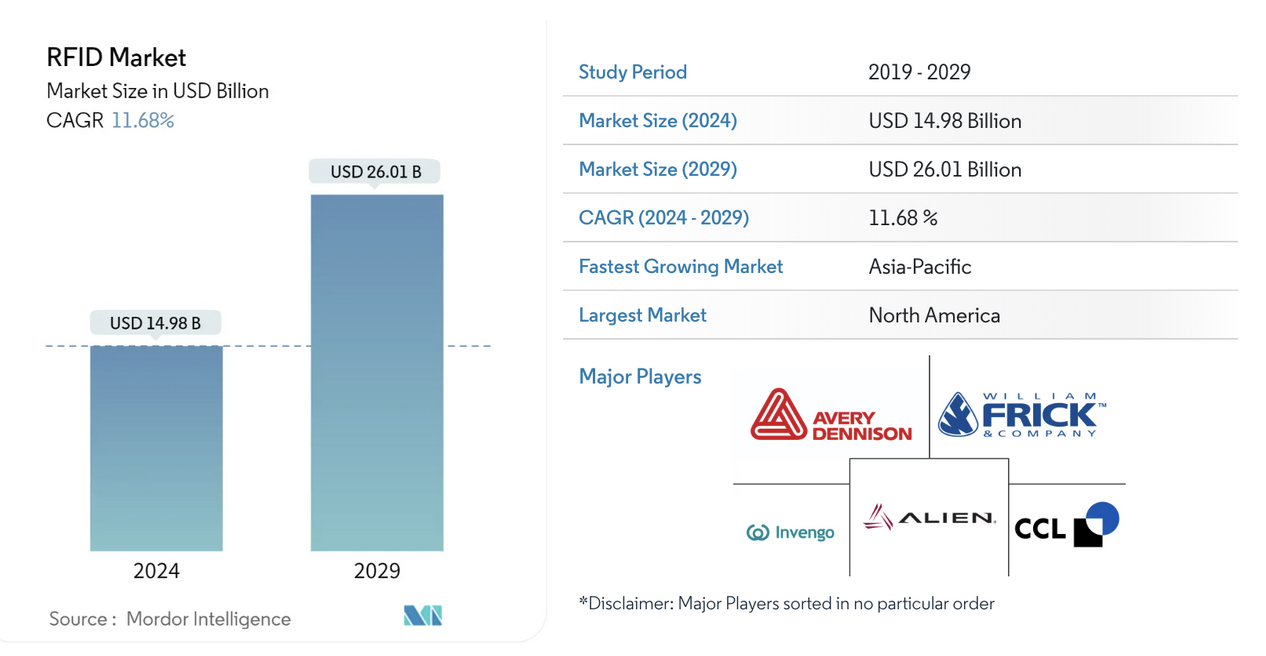
RFID’s market size is growing rapidly
2. Maintenance and Inspection
Preventative maintenance should be an integral part of any asset management strategy, more so in the construction industry. It helps prolong the lifespan of your assets, minimizes downtime, and enhances your profit rates in the long run. Customization is the most critical aspect, which involves creating a schedule for regular tool inspection, cleaning, and lubrication.
For instance, power tools that perform heavy-duty work are more prone to dust build-up, which can negatively affect their performance. They must be cleaned regularly with a cleaning brush to keep them performing optimally. On the contrary, hand tools don't have as much dust build-up, but they do require periodic sharpening and lubrication.
1. Crew Training
Remember that your crew is critical to identify potential issues before they become full-blown problems. You should craft a comprehensive training program in which they're taught to recognize signs of wear and tear, such as malfunctioning buttons, blunt blades, misfiring power tools, and the like. Most downtimes are a direct result of companies not identifying issues beforehand, but crew training can definitely resolve this problem.
2. Technological Solution for Maintenance
Implementing advanced building asset management software can help you keep track of a tool’s maintenance history, notifying you of upcoming service schedules. Pick software that sends automatic notifications for preventive maintenance so that none of your tools gets neglected.
3. Software Solution
Gone are the days when construction companies had to rely on spreadsheets and unreliable memory to keep track of their assets. Construction asset management software has put to rest all of those worries by offering a modern and unique solution, changing how you manage and use your tools.
- Asset management software can be accessed on multiple devices, including smartphones, allowing your crew to update data directly from the job site. No need to fill up tons of manual datasheets and waste precious time.
- The software solution should integrate seamlessly with existing hardware. RFID readers and barcode scanners act as an extension of your crew, ensuring a swift check-in/check-out process for your equipment. It prevents errors that occur through manual data entry and ensures your data is always up to date for effective maintenance.
4. Employee Training and Accountability
Construction asset management should be a top priority for an asset manager, but it isn't possible without their crew's backing. You need a well-trained and accountable crew to help maintain your assets, extend their lifespans, and ensure that problems are controlled before they become too much to handle.
Train your employees in the following areas:
- Using and caring for tools, including cleaning methods required for different tools.
- Check-in and check-out procedures through software and mobile apps.
- Reporting procedures for damaged or underperforming tools. It should also include daily reports on malfunctions workers notice during work.
- Focus on tool security to minimize losses. Encourage crew members to take ownership of the tools and use them in a way that minimizes damage.
It's not just technical skills that matter here. Building a culture of accountability among your employees is equally critical to ensuring optimal usage of tools and loss minimization. Train their employees to think of these tools as their own and assign them to teams or individual employees to foster a sense of ownership.
5. Predictive Analytics
Asset management software has become advanced to the point where it can predict failure using tool usage and maintenance data. It can be incredibly helpful in reducing downtimes at key moments of any project. It is also useful in maintaining safety standards and preventing potential hazards caused by breakdowns. The software notifies you about the tools approaching their end of life, so that the crew can timely replace them and there is no hindrance to productivity.
The analytics provided by the software are also helpful in optimizing the budget and critically allocating resources for maintenance. For instance, the tools that you use most often during construction projects can be flagged for more frequent maintenance to maximize their lifespan.
The Significance of an Asset Management Software
Technology has advanced to the point where construction asset management is incomplete and frankly unthinkable without quality software. Sure, you can use the old-school spreadsheets and manual paperwork, but do you actually want to go through the hassle?
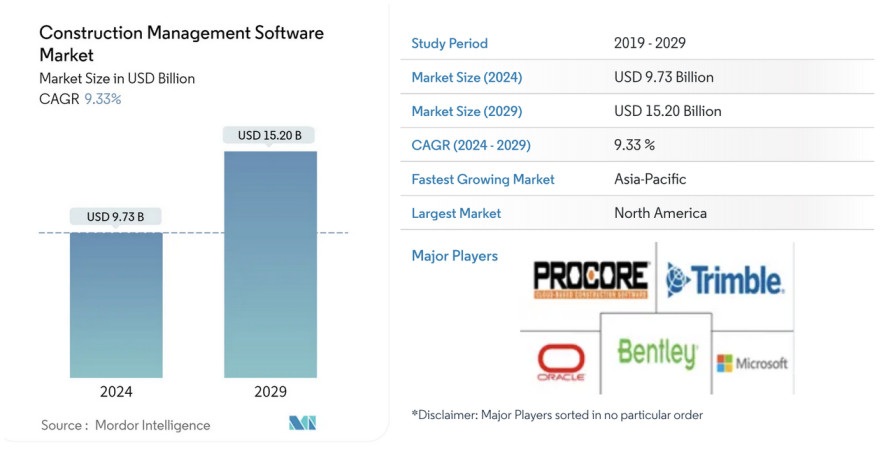
The construction asset management software market is expecting significant expansion.
An asset management software does all the tracking, integration, and analysis you want to keep your assets in optimal condition. When integrated into the workflow, the asset management software gives you a holistic picture of your assets, including their current and future condition.
Let's discuss some essential features of quality asset management software:
1. Location Tracking
Equipment is always on the move in the construction industry, so the software you deploy must have GPS-enabled location-tracking capabilities. You can simply attach trackers to your equipment or vehicles and the software will keep you updated about their location.
2. Tracking Maintenance and Repairs
It's almost impossible to manage maintenance for every single item in your inventory manually. That's why asset management software is indispensable for scheduling maintenance. It notifies you whenever an asset needs maintenance based on the manufacturer's recommendations or specific usage data. It also assigns maintenance jobs to qualified technicians, ensuring optimal maintenance and repair of your equipment.
3. Full Lifecycle Tracking
One of the best features of quality asset management software is that it tracks the whole lifecycle of an asset, starting from its acquisition to consistent depreciation to the ultimate disposal, showing you its lifetime costs. It also helps predict the lifetime of your assets through borrowing time, number of breakages, and related metrics.
4. Compliance Regulations
Equipment maintenance isn't just about ensuring optimal performance and maximum profits. It's also closely linked to compliance regulations regarding safety and other standards. If you don't maintain your equipment, it stays unsafe and can potentially harm workers. The Department of Labor’s Occupational Safety and Health Administration (OSHA) imposed fines of $201,000 on a construction company last year for repeatedly flouting workplace safety regulations, resulting in the death of a 24-year-old worker.
Asset management software makes compliance tracking much easier for your company. You have all the legal documents in a single place, where you can cross-check your internal reports to ensure your company is following rules and regulations.
Manage Your Construction Assets With Itefy
Understandably, any construction company wants to maximize profits. That's possible only when downtimes are kept to a minimum through robust asset management and maintenance.
The best way to do that is by using Itefy's Asset Management System. Our advanced solution for construction asset management allows companies to not only prevent equipment loss and extend its lifespan but also provides valuable insights into your existing inventory. With regular condition tracking, you know your assets need maintenance beforehand, resulting in minimal downtimes.
So, let's help you with building asset management with a no-limits 14-day trial, after which you can pick a bundle that fits your needs.